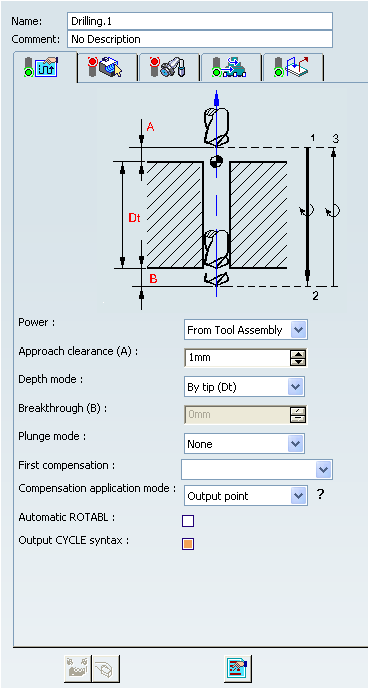
Machining Strategy Parameters
Note:
Since the position of those parameters varies in the different dialog box, they are listed in alphabetical order.
- Power
- Specifies power option for the operation.
There are
different Power values for different operations under a single tool
change. You can output this Power syntax in the APT source for the
operation and use this output in setting up the machine, to use the full potential of multi-task drill
tool holders, and effectively improve productivity and
performance: The options in the
Power dropdown combo box are as follows:
- From Tool Assembly: The Power value defined in the
tool assembly is taken into consideration for that operation.
- Fixed: This value is specific to the
operation and there is no impact of the Power value chosen
for tool assembly.
- Powered: This value is specific to the
operation and there is no impact of the Power value chosen
for tool assembly.
Note:
The Power parameter value is editable for the following axial operations:
- Drilling,
- Spot Drilling,
- Drilling Dwell Delay,
- Drilling Deep Hole,
- Drilling Break Chips,
- Tapping,
- Reverse Threading,
- Thread without
Tap Head,
- Boring,
- Boring and Chamfering,
- Reaming,
- Counter Boring,
- Counter Sinking,
- Chamfering Two Sides,
- Sequential
Axial.
Since the tool
motion is not purely axial for these operations (meaning Powered cannot be set to Fixed), Power is set to Powered and is not editable for the following operations:
- Boring
Spindle Stop,
- Back Boring,
- T-Slotting,
- Circular Milling,
- Thread
Milling,
- Sequential Groove.
At the Tool Assembly level, you can
select Fixed or Powered for the following operations:
- Boring Spindle Stop,
- Back
Boring,
- T-Slotting,
- Circular Milling,
- Thread Milling,
- Sequential Groove.
- Approach clearance (A)
- Specifies a safety distance along the tool axis for approaching
the hole reference.
- Approach clearance 2 (A2)
- Defines a safety distance
along the tool axis for approaching the chamfering or back boring
pass.
This is available for Boring and Chamfering, Chamfering Two Sides, and
Back Boring operations.
- Automatic draft angle
- Specifies the draft angle to be applied on the circular
flank between the top and bottom of the hole.
This is available for Circular Milling, for Standard Machining mode
only.
- Automatic ROTABL
- When selected, generates rotation motions between drilling
points that have different tool axes.
- This capability works with a 3-axis milling machine with
rotary table when ROTABL/ output is requested.
- Rotary motions are displayed during replay.
- Facilitates environment setup by minimizing the requirement
on post processors (avoids having to deal with X, Y, Z, I, J,
K outputs for rotary tables).
-
Provides the NC programmer with a more accurate tool path simulation
for machine tools with rotary table.
Note:
No rotary motion is performed if a linking macro motion
is defined (and activated) on the drilling operation. If activated,
the linking macro is always performed between the points to
machine.
- Axial mode
- The options in the
Axial mode dropdown combo box specifies how the distance between two consecutive levels
is computed.
The options are:
- Maximum depth of cut (Mdc)
Defines the maximum depth of cut in an axial strategy.
- Number of levels
Defines the number of levels to be machined in an axial
strategy.
- Number of levels without top.
- Available for Circular Milling (Standard Machining mode only)
- Breakthrough (B)
- Specifies the distance in the tool axis direction that the tool
goes completely through the part.
- Compensation application mode
- The options in the
Compensation application mode dropdown combo box specifies how the corrector type specified on the tool (P1,
P2, P3, for example) is used to define the position of the tool.
