PP Word Tables
You can create and manage Post-Processor word tables within Machine Programming.
Default Values
Some NC commands and NC instructions have default values.
The example below shows an NC command with explicit definition:
*START_NC_COMMAND NC_CHANGE_REF_PT
SWITCH/%MFG_QUADRANT
*END
If this output is not required, you must define an empty NC command or
NC instruction. For example:
*START_NC_COMMAND NC_CHANGE_REF_PT
*END
TPRINT and NOTEPRINT and NOTE are automatically included in the lists of major words
with parameters and minor words respectively, even if they are not specifically
declared in the PP word table.

NC Commands
For a given machine tool (i.e. post-processor), you can define PP word
syntaxes associated to particular NC commands.
A NC command is a machine function such as a feedrate declaration (NC_FEEDRATE)
or a spindle activation (NC_SPINDLE_START).
A syntax comprises a major word and one or more syntax elements such
as minor words, numerical values, lists and parameters.
A syntax that includes lists or parameters is a parameterized syntax.
Parameterized SyntaxThis is an example of parameterized syntax
*START_NC_COMMAND NC_COMPENSATION
LOADTL/%MFG_TL_NUMBER,%MFG_TOOL_COMP
*END Notes:
- The & character indicates a list and the % character
indicates a parameter.
- A list has a finite number of values.
- You can define
only one syntax for each NC command.
The examples below show how lists can be used to define units for feeds
and speeds.
- Example: Defining Inch Units for Feeds and Speeds
*START_NC_COMMAND
NC_FEEDRATE
*START_LIST MFG_FEED_UNIT
IPM ,IPR
*END
FEDRAT/%MFG_FEED_VALUE,&MFG_FEED_UNIT
*END
/
*START_NC_COMMAND NC_SPINDLE_START
*START_LIST MFG_SPNDL_UNIT
RPM ,SFM
*END
SPINDL/%MFG_SPNDL_SPEED,&MFG_SPNDL_UNIT,&MFG_SPNDL_WAY
*END
/
*START_NC_COMMAND NC_SPINDLE_LATHE
*START_LIST MFG_SPNDL_UNIT
RPM ,SFM
*END
SPINDL/%MFG_SPNDL_SPEED,&MFG_SPNDL_UNIT
*END
- Example: Defining Metric Units for Feeds and Speeds
*START_NC_COMMAND
NC_FEEDRATE
*START_LIST MFG_FEED_UNIT
MMPM ,MMPR
*END
FEDRAT/%MFG_FEED_VALUE,&MFG_FEED_UNIT
*END
/
*START_NC_COMMAND NC_SPINDLE_START
*START_LIST MFG_SPNDL_UNIT
RPM ,SMM
*END
SPINDL/%MFG_SPNDL_SPEED,&MFG_SPNDL_UNIT,&MFG_SPNDL_WAY
*END
/
*START_NC_COMMAND NC_SPINDLE_LATHE
*START_LIST MFG_SPNDL_UNIT
RPM ,SMM
*END
SPINDL/%MFG_SPNDL_SPEED,&MFG_SPNDL_UNIT
*END
For an example of how to define syntaxes in NC commands, refer to
Define PP Word Syntax.
Arithmetic OperatorsYou can use the following arithmetic operators in PP word syntaxes:
- addition (+)
- subtraction (-)
- multiplication (*)
- division (/).
These operators can be used:
- between word syntaxes (for example, %MFG_xxx + %MFG_yyy)
- between a value and a word syntax (for example, n + %MFG_yyy)
- between a word syntax and a value (for example, %MFG_xxx + n)
- between values (for example, n + m).
Parenthesis are not needed in expressions: they can be ignored and cannot appear in NC data output. For example: WORD/%MFG_aaa, %MFG_xxx + %MFG_yyy, %MFG_bbb/2
Operators are processed in the order they appear in the syntax: the example below means that %MFG_xxx is added to %MFG_yyy, then this sum is multiplied
by %MFG_zzz. %MFG_xxx + %MFG_yyy * %MFG_zzz
Note:
Avoid using the +, -, *, / characters for other meanings.
For example, use an underscore (_) instead of a dash (-) in the
following expression to avoid any ambiguity: PPRINT/DIAMETER-VALUE, %MFG_NOMINAL_DIAM
Other NC CommandsNote:
Parameters listed under a context have to be used in the same context
(where it makes sense) and should not be extended to other contexts.
NC Commands |
Comments |
NC_AXIS_LOCK |
Allows blocking a linear or rotary axis. See Displacing and Locking Linear and Rotary Axes. |
MFG_AXIS_LOCK_STATUS |
Defines the lock status of the NC axis. |
MFG_NCAXIS_NAME |
Defines the name of NC axis. |
NC_AXIS_MOVE |
Allows linear displacement. See Displacing and Locking Linear and Rotary Axes. |
MFG_NCAXIS_NAME |
Defines the name of the NC axis. |
MFG_AXIS_POSITION |
Defines the position of the NC axis |
NC_CHANGE_REF_PT |
Defines the tool compensation corresponding to the desired tool
output point. |
MFG_QUADRANT |
Defines the number of the compensation type (for example, 2 for compensation
type P2). |
MFG_NOSE_RADIUS |
Defines the insert nose radius. |
MFG_TL_SET_X |
Defines the tool assembly set length in x direction. |
MFG_TL_SET_Y |
Defines the tool assembly set length in y direction. |
MFG_TL_SET_Z |
Defines the tool assembly set length in z direction. |
MFG_LGTH_COR_REG, MFG_TOOL_COMP MFG_TL_COMP |
Define the number of the correction
register. |
By default,
the syntax is:
SWITCH/% MFG_QUADRANT Syntax example for turning operations:
SWITCH/%MFG_TL_COMP,%MFG_QUADRANT,INCR,%MFG_TL_SET_X,
%MFG_TL_SET_Z,%MFG_NOSE_RADIUS
NC Commands |
Comments |
NC_COMMENT |
|
MFG_MO_COMMENT |
Defines the comment on the Machining Operation. |
By default,
the syntax is
% MFG_MO_COMMENT
NC Commands |
Comments |
NC_COMPENSATION |
|
MFG_TOOL_COMP MFG_TL_COMP |
Specifies the length number of current corrector. |
MFG_TL_COMP_RAD |
Defines the tool compensation radius. |
MFG_TL_NUMBER |
Defines the tool number associated to the compensation. |
MFG_TL_NAME |
Defines the name of tool associated to the compensation. |
By default,
the syntax is
LOADTL/% MFG_TL_NUMBER ,%MFG_TL_COMP
NC Commands |
Comments |
NC_CUTCOM_ON |
The syntax of this NC command is CUTCOM/ON and cannot be parameterized.
|
NC_CUTCOM_OFF |
The syntax of this NC command is CUTCOM/OFF and cannot be parameterized. |
NC_CUTCOM_NORMDS_ON |
The syntax of this NC command is CUTCOM/SAME, NORMDS and cannot be parameterized. |
NC_CUTCOM_NORMDS_OFF |
The syntax of this NC command is CUTCOM/OFF and cannot be parameterized. |
NC_CUTCOM_NORMPS_ON |
The syntax of this NC command is CUTCOM/NORMPS and cannot be parameterized.
|
NC_CUTCOM_NORMPS_OFF |
The syntax of this NC command is CUTCOM/OFF and cannot be parameterized. |
NC_CUTCOM_LEFT |
The syntax of this NC command is CUTCOM/LEFT and cannot be parameterized. |
NC_CUTCOM_RIGHT |
The syntax of this NC command is CUTCOM/RIGHT and cannot be parameterized. |
NC Commands |
Comments |
NC_DELAY |
|
MFG_DELAY_UNIT |
Defines the delay units from two values:
- First value: delay expressed in number of revolutions.
