Activate the Manufacturing Program and click Groove Milling
in the Prismatic Machining Operations toolbar.
A Groove Milling entity is added to the Manufacturing Program.
The Groove Milling dialog box appears directly at the
Geometry tab
. This tab includes a sensitive icon to
help you specify the
geometry.
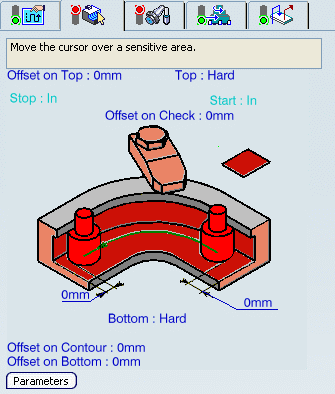
The top plane, groove bottom, and flank
guiding element in the icon are
colored red indicating that this geometry is required for defining the
operation. All other geometry is optional.
Still in the Geometry tab, select the required geometry.
See Selecting Geometry
- Click the red bottom in the icon, then select the bottom
of the groove in the authoring window.
- Click the red top in the icon, then select the top of the
groove in the authoring window.
- Click the red guiding element in the icon, then select
the flank contour of the groove in the authoring window.
- Right-click Start to set this condition to
Out. Click the first relimiting element in the icon, then
select the horizontal edge at one end of the contour profile in the authoring window. Set Offset on Limit1 to 5mm.
- Right-click Stop to set this condition to Out. Click the second relimiting element in the icon, then select
the horizontal edge at the other end of the contour profile in the authoring window.
Set the Offset on Limit2 to 5mm.
Note:
- Right-click the bottom element and make sure the Contour Detection contextual
command is not selected. If Contour Detection is set, the boundary of the selected face is
proposed automatically as guiding contour.
- A Collision Checking capability is
available in the Geometry tab, which allows collision checking
between the tool and guide elements during macro motions.
The bottom, guide, limit, and check elements of the
icon are now colored green indicating that this geometry is now defined.
These are also indicated on the part.
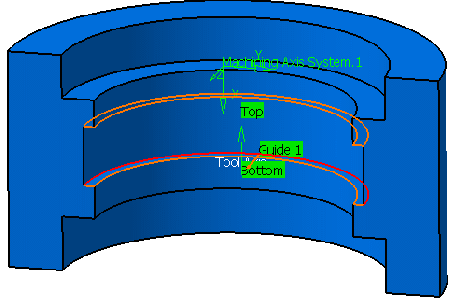
Select the Strategy tab
.
- Choose the desired Tool path style: Zig zag or One way.
- Set the machining criteria, strategy parameters, radial and axial stepover conditions, finishing, and user parameters.
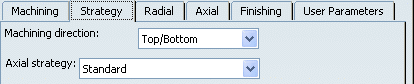
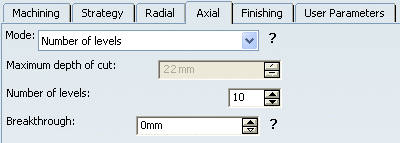
Go to the Tool tab
to select a tool.
See Specifying a Tool Element in a Machining Operation
Select the Feeds and Speeds
tab
to specify the feedrates
and spindle speeds for the operation.
Select the Macro tab to optimize this macro and add approach and retract
macros to the operation
See Defining Macros on Milling Operations
Click Tool Path Replay
to check the validity of the operation.
See Replaying the Tool Path
- The tool path is computed.
- A progress indicator is displayed.
- You can cancel the tool path computation at any moment before 100%
completion.
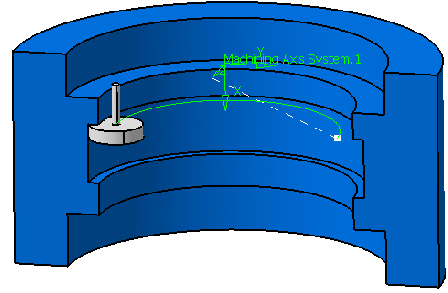
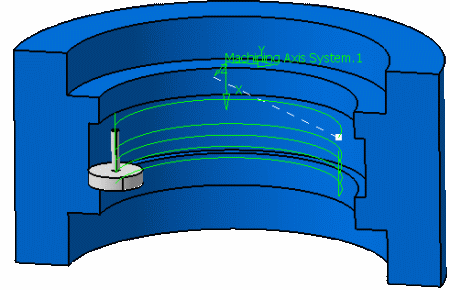
By default,
Return
between levels macro is used in the specified operation to allow switching compensation points for machining
upper and lower levels of the groove.
Click OK to create the operation.