The options are:
- Output point: the tool compensation point
is generated in the output file. The tool path computation
is done according to the tool tip.
- Guiding point: the tool motion is computed
according to the tool compensation point and the tool compensation
point is generated in the output file.
Note:
The tool compensation point is defined on the tool
and used on the operation. The Compensation application mode defines the tool position to reach.
- Compensation output
- The options in the
Compensation output dropdown combo box manage the generation of Cutter compensation
(CUTCOM) instructions in the NC data output.
The options are:
- None: Cutter compensation instructions are
not automatically generated in the NC data output. However,
CUTCOM instructions can be inserted manually. In this case,
refer to Procedure for Generating CUTCOM Syntaxes .
- 2D radial profile: Both the tool tip and
cutter profile can be visualized during tool path replay.
Cutter compensation instructions are automatically generated
in the NC data output. An approach macro must be defined
to allow the compensation to be applied.
- 2D radial tip: The tool tip can be visualized
during tool path replay. Cutter compensation instructions
are automatically generated in the NC data output. An approach
macro must be defined to allow the compensation to be applied.
- Available for Circular Milling, for Standard Machining mode
only.
- First compensation
- Specifies the first tool compensation number for the operation.
- Second compensation
- Specifies the second tool compensation number
for the operation. Available for Boring and Chamfering and Chamfering Two Sides operations.
- Decrement limit
- Specifies the coefficient used to determine the maximum allowed depth of cut
for a peck in a Drilling Deephole operation. The depth of a new peck never becomes smaller than the Maximum
depth of cut multiplied by the Decrement limit i.e. Depth of current peck > Maximum depth of cut * Decrement limit
When Depth of current peck = Maximum depth of cut * Decrement limit,
this depth is kept for all remaining pecks until the total depth
is reached. Example: A Drilling Deephole operation uses the following parameters:
- Maximum depth of cut = 10mm
- Decrement rate = 0.1
- Decrement limit = 0.8
Therefore, depth of current peck is always greater than
8mm (that is, 10mm*0.8):
- Depth of peck 1 = 10mm
- Depth of peck 2 = 9mm
- Depth of peck 3 = 8mm
- Depth of remaining pecks = 8mm
Note:
The value of Decrement limit must be greater than zero.
- Decrement rate
- In
a Drilling Deephole operation, decreases the
effective depth of cut at each new peck until the total depth
is reached:
- Depth of peck 1 = Max depth of cut (Dc)
- Depth of peck 2 = Dc * (1-Decrement rate)
- Depth of peck 3 = Dc * (1-2*Decrement rate)
and so on.
Note:
If Decrement rate is equal to zero, the Max depth of cut (Dc) is applied at each new peck as a constant step.
- Depth mode
- The options in the
Depth mode dropdown combo box describe how the depth computation is done, depending on the type of operation.
The options are:
- tool tip,
- shoulder,
- diameter
- or a distance value.
- Direction of cut
- The options in the
Direction of cut dropdown combo box are as follows:
- Climb milling: the front of the advancing
tool (in the machining direction) cuts into the material
first
- Conventional milling: the rear of the advancing
tool (in the machining direction) cuts into the material
first.
- Available for Circular Milling and T-Slotting.
- Distance between paths (Dp)
- Specifies the maximum distance between two consecutive tool paths
in a radial strategy (for both Standard and Helical Machining modes). Available for Circular Milling.
- Dwell mode
- The options in the
Dwell mode dropdown combo box are as follows:
- None
- By revolutions: specifies the number of revolutions
for the dwell
- By time units: specifies the time duration of the
dwell.
- Helix mode
-
The options in the
Helix mode dropdown combo box specifies how the helix computation is to be done (for Helical Machining mode only), and are as follows:
- Pitch (P): Specifies the helix pitch
- Angle (Ang): Specifies the helix angle.
- Available for Circular Milling.
- Machining mode
The options in the
Machining mode dropdown combo box are as follows:
- Standard
- Helical
- Available for Circular Milling.
Note:
Helical interpolation instructions can be generated in
the output file (APT source and Clfile) for helical tool motions.