By default,
the value is REV.
- Second value: delay expressed in seconds.
By default,
the value is a blank string (represented by 8 underscore characters). When the statement is generated by the application this string is ignored.
|
MFG_DELAY_VALUE |
Defines the numerical value of the delay. |
By default,
the syntax is
DELAY/%MFG_DELAY_VALUE,&MFG_DELAY_UNIT
NC Commands |
Comments |
NC_FEEDRATE |
|
MFG_FEED_UNIT |
Defines the feedrate unit. This is done from a list with two values:
- First value: feedrate expressed in model units per minute.
By default,
the value is MMPM
- Second value: feedrate expressed in model units per revolution.
By default,
the value is MMPR
|
MFG_FEED_VALUE |
Defines the numerical value of the feedrate. |
By default,
the syntax is
FEDRAT/% MFG_FEED_VALUE,&MFG_FEED_UNIT
NC Commands |
Comments |
NC_MACHINING_AXIS |
|
MFG_NCAXIS_IDENTIFIER |
See Displacing and Locking Linear and Rotary Axes Defines the NC-Axis identifiers, as the name of the Manufacturing Program for the first output,
otherwise as the name of the machining axis change. |
MFG_SPINDLE_NAME |
Defines the name of the spindle that is linked to the origin. |
MFG_SPINDLE_NUMBER |
Defines the number of the spindle that is linked to the origin. |
MFG_NCAXIS_X_ORIG MFG_NCAXIS_Y_ORIG MFG_NCAXIS_Z_ORIG |
Defines the coordinates of
the machining axis origin. |
MFG_NCAXIS_X_VECX MFG_NCAXIS_Y_VECX MFG_NCAXIS_Z_VECX |
Defines the components of the
x-axis. |
MFG_NCAXIS_X_VECY MFG_NCAXIS_Y_VECY MFG_NCAXIS_Z_VECY |
Defines the components of the
y-axis. |
MFG_NCAXIS_X_VECZ MFG_NCAXIS_Y_VECZ MFG_NCAXIS_Z_VECZ |
Defines the components of the
z-axis. |
By default,
the syntax is
$$*CATIA0
$$ %MFG_NCAXIS_IDENTIFIER
$$ %MFG_NCAXIS_X_VECX %MFG_NCAXIS_X_VECY %MFG_NCAXIS_X_VECZ
%MFG_NCAXIS_X_ORIG
$$ %MFG_NCAXIS_Y_VECX %MFG_NCAXIS_Y_VECY
%MFG_NCAXIS_Y_VECZ
%MFG_NCAXIS_Y_ORIG
$$ %MFG_NCAXIS_Z_VECX %MFG_NCAXIS_Z_VECY %MFG_NCAXIS_Z_VECZ
%MFG_NCAXIS_Z_ORIG
NC Commands |
Comments |
NC_MULTAX_ON |
The syntax of this NC command is MULTAX and cannot be parameterized.
|
NC_MULTAX_OFF |
The syntax of this NC command is MULTAX/OFF and cannot be parameterized. |
NC Commands |
Comments |
NC_PITCH |
|
MFG_THREAD_PITCH |
Defines the thread pitch. |
MFG_NUM_THREADS |
Defines the number of threads. |
Syntax examples: PITCH/%MFG_THREAD_PITCH
PITCH/(1/%MFG_THREAD_PITCH),MULTRD,%MFG_NUM_THREADS
FEDRAT/%MFG_THREAD_PITCH,MMPR
NC Commands |
Comments |
NC_SPINDLE_ON |
The syntax of this NC command is SPINDL/ON and cannot be parameterized.
|
NC_SPINDLE_START NC_SPINDLE |
|
MFG_SPNDL_UNIT |
Defines the spindle speed unit. This is done from a list with two values:
- First value: spindle rotation expressed in revolutions per minute.
By default,
the value is RPM.
- Second value: spindle rotation expressed in surface meters per minute.
By default,
the value is SMM.
|
MFG_SPNDL_WAY |
Defines the spindle direction. This is done from a list with two values:
- First value: spindle rotation processed clockwise.
By default,
the value is CLW.
- Second value: spindle rotation processed counter-clockwise.
By default,
the value is CCLW.
|
MFG_SPNDL_SPEED |
Defines the numerical value of the spindle speed. |
MFG_SPNDL_DIAMTR |
Defines the diameter of the tool where the spindle speed is taken
into account. |
NC_SPINDLE_LATHE |
Corresponds to the part spindle speed. |
NC_SPINDLE_STOP |
Note:
this NC command is available to allow compatibility with previous versions.
However, whenever possible, use NC_SPINDLE_LOCK or NC_SPINDLE_OFF
instead of MFG_SPNDL_STOP.
|
MFG_SPNDL_STOP |
List with two values defining the action applied to the
spindle:
- First value: de-activation of the spindle.
By default,
the value is OFF.
- Second value: spindle locked in an indexed position.
By default,
the value is LOCK.
|
NC_SPINDLE_LOCK |
The syntax of this NC command is SPINDL/LOCK and cannot be parameterized. |
NC_SPINDLE_OFF |
The syntax of this NC command is SPINDL/OFF and cannot be parameterized. |
By default,
the syntax is
SPINDL/%MFG_SPNDL_SPEED,&MFG_SPNDL_UNIT,
&MFG_SPNDL_WAY
NC Commands |
Comments |
NC_THREAD_TURN |
|
NC_THREAD_TURN_OFF |
Ends a NC_THREAD_TURN statement. |
Syntax examples THREAD/TURN
*START_NC_COMMAND
NC_THREAD_TURN_OFF
THREAD/OFF
*END

NC Instructions
For a given machine tool (i.e. post-processor), you can define sequences
of PP word syntaxes associated to particular NC instructions.
Displacing and Locking Linear and Rotary
Axes- Default format for a linear displacement
PPFUN/ <Letter of the axis>,<Letter of the axis>AXIS,value of the
displacement
- Customized in the PP table
- By means of NC_AXIS_MOVE
/
*START_NC_COMMAND NC_AXIS_MOVE
CLAMP/OFF,%MFG_NCAXIS_NAME,%MFG_AXIS_POSITION
*END
/
- Format for a rotary displacement:
ROTABL/value of the rotation,<rotary direction >,<rotation axis>
- Customized in the PP table
- By means of the NC instructions
NC_TABLE_ROTATION, NC_MACHINING_AXIS and NC_HEAD_ROTATION.
