Activate the Manufacturing Program and click Profile Contouring
in the Prismatic Machining Operations toolbar.
A Profile Contouring entity is added to the Manufacturing Program. The Profile Contouring dialog box appears
directly at the Geometry tab
.
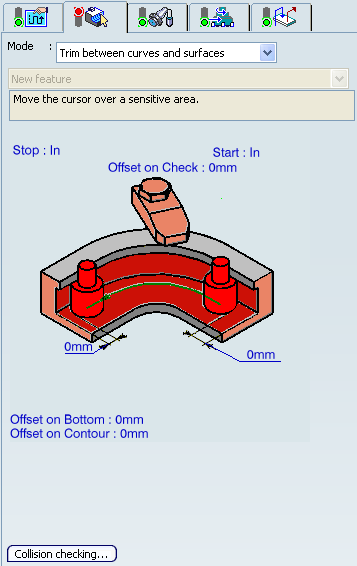
The top guiding curve and part bottom
in the icon are colored red indicating that this geometry
is required for defining the operation. All other geometry
is optional.
Still in the Geometry tab:
See Selecting Geometry
- Set the Contouring mode to
Trim between curves and surfaces.
- Click the red bottom in the icon,
then select the bottom surface of the part in the authoring window.
- Click top guiding curve in the
icon, then select the top edge of the part in the authoring window.
- Click the first relimiting element
in the icon, then select a vertical edge at one end
of the part in the authoring window.
- Click the second relimiting element
in the icon, then select the vertical edge at the other
end of the part in the authoring window.
- If needed, set offset on the geometric
elements.
The guide and limit elements of
the icon are now colored green indicating that this
geometry is now defined. These are also indicated on
the part.
Note:
A Collision Checking
capability is available in the Geometry tab,
which allows collision checking between the tool and
guide elements during macro motions.

Select the Strategy tab
.
- Choose the desired Tool path style.
- Set the machining criteria.
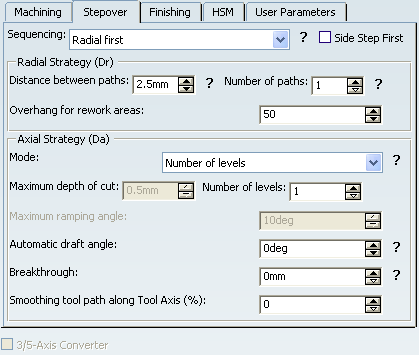
Note:
The 3/5-Axis Converter
is not supported and is disabled.
Go to the Tool tab
and select a T- Slotter tool with a diameter of 30mm.
See Specifying a Tool Element in a Machining Operation
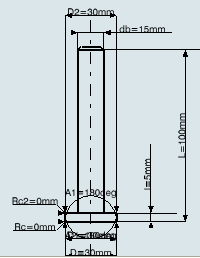
Note:
- The difference in cutting part between Z and -Z orientation is not supported properly.
- RC and RC2 must have same value.
Select the Feeds and Speeds
tab
to specify the feedrates
and spindle speeds for the operation.
Select the Macro tab
to add approach and retract motions to the operation.
Note:
When macros are used, the surface
selected as bottom is checked for collisions.
See Defining Macros on Milling Operations
Note:
- We recommend that you define the horizontal motion first
, to avoid collision with the undercut.
- The axial motions
are defined according to the tool axis defined in the machining operation.
- The ramping motion
, helix motion
, and add tool axis motion
are not supported.
Click Tool Path Replay
to check the validity of the operation.
See Replaying the Tool Path
- The tool path is computed.
- A progress indicator is displayed.
- You can cancel the tool path computation at any moment before 100%
completion.
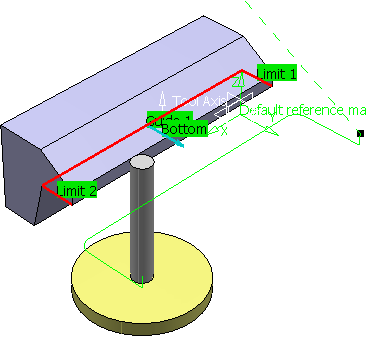
Click OK to create the
operation.