- Machining Strategy
- The options in the
Machining Strategy dropdown combo box specifies how the tool is computed, and are as follows:
- Mono-pass (default value)
Machining motion is done in one pass. Tool is considered
as a mono-cutting level tool.
- Optimized passesThis strategy is useful for thread mill tool (more than
one cutting level exists on the tool). It is not available
when a boring bar is used.
Tool path depends on the tool characteristics and thread
depth.
One or more helical (height = pitch) tool paths can be generated:
the number of helical tool paths depends on the effective
thread length of the tool and the thread depth of the hole.
- Available in Thread Milling.
Note:
- Regarding thread mills and effective thread length: Length1 depends on Cutting length (Lc) and Taper
angle (Ach). See
Tool Resources for Milling and Drilling for geometry parameters.
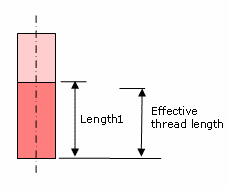
- Cutting levels on the tool is the number of thread
pitches that can be machined during one helical motion.
The number of cutting levels is defined as follows:
- Number of effective cutting levels = int (Length 1 /
tool pitch)
- Effective thread length = number of cutting levels *
pitch.
- Between helical tool paths:
- Approach macro motion is done before each helical motion
- Retract macro motion is done after each helical motion
The following figure illustrates the motion involved for
2 helical tool paths.
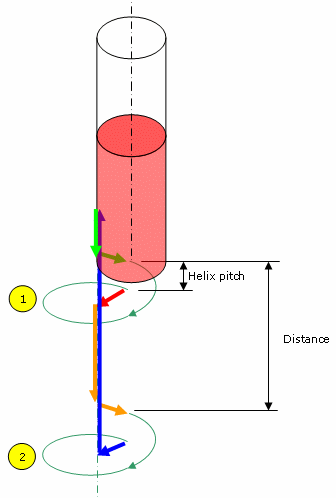
Key to colors and arrows in this figure:
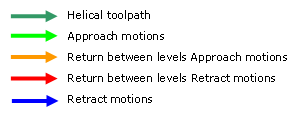
The helical tool path is done for one helix pitch height. The distance is defined from start of one helix motion
to next start of next helix motion. (Distance = effective thread length of the tool + pitch.)
The figures below illustrate the various combinations depending
on tool type, tool's effective thread length, thread depth of
hole, machining strategy, machining direction
- Thread mill, Machining strategy=Optimized passes, Machining
direction=Top to Bottom:
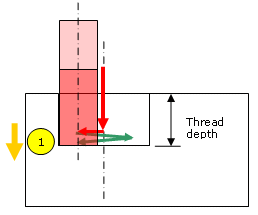
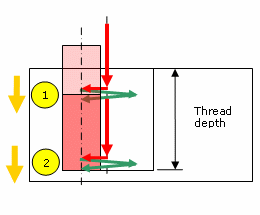
- Thread mill, Machining strategy = Optimized passes, Machining
direction = Bottom to Top:
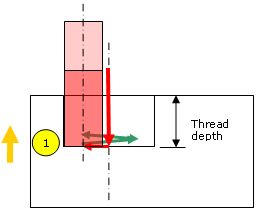
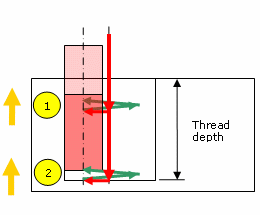
- Thread mill or Boring bar, Machining strategy = Mono-pass,
machining direction = Top to Bottom:
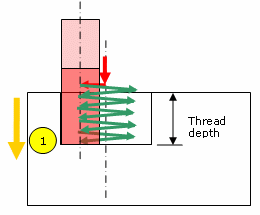
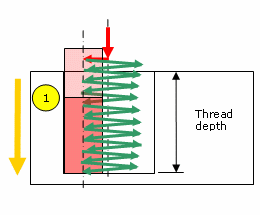
- Thread mill or Boring bar, Machining strategy = Mono-pass,
Machining direction = Bottom to Top:
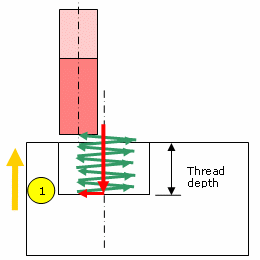
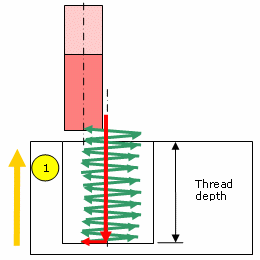
- Machining tolerance
-
- Specifies the maximum allowed distance between the theoretical
and computed tool path.