/
*START_NC_INSTRUCTION NC_HEAD_ROTATION
*START_SEQUENCE
ROTHED/%MFG_AMOUNT_ROT,%MFG_DIR_OF_ROT
*END
*END
/
*START_NC_INSTRUCTION NC_TABLE_ROTATION
*START_SEQUENCE
ROTABL/%MFG_AMOUNT_ROT,%MFG_DIR_OF_ROT,%MFG_ABC_AXIS
*END
*END
/
*START_NC_INSTRUCTION NC_MACHINING_AXIS
*START_SEQUENCE
$$ %MFG_NCAXIS_IDENTIFIER
$$ %MFG_NCAXIS_X_VECX %MFG_NCAXIS_X_VECY %MFG_NCAXIS_X_VECZ
%MFG_NCAXIS_X_ORIG
$$ %MFG_NCAXIS_Y_VECX %MFG_NCAXIS_Y_VECY %MFG_NCAXIS_Y_VECZ
%MFG_NCAXIS_Y_ORIG
$$ %MFG_NCAXIS_Z_VECX %MFG_NCAXIS_Z_VECY %MFG_NCAXIS_Z_VECZ
%MFG_NCAXIS_Z_ORIG
CATMAT/%MFG_NCAXIS_X_ORIG,%MFG_NCAXIS_Y_ORIG,%MFG_NCAXIS_Z_ORIG,
%MFG_NCAXIS_X_VECX,%MFG_NCAXIS_X_VECY,%MFG_NCAXIS_X_VECZ,
%MFG_NCAXIS_Y_VECX,%MFG_NCAXIS_Y_VECY,%MFG_NCAXIS_Y_VECZ,
%MFG_NCAXIS_Z_VECX,% MFG_NCAXIS_Z_VECY,%MFG_NCAXIS_Z_VECZ,
%MFG_NCAXIS_IDENTIFIER
*END
*END
- Blocked axix
LOCK/ <Letter of the axis>,<Letter of the axis>AXIS,ON
- Customized in the PP table
- By means of NC_AXIS_LOCK.
/
*START_NC_COMMAND NC_AXIS_LOCK
CLAMP/%MFG_AXIS_LOCK_STATUS,%MFG_NCAXIS_NAME
*END
/

Axial Machining
Operation Type NC Instructions
For axial machining operations, the standard parameters are either:
- parameters defined on the corresponding machining operation (geometrical
data, machining strategy parameters, feeds and speeds, and so on)
- parameters that are calculated according to an application method.
Examples
In the figures below:
- the detail depth (MFG_DETAIL_DEPTH), total depth (MFG_TOTAL_DEPTH) and
total depth up to the tool compensation point (MFG_TOTAL_DEPTH_COMP)
are computed parameters.
- the breakthrough distance (MFG_BREAKTHROUGH) is a machining strategy
parameter
- the tool tip length is a geometric attribute of the tool (MFG_TL_TIP_LGTH).
The overall breakthrough is the breakthrough distance plus the tool tip length.
- Figure 1 showing Total depth without breakthrough
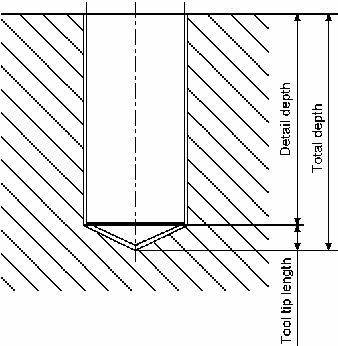
- Figure 2 showingTotal depth with breakthrough (The figures below show Depth mode behavior on axial operations with chamfering
machining):
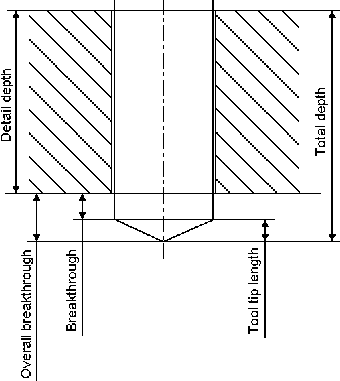
- Figure 3 showing Spot Drilling with
Depth mode=By Tip
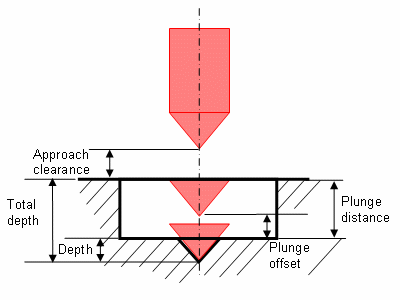
- Figure 4 showing Countersinking with
Depth mode=By Diameter
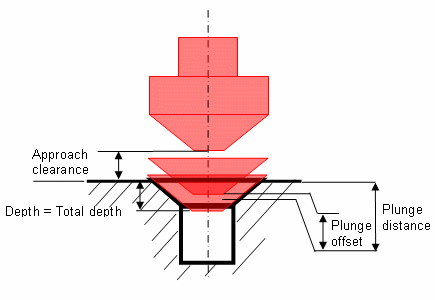
NC_BACK_BORINGGeneral parameters are as follows.
NC Commands |
Comments |
MFG_MO_TYPE |
Defines the machining operation type. |
MFG_MO_IDENTIFIER |
Specifies the machining operation name or identifier. |
MFG_PATTERN_NAME |
Specifies the machining pattern name. |
Feeds and Speeds parameters are as follows:
NC Commands |
Comments |
MFG_FEED_APP_MODE |
Specifies the approach feedrate mode (0: Value / 1: Rapid). |
MFG_FEED_APP_VALUE MFG_FEED_APPRCH |
Defines the approach feedrate. |
MFG_FEED_PLUNGE_MODE MFG_FEED_PL_TYPE |
Defines the plunge feedrate mode (0: Value
/ 1: Rapid). |
MFG_FEED_PLUNGE_VALUE MFG_PLUNGE_FEED |
Defines the plunge feedrate. |
MFG_FEED_MACH_VALUE MFG_FEED_MACH |
Defines the machining feedrate. |
MFG_SPINDLE_MACH_VALUE MFG_SPNDL_MACH |
Defines the machining spindle speed. |
MFG_FEED_RETRACT_MODE MFG_FEED_RT_TYPE |
Defines the retract feedrate mode (0: Value
/ 1: Rapid). |
MFG_FEED_RETRACT_VALUE MFG_FEED_RETRACT |
Defines the retract feedrate. |
MFG_FEED_UNIT |
Defines the feedrate unit. |
MFG_SPNDL_UNIT |
Defines the spindle speed unit. |
Machining Strategy parameters are as follows:
NC Commands |
Comments |
MFG_CLEAR_TIP |
Defines the approach clearance. |
MFG_CLEAR_TIP_2 |
Defines the second approach clearance. |
MFG_DEPTH_MODE |
Defines the depth mode (1: Tip / 2: Shoulder).
