Machining Operation |
Effect of Reverse Machining Conditions |
Prismatic Roughing |
Climb and Conventional options are inverted |
Profile Contouring |
Climb and Conventional options are inverted
Order of multi-contours is inverted.
Start and End elements, offsets are
inverted |
Facing |
Climb and Conventional options are inverted |
Pocketing |
Climb and Conventional options are inverted |
Plunge Milling |
Nothing to reverse |
4-Axis Pocketing |
Climb and Conventional options are inverted |
All Axial Maching Operations |
Order of pattern points is inverted |
Tslotting |
Climb and Conventional options are inverted |
Circular Milling |
Climb and Conventional options are inverted Order of pattern points is inverted |
Sequential Axial |
Order of pattern points is inverted |
Slot Milling |
Climb and Conventional options are inverted |
Groove Milling |
Climb and Conventional options are inverted
Inversion of Geometry points |
Sequential Groove |
Climb and Conventional options are inverted for circular and helical
motion |
Thread Milling |
Order of pattern points is inverted |
CUTCOM |
You should check that the desired cutter compensation
is still applied (correct side, and so on). |
Roughing |
Climb and Conventional options are inverted. |
Cavities Roughing |
Climb and Conventional options are inverted |
Sweep Roughing |
Start direction is inverted |
Power Machining |
Climb and Conventional options are inverted |
Advanced Finishing |
Climb and Conventional options are inverted |
Contour Driven |
Tool Path is inverted |
4-Axis Curve Sweeping |
Start direction is inverted |
Sweeping |
Tool Path is inverted |
Pencil Machining |
Climb and Conventional options are inverted |
Zlevel |
Climb and Conventional options are inverted |
Spiral Milling |
Climb and Conventional options are inverted. |
Isoparamametric machining Operations |
Order of parts is inverted.
Corners 1 and 2 are swapped.
Corners 3 and 4 are swapped.
Corresponding interpolation axes at corners are swapped. |
Multi-Axis Isoparametric Machining |
Pole points are inverted |
Multi-Axis Sweeping |
Start direction is inverted |
Multi-Axis Contour Driven |
Start direction is inverted |
Multi-Axis Spiral Milling |
Climb and Conventional options are inverted |
Multi-Axis Tube Machining |
Way of cut (clockwise/counter) is inverted |
Multi-Axis Helix machining |
Climb and Conventional options are inverted |
Multi-Axis Curve Machining |
Climb and Conventional options are inverted Geometry points are inverted Sign of Tilt angle is changed to invert the left/right condition
Couple of Points limit elements are swapped.For Tangent Axis
guidance along isoparametric lines:
when machining a strip of drive surfaces, check that the reference
tool axis gives the desired result for the best matching u or v
isoparametric line of the first machined face. |
Multi-Pockets Flank Contouring |
Climb and Conventional options are inverted |
Multi-Axis Flank Contouring |
Geometry parameters are inverted |
Multi-axis Flank Contouring |
Climb and Conventional options are inverted Order of drives is inverted as follows when the
Close tool path check box is not selected.
Drives A, B, C, D are machined in the order D, C, B, A.
- Before Opposite Hand Machining:
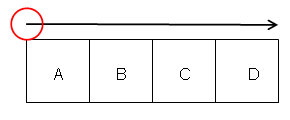
- After Opposite Hand Machining:
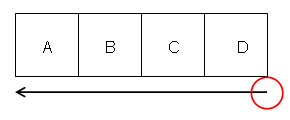
Order of drives is inverted as follows when the Close tool
path check box is selected.
Drives A, B, C, D are machined in the order A, D, C, B, A.
Drive A is the first and last machined element.
- Before Opposite Hand Machining:
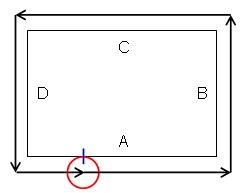
-
After Opposite Hand Machining:
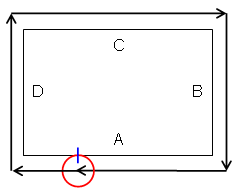
Start and End elements, offsets, and conditions are inverted.
Approach and Leave distances are swapped.
Manual direction is inverted (Left / Right).
Local stopping condition and Local restarting direction are updated.
|