- Available for Circular Milling and Thread Milling.
- Max depth of cut (Dc)
- Specifies the maximum depth of cut for:
- Each peck in a Drilling Deephole operation
- Each break chips pass in a Drilling Break Chips operation.
- Number of paths (Np)
-
Specifies the number of tool paths in a radial strategy (Available for Circular Milling, for both Standard and Helical Machining modes).
- Output CYCLE syntax
- When selected, generates the output in
CYCLE mode.
- to generate CYCLE statements, select the Output CYCLE syntax check box and set the
NC Data Options option to Yes in the NC Output Generation
dialog box.
- Otherwise, GOTO statements is generated.
Note:
when several axis orientations are present in a
machining pattern, output of the components of the tool axis
orientation is possible whenever the NC data format is set to
Axis (X, Y, Z, I, J, K) in the Part Operation's
Tool Resources for Milling and Drilling.
- Percentage overlap
- Specifies the percentage overlap (Available for Circular Milling, for both Standard and
Helical Machining modes).
- Plunge for chamfering
- if a Plunge mode
is selected (By tip or By diameter), you can deactivate the
plunge motion for the chamfering phase of the operation by deselecting
the Plunge for chamfering check box. In this case,
the plunge motion is done for the boring phase only.
- Available for Boring and Chamfering operations.
- Plunge diameter (Pd)
- Specifies the plunge diameter value.
- Plunge mode
- The options in the
Plunge mode dropdown combo box specifies an axial plunge from the hole reference at plunge
feedrate prior to machining, and are as follows:
- None,
- By tip,
- By diameter.
Note:
The overall plunge distance is determined as follows:
Approach clearance + (Plunge depth - Plunge
offset)
where Plunge depth is determined by a tool tip or tool diameter
value.
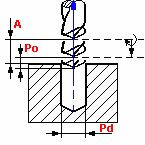
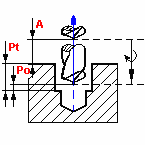
- Plunge offset (Po)
- Specifies
the plunge offset value.
- Plunge tip (Pt)
- Specifies the plunge tip distance.
- Retract
- Specifies the retract clearance after the machining pass in a
Back Boring operation.
- Retract offset (Or)
- Specifies
the value of
- The back motion used to break chips after each drilling pass in a Drilling Break Chips operation.
- The offset where machining feedrate starts before each new peck in a Drilling Deephole operation.
- Sequencing mode
- The options in the
Sequencing mode dropdown combo box specifies the order in which machining is to be done, and are as follows:
- Axial first:axial machining is done first then
radial
- Radial first: radial machining is done first then
axial.
- Available for Circular Milling (Standard Machining mode only)
- Shift mode
-
The options in the
Shift mode dropdown combo box are used to offset the tool just before retracting, and are as follows:
- None
- By linear coordinates, with:
- Shift along X
- Shift along Y
- Shift along Z
- By polar coordinates
with:
- Shift distance
- Shift angle
The values entered for the selected shift mode determine
the angle at which the active part of the boring bar stops and
the amount of the tool displacement.
For a shift defined by polar coordinates
(90deg, 1.5mm), the tool is displaced 1.5mm as indicated by
the arrow in the figure below.
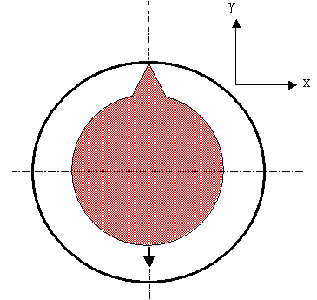
The same shift motion could
be obtained by the linear coordinates
(0mm, 1.5mm, 0mm).
- Spring pass
- Available for Circular Milling and Thread Milling, indicates whether or not a spring pass is to be done at the
same location as the last pass. The spring pass is used to compensate
the natural 'spring' of the tool and improve the surface finish.

GeometryFor 2.5-axis operations, the program automatically manages
holes at different levels using horizontal transition paths.