|
MFG_DWELL_MODE |
Defines the dwell mode (0: None / 1: By revolutions / 2: By time). |
MFG_DWELL_REVOL |
Defines the dwell delay in revolutions. |
MFG_DWELL_TIME |
Defines the dwell delay in time units (seconds). |
MFG_LIFT_MODE |
Defines the shift mode (0: None / 1: Linear coordinates / 2: Polar coordinates). |
MFG_XOFF |
Defines a shift along X. |
MFG_YOFF |
Defines a shift along Y. |
MFG_ZOFF |
Defines a shift along Z. |
MFG_LIFT_ANGLE |
Defines a shift angle. |
MFG_LIFT_DIST |
Defines a shift distance. |
MFG_RETRACT_CLEAR_TIP |
Defines a retract clearance. |
MFG_TOOL_COMP MFG_TL_COMP |
Specifies the length number of current corrector. |
MFG_TOOL_COMP_DIST |
Defines the distance between the position of the current corrector
and the tool tip. |
MFG_TOOL_COMP_DIST_1 |
Defines the distance between the position of the first corrector
and the tool tip. |
Geometry parameters are as follows:
NC Commands |
Comments |
MFG_DIAMETER |
Defines the nominal diameter of the tool. |
MFG_NOMINAL_DIAMETER |
Defines the nominal diameter of the machined feature. |
MFG_BCK_BORE_VAL |
Defines the back bore depth. |
MFG_JUMP_DIST |
Defines the jump distance. |
Computed parameters are as follows (see Figure
1 and Figure 2 above):
NC Commands |
Comments |
MFG_DETAIL_DEPTH |
Computes the hole depth that is effectively machined. |
MFG_TOTAL_DEPTH |
Computes the total depth machined by the operation. This includes the
hole depth, breakthrough, and tool tip length. |
MFG_TOTAL_DEPTH_COMP |
Computes the total depth machined by the operation up to the tool
compensation point selected for the operation. This includes hole depth,
breakthrough, and tool tip length up to the compensation point. |
MFG_CMP_DWL_TIME |
Computes the dwell delay (in time units of seconds): this
parameter is computed if dwell mode is set to 'revolutions'. Otherwise,
the dwell time is returned as is. |
MFG_CMP_OFFSET |
Computes the offset. |
MFG_CMP_ANGLE |
Computes the shift angle. This parameter is computed if Shift mode
is set to 'Linear coordinates'. Otherwise, the Shift angle is returned as
is. |
By default,
the syntax is
CYCLE/BORE,%MFG_TOTAL_DEPTH,%MFG_CLEAR_TIP
NC_BORING General parameters are as follows:
NC Commands |
Comments |
MFG_MO_TYPE |
Defines the machining operation type. |
MFG_MO_IDENTIFIER |
Specifies the machining operation name or identifier. |
MFG_PATTERN_NAME |
Specifies the machining pattern name. |
Feeds and Speeds parameters are as follows:
NC Commands |
Comments |
MFG_FEED_APP_MODE |
Specifies the approach feedrate mode (0: Value / 1: Rapid). |
MFG_FEED_APP_VALUE MFG_FEED_APPRCH |
Defines the approach feedrate. |
MFG_FEED_PLUNGE_MODE MFG_FEED_PL_TYPE |
Defines the plunge feedrate mode (0: Value
/ 1: Rapid). |
MFG_FEED_PLUNGE_VALUE MFG_PLUNGE_FEED |
Defines the plunge feedrate. |
MFG_FEED_MACH_VALUE MFG_FEED_MACH |
Defines the machining feedrate. |
MFG_SPINDLE_MACH_VALUE MFG_SPNDL_MACH |
Defines the machining spindle speed. |
MFG_FEED_RETRACT_MODE MFG_FEED_RT_TYPE |
Defines the retract feedrate mode (0: Value
/ 1: Rapid). |
MFG_FEED_RETRACT_VALUE MFG_FEED_RETRACT |
Defines the retract feedrate. |
MFG_FEED_UNIT |
Defines the feedrate unit. |
MFG_SPNDL_UNIT |
Defines the spindle speed unit. |
Machining Strategy parameters are as follows:
NC Commands |
Comments |
MFG_CLEAR_TIP |
Defines the approach clearance. |
MFG_DEPTH_MODE |
Defines the depth mode (1: Tip / 2: Shoulder).
|
MFG_BREAKTHROUGH |
Defines the breakthrough distance. |
MFG_PLUNGE_MODE |
Defines the plunge mode (0: None / 1: Tip / 3: Diameter). |
MFG_PLUNGE_TIP |
Defines the plunge tip distance. |
MFG_PLUNGE_OFFST |
Defines the plunge tip offset. |
MFG_PLUNGE_DIAMETER |
Defines the plunge diameter. |
MFG_DWELL_MODE |
Defines the dwell mode (0: None / 1: By revolutions / 2: By time). |
MFG_DWELL_REVOL |
Defines the dwell delay in revolutions. |
MFG_DWELL_TIME |
Defines the dwell delay in time units (seconds). |
MFG_TOOL_COMP MFG_TL_COMP |
Specifies the length number of current corrector. |
MFG_TOOL_COMP_DIST |
Specifies the length number of the first corrector. |
MFG_TOOL_COMP_DIST |
Defines the distance between the position of the current corrector
and the tool tip. |
MFG_TOOL_COMP_DIST_1 |
Defines the distance between the position of the first corrector
and the tool tip. |
Geometry parameters are as follows:
NC Commands |
Comments |
MFG_DIAMETER |
Defines the nominal diameter of the tool. |
MFG_NOMINAL_DIAMETER |
Defines the nominal diameter of the machined feature. |
MFG_JUMP_DIST |
Defines the jump distance. |
Computed parameters are as follows (see Figure
1 and Figure 2 above):
NC Commands |
Comments |
MFG_DETAIL_DEPTH |
Computes the hole depth that is effectively machined. |
MFG_TOTAL_DEPTH |
Computes the total depth machined by the operation. This includes the
hole depth, breakthrough, and tool tip length. |
MFG_TOTAL_DEPTH_COMP |
Computes the total depth machined by the operation up to the tool
compensation point selected for the operation. This includes hole depth,
breakthrough, and tool tip length up to the compensation point. |
MFG_PLUNGE_DIST |
Whatever the selected plunge mode (by Tip or by Diameter),
this parameter returns the plunge distance. The plunge offset is taken into
account in this value.
