Activate the Manufacturing Program and click
Circular Milling
in the Axial Machining Operations toolbar.
A Circular Milling entity is
added to the Manufacturing Program.
The Circular Milling dialog box appears directly at the
Geometry tab
. This tab includes a sensitive icon to
help you specify the
geometry.
Areas of the icon are colored red indicating that this
geometry is required.
Still in the Geometry tab:
See Selecting Geometry
- Enter Offset values for the Bottom and
Contour, if required.
- Select the red hole depth representation then select hole
geometry in the authoring window. Double-click to end your selections.
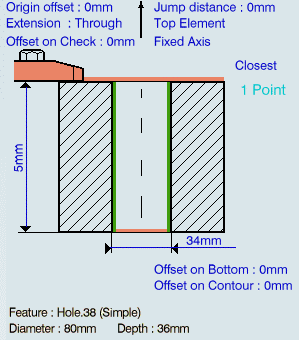
- Select the axis representation in the sensitive icon to invert the tool axis direction, if required.
Select the Strategy tab
.
- Choose the Machining mode: Standard or Helical.
- Specify the machining strategy parameters.
The following are common to both
machining modes:
- Approach clearance (A)
- Plunge mode
- Machining tolerance
- Direction of cut
- Percentage overlap
- Compensation number depending on those available on the tool
- Compensation application mode: Output point or Guiding point
- Compensation output, which allows you to manage the generation of Cutter compensation (CUTCOM) instructions in the NC data output.
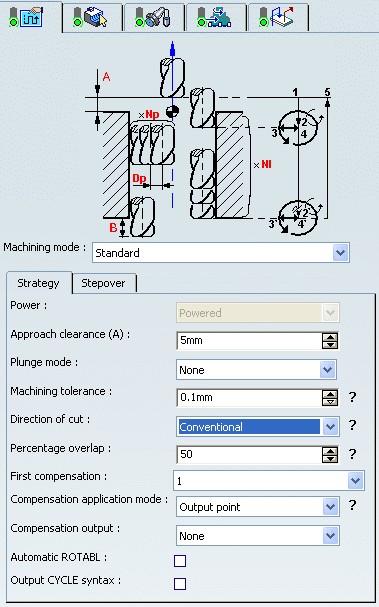
The Stepover parameters when Machining mode is Standard:
- Breakthrough (B)
- Distance between paths (Dp) and Number of paths (Np)
- Axial mode: Maximum depth of cut or Number of levels (with or
without top)
- Sequencing mode: Axial first or Radial first
- Automatic draft angle.
- Spring pass
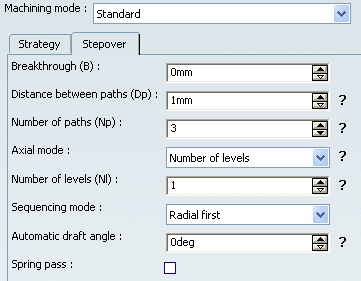
The Stepover parameters when Machining mode is Helical:
- Breakthrough (B)
- Distance between paths (Dp) and Number of paths (Np)
- Helix mode: By angle or By pitch
- Angle (Ang) or Pitch (P) value.
- Spring pass
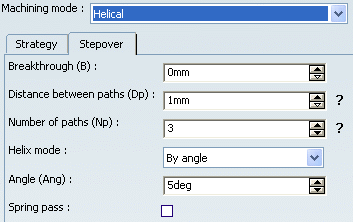
Go to the Tool tab
to select a tool.
See Specifying a Tool Element in a Machining Operation
You can use any of the following tool types:
- End Mill
- Face Mill
- Conical Mill
- Drill
- Spot Drill
- Countersink
- T-slotter
Select the Feeds and Speeds
tab
to specify the feedrates
and spindle speeds for the operation.
Note:
In the tool path represented in the Strategy tab, tool motion is at:
- Motion at machining feedrate from 1 to 2
- Motion at feedrates defined on macros from 2 to 3, 3 to 4, 4 to
2', 2' to 3' and 3' to 4'
- Retract at retract feedrate from 4' to 5.
Select the Macro tab
to add approach and retract motions to the operation.
See Defining Macros on Axial Machining Operations
- Select Predefined Helix to insert a helix approach macro
The Predefined-Helix mode is available for approach macro and the return between level approach
macro in Standard machining mode.
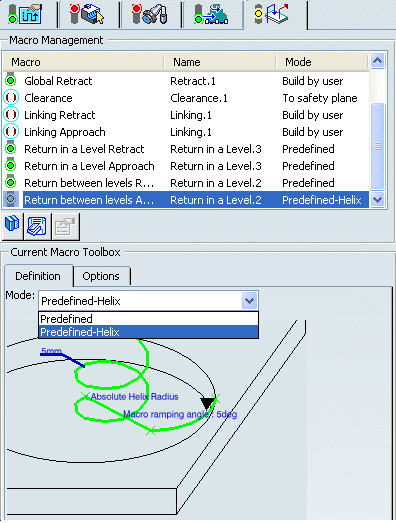
The sketch below the mode changes to Helix motion.
- Double-click Helix Radius (5mm) on the manipulator.
The Edit Parameter dialog box appears and allows you to change the radius value.
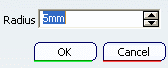
- Double-click Macro Ramping Angle on the manipulator.
The Edit Parameter dialog box comes and allows you to change the macro ramping angle value.
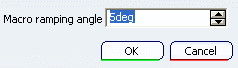
- Double-click Absolute Helix Radius on the manipulator, or click Parameter in the contextual
menu.
The following dialog box appears and allows you to change the value.
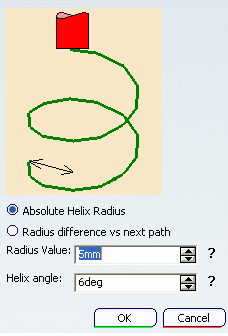
- Click the manipulator to change the radius state can be changed from Absolute Helix Radius to Radius difference vs next path.
- Right-click an arc of helix manipulator and select the Feedrate type from the contextual menu.
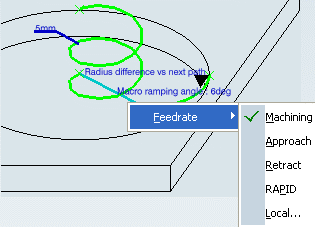
Click Tool Path Replay
to check the validity of the operation.
See Replaying the Tool Path
- The tool path is computed.
- A progress indicator is displayed.
- You can cancel the tool path computation at any moment before 100%
completion.
Click OK to create the operation.
Note:
If your PP table is customized with the following statement for
Circular Milling operations:
CYCLE/CIRCULARMILLING, %MFG_TOTAL_DEPTH,
%MFG_FEED_MACH_VALUE,&MFG_FEED_UNIT, %MFG_CLEAR_TIP
A typical NC data output is as follows:
CYCLE/CIRCULARMILLING, 38.500000, 500.000000, MMPM, 2.500000
The parameters available for PP word syntaxes for this type of
operation are described in the NC_CIRCULAR_MILLING section of the Manufacturing
Infrastructure User's Guide.
Click Edit Cycle
to edit or choose output syntaxes.