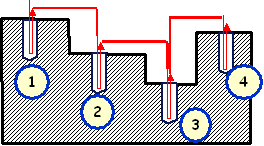
The Geometry tab lets you select the required geometry and parameters. Note:
The look of the tab varies with the operation used.
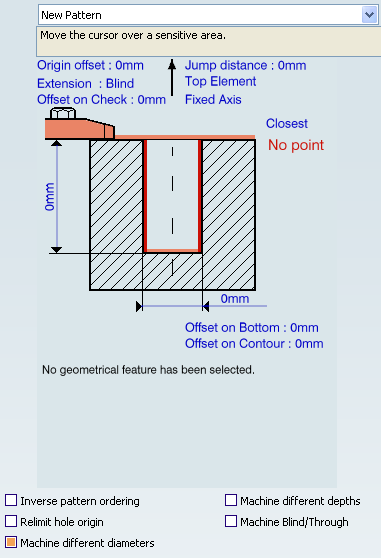
- Origin Offset
- Specifies an Origin
Offset in order to shift the entire tool path by the specified
amount.
- Extension: Blind/Through
- Manages the type of the hole.
- Jump Distance
- Allows an
extra clearance for moving in Rapid motion between the
holes to be drilled whenever this distance is greater than the
approach clearance.
For example, for an approach clearance of 2.5mm and a jump distance
of 10mm, the extra clearance is 7.5mm.
- Top Element/Projection
- Projection mode.
The reference pattern points are projected onto the selected
part surface. The projected points and the axes normal to the
surface define the hole positions to be drilled.
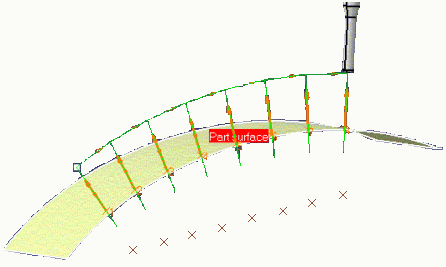
- Top Element mode.
The reference pattern points define the hole positions to be
drilled. The machining depth takes into account the normal distance
between the reference points and the selected part surface.
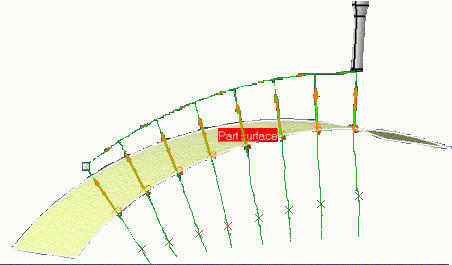
- Inverse Pattern Ordering
- Allows an operation to locally override the ordering of
the machining pattern by inverting it.
This option is useful in the following cases:
- When machining symmetrical parts. Refer to
Effect of Reverse Machining Conditions.
- To save machining time when managing two operations
sharing the same machining pattern on a large part. The
first operation can be set to machine from the first position
to the last one, and the second operation can be set machine
from the last position to the first one.
- Relimit Hole Origins
- The Relimit hole origin and Machine different
depths check boxes can be used together to manage the
machining strategy of different design hole configurations. In the following figures the red star (
)
represents the origin of the selected design hole, and the green
star ( )
represents the start of the tool path:
- Relimit hole origin Off, Machine different
depthsOff
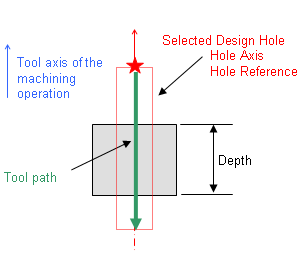
- Relimit hole origin Off, Machine different
depthsOn
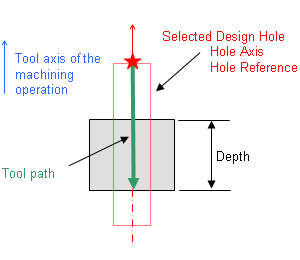
- Relimit hole origin On, Machine different
depthsOff
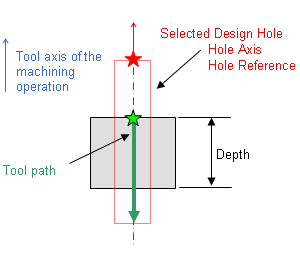
- Relimit hole origin On, Machine different
depthsOn
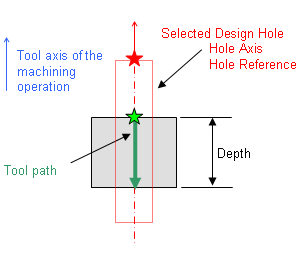
- Machine different diameters
- Lets you machine different hole diameters in a Circular Milling operation:
- If selected, the diameter specified for each position of
the machining pattern is machined.