|
MFG_CMP_DWL_TIME |
Computes the dwell delay (in time units of seconds): this
parameter is computed if dwell mode is set to 'revolutions'. Otherwise,
the dwell time is returned as is. |
By default,
the syntax is
CYCLE/BORE,%MFG_TOTAL_DEPTH,%MFG_CLEAR_TIP
NC_BORING_SPINDLE_STOP General parameters are as follows:
NC Commands |
Comments |
MFG_MO_TYPE |
Defines the machining operation type. |
MFG_MO_IDENTIFIER |
Specifies the machining operation name or identifier. |
MFG_PATTERN_NAME |
Specifies the machining pattern name. |
Feeds and Speeds parameters are as follows:
NC Commands |
Comments |
MFG_FEED_APP_MODE |
Specifies the approach feedrate mode (0: Value / 1: Rapid). |
MFG_FEED_APP_VALUE MFG_FEED_APPRCH |
Defines the approach feedrate. |
MFG_FEED_PLUNGE_MODE MFG_FEED_PL_TYPE |
Defines the plunge feedrate mode (0: Value
/ 1: Rapid). |
MFG_FEED_PLUNGE_VALUE MFG_PLUNGE_FEED |
Defines the plunge feedrate. |
MFG_FEED_MACH_VALUE MFG_FEED_MACH |
Defines the machining feedrate. |
MFG_SPINDLE_MACH_VALUE MFG_SPNDL_MACH |
Defines the machining spindle speed. |
MFG_FEED_RETRACT_MODE MFG_FEED_RT_TYPE |
Defines the retract feedrate mode (0: Value
/ 1: Rapid). |
MFG_FEED_RETRACT_VALUE MFG_FEED_RETRACT |
Defines the retract feedrate. |
MFG_FEED_UNIT |
Defines the feedrate unit. |
MFG_SPNDL_UNIT |
Defines the spindle speed unit. |
Machining Strategy parameters are as follows:
NC Commands |
Comments |
MFG_CLEAR_TIP |
Defines the approach clearance. |
MFG_DEPTH_MODE |
Defines the depth mode (1: Tip / 2: Shoulder).
|
MFG_BREAKTHROUGH |
Defines the breakthrough distance. |
MFG_PLUNGE_MODE |
Defines the plunge mode (0: None / 1: Tip / 3: Diameter). |
MFG_PLUNGE_TIP |
Defines the plunge tip distance. |
MFG_PLUNGE_OFFST |
Defines the plunge tip offset. |
MFG_PLUNGE_DIAMETER |
Defines the plunge diameter. |
MFG_DWELL_MODE |
Defines the dwell mode (0: None / 1: By revolutions / 2: By time). |
MFG_DWELL_REVOL |
Defines the dwell delay in revolutions. |
MFG_DWELL_TIME |
Defines the dwell delay in time units (seconds). |
MFG_LIFT_MODE |
Defines the shift mode (0: None / 1: Linear coordinates / 2: Polar coordinates). |
MFG_XOFF |
Defines a shift along X. |
MFG_YOFF |
Defines a shift along Y. |
MFG_ZOFF |
Defines a shift along Z. |
MFG_LIFT_ANGLE |
Defines a shift angle. |
MFG_LIFT_DIST |
Defines a shift distance. |
MFG_TOOL_COMP MFG_TL_COMP |
Specifies the length number of current corrector. |
MFG_TOOL_COMP_1 |
Specifies the length number of the first corrector. |
MFG_TOOL_COMP_DIST |
Defines the distance between the position of the current corrector
and the tool tip. |
MFG_TOOL_COMP_DIST_1 |
Defines the distance between the position of the first corrector
and the tool tip. |
Geometry parameters are as follows:
NC Commands |
Comments |
MFG_DIAMETER |
Defines the nominal diameter of the tool. |
MFG_NOMINAL_DIAMETER |
Defines the nominal diameter of the machined feature. |
MFG_JUMP_DIST |
Defines the jump distance. |
Computed parameters are as follows (see Figure
1 and Figure 2 above):
NC Commands |
Comments |
MFG_DETAIL_DEPTH |
Computes the hole depth that is effectively machined. |
MFG_TOTAL_DEPTH |
Computes the total depth machined by the operation. This includes the
hole depth, breakthrough, and tool tip length. |
MFG_TOTAL_DEPTH_COMP |
Computes the total depth machined by the operation up to the tool
compensation point selected for the operation. This includes hole depth,
breakthrough, and tool tip length up to the compensation point. |
MFG_PLUNGE_DIST |
Whatever the selected plunge mode (by Tip or by Diameter),
this parameter returns the plunge distance. The plunge offset is taken into
account in this value.
|
MFG_CMP_DWL_TIME |
Computes the dwell delay (in time units of seconds): this
parameter is computed if dwell mode is set to 'revolutions'. Otherwise,
the dwell time is returned as is. |
MFG_CMP_OFFSET |
Computes the offset. |
MFG_CMP_ANGLE |
Computes the shift angle. This parameter is computed if Shift mode
is set to 'Linear coordinates'. Otherwise, the Shift angle is returned as
is. |
By default,
the syntax is
CYCLE/BORE,%MFG_TOTAL_DEPTH,%MFG_CLEAR_TIP
NC_BORING_AND_CHAMFERING General parameters are as follows:
NC Commands |
Comments |
MFG_MO_TYPE |
Defines the machining operation type. |
MFG_MO_IDENTIFIER |
Specifies the machining operation name or identifier. |
MFG_PATTERN_NAME |
Specifies the machining pattern name. |
Feeds and Speeds parameters are as follows:
NC Commands |
Comments |
MFG_FEED_APP_MODE |
Specifies the approach feedrate mode (0: Value / 1: Rapid). |
MFG_FEED_APP_VALUE MFG_FEED_APPRCH |
Defines the approach feedrate. |
MFG_FEED_PLUNGE_MODE MFG_FEED_PL_TYPE |
Defines the plunge feedrate mode (0: Value
/ 1: Rapid). |
MFG_FEED_PLUNGE_VALUE MFG_PLUNGE_FEED |
Defines the plunge feedrate. |
MFG_FEED_MACH_VALUE MFG_FEED_MACH |
Defines the machining feedrate. |
MFG_SPINDLE_MACH_VALUE MFG_SPNDL_MACH |
Defines the machining spindle speed. |
MFG_CHAMFER_FEED_VALUE MFG_CHAMFER_FEED |
Defines the machining feedrate for chamfering
phase. |
MFG_CHAMFER_SPINDLE_VALUE |
Defines the machining spindle speed for chamfering phase. |
MFG_FEED_RETRACT_MODE MFG_FEED_RT_TYPE |
Defines the retract feedrate mode (0: Value
/ 1: Rapid). |
MFG_FEED_RETRACT_VALUE MFG_FEED_RETRACT |
Defines the retract feedrate. |
MFG_FEED_UNIT |
Defines the feedrate unit. |
MFG_SPNDL_UNIT |
Defines the spindle speed unit. |
Machining Strategy parameters are as follows:
NC Commands |
Comments |
MFG_CLEAR_TIP |
Defines the approach clearance. |
MFG_CLEAR_TIP_2 |
Defines the second approach clearance |
MFG_DEPTH_MODE |
Defines the depth mode (1: Tip / 2: Shoulder).
|
MFG_BREAKTHROUGH |
Defines the breakthrough distance. |
MFG_PLUNGE_MODE |
Defines the plunge mode (0: None / 1: Tip / 3: Diameter). |
MFG_PLUNGE_TIP |
Defines the plunge tip distance. |
MFG_PLUNGE_OFFST |
Defines the plunge tip offset. |
MFG_PLUNGE_DIAMETER |
Defines the plunge diameter. |
MFG_DWELL_MODE |
Defines the dwell mode (0: None / 1: By revolutions / 2: By time). |
MFG_DWELL_REVOL |
Defines the dwell delay in revolutions. |
MFG_DWELL_TIME |
Defines the dwell delay in time units (seconds). |
MFG_TOOL_COMP MFG_TL_COMP |
Specifies the length number of current corrector. |
MFG_TOOL_COMP_1 |
Specifies the length number of the first corrector. |
MFG_TOOL_COMP_2 |
Specifies the length number of the second corrector. |
MFG_TOOL_COMP_DIST |
Defines the distance between the position of the current corrector
and the tool tip. |
MFG_TOOL_COMP_DIST_1 |
Defines the distance between the position of the first corrector
and the tool tip. |
MFG_TOOL_COMP_DIST_2 |
Defines the distance between the position of the second corrector
and the tool tip. |
Geometry parameters are as follows:
NC Commands |
Comments |
MFG_DIAMETER MFG_CHAMFER_VAL |
Defines the chamfer diameter. |
MFG_NOMINAL_DIAMETER |
Defines the nominal diameter of the machined feature. |
MFG_JUMP_DIST |
Defines the jump distance. |
Computed parameters are as follows (see Figure
1 and Figure 2 above):
NC Commands |
Comments |
MFG_DETAIL_DEPTH |
Computes the hole depth that is effectively machined. |
MFG_TOTAL_DEPTH |
Computes the total depth machined by the operation. This includes the
hole depth, breakthrough, and tool tip length. |
MFG_TOTAL_DEPTH_COMP |
Computes the total depth machined by the operation up to the tool
compensation point selected for the operation. This includes hole depth,
breakthrough, and tool tip length up to the compensation point. |
MFG_PLUNGE_DIST |
Whatever the selected plunge mode (by Tip or by Diameter),
this parameter returns the plunge distance. The plunge offset is taken into
account in this value.
|
MFG_CMP_DWL_TIME |
Computes the dwell delay (in time units of seconds): this
parameter is computed if dwell mode is set to 'revolutions'. Otherwise,
the dwell time is returned as is. |
By default,
the syntax is
CYCLE/BORE,%MFG_TOTAL_DEPTH,%MFG_CLEAR_TIP
NC_BREAK_CHIPS General parameters are as follows:
NC Commands |
Comments |
MFG_MO_TYPE |
Defines the machining operation type. |
MFG_MO_IDENTIFIER |
Specifies the machining operation name or identifier. |
MFG_PATTERN_NAME |
Specifies the machining pattern name. |
Feeds and Speeds parameters are as follows:
NC Commands |
Comments |
MFG_FEED_APP_MODE |
Specifies the approach feedrate mode (0: Value / 1: Rapid). |
MFG_FEED_APP_VALUE MFG_FEED_APPRCH |
Defines the approach feedrate. |
MFG_FEED_PLUNGE_MODE MFG_FEED_PL_TYPE |
Defines the plunge feedrate mode (0: Value
/ 1: Rapid). |
MFG_FEED_PLUNGE_VALUE MFG_PLUNGE_FEED |
Defines the plunge feedrate. |
MFG_FEED_MACH_VALUE MFG_FEED_MACH |
Defines the machining feedrate. |
MFG_SPINDLE_MACH_VALUE MFG_SPNDL_MACH |
Defines the machining spindle speed. |
MFG_FEED_RETRACT_MODE MFG_FEED_RT_TYPE |
Defines the retract feedrate mode (0: Value
/ 1: Rapid). |
MFG_FEED_RETRACT_VALUE MFG_FEED_RETRACT |
Defines the retract feedrate. |
MFG_FEED_UNIT |
Defines the feedrate unit. |
MFG_SPNDL_UNIT |
Defines the spindle speed unit. |
Machining Strategy parameters are as follows:
NC Commands |
Comments |
MFG_CLEAR_TIP |
Defines the approach clearance. |
MFG_DEPTH_MODE |
Defines the depth mode (1: Tip / 2: Shoulder).
|
MFG_BREAKTHROUGH |
Defines the breakthrough distance. |
MFG_AXIAL_DEPTH |
Defines the maximum depth of cut. |
MFG_OFFSET_RET |
Defines the retract offset. |
MFG_PLUNGE_MODE |
Defines the plunge mode (0: None / 1: Tip / 3: Diameter). |
MFG_PLUNGE_TIP |
Defines the plunge tip distance. |
MFG_PLUNGE_OFFST |
Defines the plunge tip offset. |
MFG_PLUNGE_DIAMETER |
Defines the plunge diameter. |
MFG_DWELL_MODE |
Defines the dwell mode (0: None / 1: By revolutions / 2: By time). |
MFG_DWELL_REVOL |
Defines the dwell delay in revolutions. |
MFG_DWELL_TIME |
Defines the dwell delay in time units (seconds). |
MFG_TOOL_COMP MFG_TL_COMP |
Specifies the length number of current corrector. |
MFG_TOOL_COMP_1 |
Specifies the length number of the first corrector. |
MFG_TOOL_COMP_DIST |
Defines the distance between the position of the current corrector
and the tool tip. |
MFG_TOOL_COMP_DIST_1 |
Defines the distance between the position of the first corrector
and the tool tip. |
Geometry parameters are as follows:
NC Commands |
Comments |
MFG_DIAMETER |
Defines the nominal diameter of the tool. |
MFG_NOMINAL_DIAMETER |
Defines the nominal diameter of the machined feature. |
MFG_DETAIL_DEPTH |
Computes the hole depth that is effectively machined. |
MFG_TOTAL_DEPTH |
Computes the total depth machined by the operation. This includes the
hole depth, breakthrough, and tool tip length. |
MFG_TOTAL_DEPTH_COMP |
Computes the total depth machined by the operation up to the tool
compensation point selected for the operation. This includes hole depth,
breakthrough, and tool tip length up to the compensation point. |
MFG_PLUNGE_DIST |
Whatever the selected plunge mode (by Tip or by Diameter),
this parameter returns the plunge distance. The plunge offset is taken into
account in this value.
|
MFG_CMP_DWL_TIME |
Computes the dwell delay (in time units of seconds): this
parameter is computed if dwell mode is set to 'revolutions'. Otherwise,
the dwell time is returned as is. |
MFG_EFFCT_DEPTH |
Defines the effective depth (= maximum depth of cut).