- Otherwise, the diameter of the first position of the machining
pattern is used for all the pattern holes.
- Machine different depths
- When dealing with
design feature holes in design patterns, both the result and
specification mode are taken into account (except for Spot Drilling,
Counterboring, and Countersinking operations).
- When selected, the Machine different depths check box manages automatically different
depths of holes in a pattern (result mode).
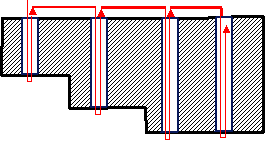
- When cleared, the program uses the values specified in the Geometry
tab for the pattern holes (specification mode).
Note:
- For Threading operations,
select the Machine different thread depths check
box when you want the program to take the real thread depth
of each selected pattern hole into account.
- Different thread depths can be applied only when information
exists on the geometry linked to the machined position. For
example, thread information exists on a threaded design hole
but none exists for a circular edge. When no thread information
exists on the geometry linked to the machined position, the
depth defined on the operation is used.
- Machine Blind/Through
- If selected, the blind/through characteristic of the hole
is determined for each position of the machining pattern.
- If not selected, the blind/through characteristic of the
first position of the machining pattern is used for all the
pattern holes.
Note:
The Machine
Blind/Through capability is not available for user features.
- Bottom Plane
- If a bottom plane is selected,
the machining depth is the distance between the hole origin
and its projection on the bottom plane. This machining depth
is computed for each hole in the machining pattern. The depth shown in the geometry dialog box is the machining depth
computed for the first hole. The Machine different depths
setting is ignored when a bottom plane is selected.

Machining
PatternsA machining pattern comprises two sets of data:
- Patten geometry: hole positions/axes, top element
- Pattern usage or technology data: ordering mode,
jump distance, local entry/exit distances, local depth,
activate/deactivate status.
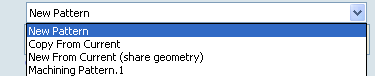
- New Pattern
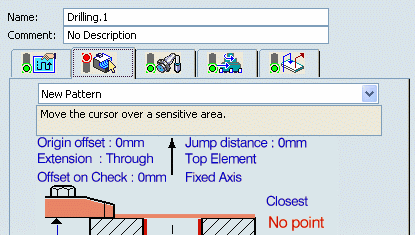 Prompts you to create
a machining pattern for the operation by clicking
the sensitive text (No Point or x Points) and selecting
one of the existing patterns displayed in a dialog box and/or select geometry in the authoring window to define the hole positions.Note:
The new machining pattern is created when you create the
machining operation. The pattern geometry and technology data
is stored and the new pattern is assigned an identifier
Machining Pattern.x
If there are already machining patterns on previous operations,
the list allows a quick selection of an existing pattern. If
selected, the existing pattern is shared between the operations.
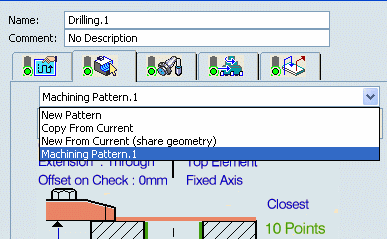
- Copy from Current: The machining pattern (geometry
and technology data) is duplicated. The pattern cannot be shared.
It is possible to modify the machining data in the current machining
operation without impacting other operations.
- New from Current (share geometry): The machining
pattern (geometry and technology data) is duplicated. The pattern
can be shared. If the pattern is modified, all operations using
it can be impacted.
- New Pattern: A new machining pattern is created
with the geometry and technology data that you specify.
Note:
- Modification of a machining pattern is possible using the
Machining Pattern editor only. This editor can be opened by
double-clicking the machining pattern in the manufacturing view.
Refer to
Creating a Machining Pattern on Machinable Features for more information.