|
By default,
the syntax is
CYCLE/BRKCHP,%MFG_TOTAL_DEPTH,%MFG_CLEAR_TIP
NC_CIRCULAR_MILLING General parameters are as follows:
NC Commands |
Comments |
MFG_MO_TYPE |
Defines the machining operation type. |
MFG_MO_IDENTIFIER |
Specifies the machining operation name or identifier. |
MFG_PATTERN_NAME |
Specifies the machining pattern name. |
Feeds and Speeds parameters are as follows:
NC Commands |
Comments |
MFG_FEED_APP_VALUE MFG_FEED_APPRCH |
Defines the approach feedrate. |
MFG_FEED_PLUNGE_MODE MFG_FEED_PL_TYPE |
Defines the plunge feedrate mode (0: Value
/ 1: Rapid). |
MFG_FEED_PLUNGE_VALUE MFG_PLUNGE_FEED |
Defines the plunge feedrate. |
MFG_FEED_MACH_VALUE MFG_FEED_MACH |
Defines the machining feedrate. |
MFG_SPINDLE_MACH_VALUE MFG_SPNDL_MACH |
Defines the machining spindle speed. |
MFG_FEED_RETRACT_MODE MFG_FEED_RT_TYPE |
Defines the retract feedrate mode (0: Value
/ 1: Rapid). |
MFG_FEED_RETRACT_VALUE MFG_FEED_RETRACT |
Defines the retract feedrate. |
MFG_FEED_UNIT |
Defines the feedrate unit. |
MFG_SPNDL_UNIT |
Defines the spindle speed unit. |
Machining Strategy parameters are as follows:
NC Commands |
Comments |
MFG_CLEAR_TIP |
Defines the approach clearance. |
MFG_TOOL_COMP MFG_TL_COMP |
Specifies the length number of current corrector. |
MFG_TOOL_COMP_1 |
Specifies the length number of the first corrector. |
MFG_TOOL_COMP_DIST |
Defines the distance between the position of the current corrector
and the tool tip. |
MFG_TOOL_COMP_DIST_1 |
Defines the distance between the position of the first corrector
and the tool tip. |
MFG_RADIAL_STEP |
Defines the distance between paths. |
MFG_RADIAL_NB |
Defines the number of paths. |
MFG_AXIAL_STRAT |
Defines the axial strategy (1: Max depth of cut / 2: Number of levels /
3: Number of levels without top).
|
MFG_AXIAL_DEPTH |
Defines the maximum depth of cut. |
MFG_AXIAL_NUMBER |
Defines the number of levels. |
MFG_SEQUENCING_STRAT |
Defines the sequencing mode (1: Radial first / 2: Axial first). |
MFG_TOLER_MACH |
Defines the machining tolerance. |
MFG_DIR_CUT |
Defines the direction of cut (1: Climb / 2: Conventional). |
MFG_OVERHANG |
Defines the percentage of overlap. |
MFG_DRAFT_ANGLE |
Defines the automatic draft angle. |
MFG_CIRCULAR_MODE |
Defines the machining mode (1: Standard / 2: Helical). |
MFG_HELIX_MODE |
Defines the helix mode (1: By pitch / 2: By angle).
|
MFG_HELIX_ANGLE |
Defines the helix angle.
|
MFG_PITCH |
Defines the pitch. |
Geometry parameters are as follows:
NC Commands |
Comments |
MFG_DIAMETER |
Defines the nominal diameter of the tool. |
MFG_JUMP_DIST |
Defines the jump distance. |
Computed parameters are as follows (see Figure
1 and Figure 2 above):
NC Commands |
Comments |
MFG_DETAIL_DEPTH |
Computes the hole depth that is effectively machined. |
MFG_TOTAL_DEPTH |
Computes the total depth machined by the operation. This includes the
hole depth, breakthrough, and tool tip length. |
MFG_TOTAL_DEPTH_COMP |
Computes the total depth machined by the operation up to the tool
compensation point selected for the operation. This includes hole depth,
breakthrough, and tool tip length up to the compensation point. |
the syntax is CYCLE/CIRCULARMILLING,%MFG_TOTAL_DEPTH,
%MFG_CLEAR_TIP
NC_COUNTERBORING General parameters are as follows:
NC Commands |
Comments |
MFG_MO_TYPE |
Defines the machining operation type. |
MFG_MO_IDENTIFIER |
Specifies the machining operation name or identifier. |
MFG_PATTERN_NAME |
Specifies the machining pattern name. |
Feeds and Speeds parameters are as follows:
NC Commands |
Comments |
MFG_FEED_APP_MODE |
Specifies the approach feedrate mode (0: Value / 1: Rapid). |
MFG_FEED_APP_VALUE MFG_FEED_APPRCH |
Defines the approach feedrate. |
MFG_FEED_PLUNGE_MODE MFG_FEED_PL_TYPE |
Defines the plunge feedrate mode (0: Value
/ 1: Rapid). |
MFG_FEED_PLUNGE_VALUE MFG_PLUNGE_FEED |
Defines the plunge feedrate. |
MFG_FEED_MACH_VALUE MFG_FEED_MACH |
Defines the machining feedrate. |
MFG_SPINDLE_MACH_VALUE MFG_SPNDL_MACH |
Defines the machining spindle speed. |
MFG_FEED_RETRACT_MODE MFG_FEED_RT_TYPE |
Defines the retract feedrate mode (0: Value
/ 1: Rapid). |
MFG_FEED_RETRACT_VALUE MFG_FEED_RETRACT |
Defines the retract feedrate. |
MFG_FEED_UNIT |
Defines the feedrate unit. |
MFG_SPNDL_UNIT |
Defines the spindle speed unit. |
Machining Strategy parameters are as follows:
NC Commands |
Comments |
MFG_CLEAR_TIP |
Defines the approach clearance. |
MFG_DEPTH_MODE |
Defines the depth mode (1: Tip / 2: Shoulder).
|
MFG_PLUNGE_MODE |
Defines the plunge mode (0: None / 1: Tip / 3: Diameter). |
MFG_PLUNGE_TIP |
Defines the plunge tip distance. |
MFG_PLUNGE_OFFST |
Defines the plunge tip offset. |
MFG_PLUNGE_DIAMETER |
Defines the plunge diameter. |
MFG_DWELL_MODE |
Defines the dwell mode (0: None / 1: By revolutions / 2: By time). |
MFG_DWELL_REVOL |
Defines the dwell delay in revolutions. |
MFG_DWELL_TIME |
Defines the dwell delay in time units (seconds). |
MFG_TOOL_COMP MFG_TL_COMP |
Specifies the length number of current corrector. |
MFG_TOOL_COMP_1 |
Specifies the length number of the first corrector. |
MFG_TOOL_COMP_DIST |
Defines the distance between the position of the current corrector
and the tool tip. |
MFG_TOOL_COMP_DIST_1 |
Defines the distance between the position of the first corrector
and the tool tip. |
Geometry parameters are as follows:
NC Commands |
Comments |
MFG_DIAMETER |
Defines the nominal diameter of the tool. |
MFG_NOMINAL_DIAMETER |
Defines the nominal diameter of the machined feature. |
MFG_JUMP_DIST |
Defines the jump distance. |
Computed parameters are as follows (see Figure
1 and Figure 2 above):
NC Commands |
Comments |
MFG_DETAIL_DEPTH |
Computes the hole depth that is effectively machined. |
MFG_TOTAL_DEPTH |
Computes the total depth machined by the operation. This includes the
hole depth, breakthrough, and tool tip length. |
MFG_TOTAL_DEPTH_COMP |
Computes the total depth machined by the operation up to the tool
compensation point selected for the operation. This includes hole depth,
breakthrough, and tool tip length up to the compensation point. |
MFG_PLUNGE_DIST |
Whatever the selected plunge mode (by Tip or by Diameter),
this parameter returns the plunge distance. The plunge offset is taken into
account in this value.