- It is possible to reference in a machining pattern
one or more 3D Wireframe features (that is, Projection, Symmetry,
Rotation and Translation operators) containing at least one
point.

Pattern Ordering Modes
Holes that are selected for a machining pattern can be
ordered using the contextual menu in the dialog box:
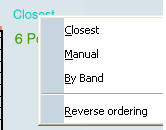
- Closest: to obtain the shortest possible tool
path,
- Manual: to obtain a numbered sequence defined by you,
- By Band: a Band Ordering dialog box
appears allowing you to obtain a Zig Zag or One Way ordering
in bands with a width defined by you.
An example of Zig Zag ordering of a pattern of
40 points for a band width of 18mm is illustrated below:

An example of One Way ordering of the same points
and same band width is illustrated below:
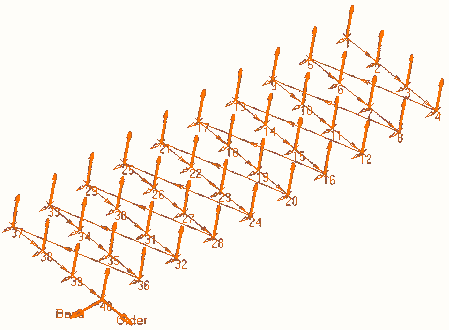
- Reverse Ordering
- Reverses the numbered sequence
of pattern points (for example, points numbered 1 thru 10 can
be numbered 10 thru 1).

NC MacrosYou can define transition paths in your machining operations by means
of NC macros:
- Approach: to approach the operation start point,
- Retract: to retract from the operation end point,
- Linking: to link points of a pattern,
- Clearance: to define the feedrate
on the horizontal path between two machining positions.
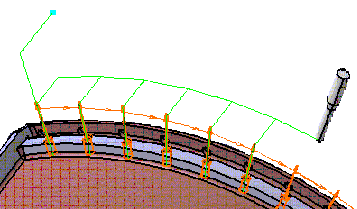
All types of macros used in Drilling
operations are collision checked. If a check element is specified
between two machined positions, a linking macro is applied to
avoid collisions. Check (or fixture) elements as well as an
associated Offset on Check can be specified in the
Geometry tab.
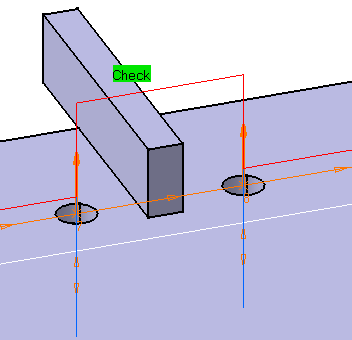
Some specific axial machining operations support additional
macro types:
- Global approach and Global retract (Circular Milling
and Thread Milling):
- The Approach macro is used to approach each drilled point
in the pattern,
- The Global approach macro is used in
the approach of the first drilled point only.
- For the first
point, the Global approach is added before the Approach
macro.
- Similarly, the Retract macro is used to retract from each
drilled point, and the Global retract macro is used in the
retract from the last drilled point only. For the last point,
the Global retract is added after the Retract macro.
- Return between levels (predefined macro in Circular
Milling in Standard Machining mode only, which is used link
two consecutive levels). A special feature of this macro
is the capability to specify a feedrate value on the approach
motion between levels.
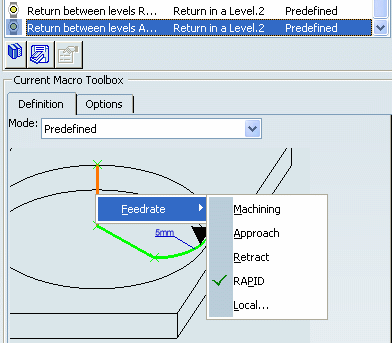
- Return in a level (predefined macro in Circular Milling
in Standard Machining mode only, which is used to link two
consecutive paths in a given level).
For all axial operations, Edit Cycle
in the dialog boxes allows
you to:
- Display the unresolved syntax of the NC Instruction
of the operation. This is the syntax as specified in the
PP table referenced by the current Part Operation.
- Display and, if needed, modify the syntax that is resolved
either by geometric selection and user entries.
See Defining Macros and Inserting PP Instructions
|