|
MFG_CMP_DWL_TIME |
Computes the dwell delay (in time units of seconds): this
parameter is computed if dwell mode is set to 'revolutions'. Otherwise,
the dwell time is returned as is. |
By default,
the syntax is
CYCLE/BORE,%MFG_TOTAL_DEPTH,%MFG_CLEAR_TIP
NC_COUNTERSINKING General parameters are as follows:
NC Commands |
Comments |
MFG_MO_TYPE |
Defines the machining operation type. |
MFG_MO_IDENTIFIER |
Specifies the machining operation name or identifier. |
MFG_PATTERN_NAME |
Specifies the machining pattern name. |
Feeds and Speeds parameters are as follows:
NC Commands |
Comments |
MFG_FEED_APP_MODE |
Specifies the approach feedrate mode (0: Value / 1: Rapid). |
MFG_FEED_APP_VALUE MFG_FEED_APPRCH |
Defines the approach feedrate. |
MFG_FEED_PLUNGE_MODE MFG_FEED_PL_TYPE |
Defines the plunge feedrate mode (0: Value
/ 1: Rapid). |
MFG_FEED_PLUNGE_VALUE MFG_PLUNGE_FEED |
Defines the plunge feedrate. |
MFG_FEED_MACH_VALUE MFG_FEED_MACH |
Defines the machining feedrate. |
MFG_SPINDLE_MACH_VALUE MFG_SPNDL_MACH |
Defines the machining spindle speed. |
MFG_FEED_RETRACT_MODE MFG_FEED_RT_TYPE |
Defines the retract feedrate mode (0: Value
/ 1: Rapid). |
MFG_FEED_RETRACT_VALUE MFG_FEED_RETRACT |
Defines the retract feedrate. |
MFG_FEED_UNIT |
Defines the feedrate unit. |
MFG_SPNDL_UNIT |
Defines the spindle speed unit. |
Machining Strategy parameters are as follows:
NC Commands |
Comments |
MFG_CLEAR_TIP |
Defines the approach clearance. |
MFG_DEPTH_MODE |
Defines the depth mode (1: Tip / 2: Shoulder).
|
MFG_PLUNGE_MODE |
Defines the plunge mode (0: None / 1: Tip / 3: Diameter). |
MFG_PLUNGE_TIP |
Defines the plunge tip distance. |
MFG_PLUNGE_OFFST |
Defines the plunge tip offset. |
MFG_PLUNGE_DIAMETER |
Defines the plunge diameter. |
MFG_DWELL_MODE |
Defines the dwell mode (0: None / 1: By revolutions / 2: By time). |
MFG_DWELL_REVOL |
Defines the dwell delay in revolutions. |
MFG_DWELL_TIME |
Defines the dwell delay in time units (seconds). |
MFG_TOOL_COMP MFG_TL_COMP |
Specifies the length number of current corrector. |
MFG_TOOL_COMP_1 |
Specifies the length number of the first corrector. |
MFG_TOOL_COMP_DIST |
Defines the distance between the position of the current corrector
and the tool tip. |
MFG_TOOL_COMP_DIST_1 |
Defines the distance between the position of the first corrector
and the tool tip. |
Geometry parameters are as follows:
NC Commands |
Comments |
MFG_DIAMETER |
Defines the nominal diameter of the tool. |
MFG_NOMINAL_DIAMETER |
Defines the nominal diameter of the machined feature. |
MFG_JUMP_DIST |
Defines the jump distance. |
Computed parameters are as follows (see Figure
4 above):
NC Commands |
Comments |
MFG_DETAIL_DEPTH |
Computes the hole depth that is effectively machined. |
MFG_TOTAL_DEPTH |
Computes the total depth machined by the operation. This includes the
hole depth, breakthrough, and tool tip length. |
MFG_TOTAL_DEPTH_COMP |
Computes the total depth machined by the operation up to the tool
compensation point selected for the operation. This includes hole depth,
breakthrough, and tool tip length up to the compensation point. |
MFG_PLUNGE_DIST |
Whatever the selected plunge mode (by Tip or by Diameter),
this parameter returns the plunge distance. The plunge offset is taken into
account in this value.
|
MFG_CMP_DWL_TIME |
Computes the dwell delay (in time units of seconds): this
parameter is computed if dwell mode is set to 'revolutions'. Otherwise,
the dwell time is returned as is. |
the syntax is CYCLE/CSINK,%MFG_TOTAL_DEPTH,%MFG_CLEAR_TIP
NC_DEEPHOLE General parameters are as follows:
NC Commands |
Comments |
MFG_MO_TYPE |
Defines the machining operation type. |
MFG_MO_IDENTIFIER |
Specifies the machining operation name or identifier. |
MFG_PATTERN_NAME |
Specifies the machining pattern name. |
Feeds and Speeds parameters are as follows:
NC Commands |
Comments |
MFG_FEED_APP_MODE |
Specifies the approach feedrate mode (0: Value / 1: Rapid). |
MFG_FEED_APP_VALUE MFG_FEED_APPRCH |
Defines the approach feedrate. |
MFG_FEED_PLUNGE_MODE MFG_FEED_PL_TYPE |
Defines the plunge feedrate mode (0: Value
/ 1: Rapid). |
MFG_FEED_PLUNGE_VALUE MFG_PLUNGE_FEED |
Defines the plunge feedrate. |
MFG_FEED_MACH_VALUE MFG_FEED_MACH |
Defines the machining feedrate. |
MFG_SPINDLE_MACH_VALUE MFG_SPNDL_MACH |
Defines the machining spindle speed. |
MFG_FEED_RETRACT_MODE MFG_FEED_RT_TYPE |
Defines the retract feedrate mode (0: Value
/ 1: Rapid). |
MFG_FEED_RETRACT_VALUE MFG_FEED_RETRACT |
Defines the retract feedrate. |
MFG_FEED_UNIT |
Defines the feedrate unit. |
MFG_SPNDL_UNIT |
Defines the spindle speed unit. |
Machining Strategy parameters are as follows:
NC Commands |
Comments |
MFG_CLEAR_TIP |
Defines the approach clearance. |
MFG_DEPTH_MODE |
Defines the depth mode (1: Tip / 2: Shoulder).
|
MFG_BREAKTHROUGH |
Defines the breakthrough distance. |
MFG_PLUNGE_MODE |
Defines the plunge mode (0: None / 1: Tip / 3: Diameter). |
MFG_PLUNGE_TIP |
Defines the plunge tip distance. |
MFG_PLUNGE_OFFST |
Defines the plunge tip offset. |
MFG_PLUNGE_DIAMETER |
Defines the plunge diameter. |
MFG_DWELL_MODE |
Defines the dwell mode (0: None / 1: By revolutions / 2: By time). |
MFG_DWELL_REVOL |
Defines the dwell delay in revolutions. |
MFG_DWELL_TIME |
Defines the dwell delay in time units (seconds). |
MFG_AXIAL_DEPTH |
Defines the maximum depth of cut. |
MFG_OFFSET_RET |
Defines the retract offset. |
MFG_DEPTH_DEC |
Defines the decrement rate. |
MFG_DEPTH_LIM |
Defines the decrement limit. |
MFG_TOOL_COMP MFG_TL_COMP |
Specifies the length number of current corrector. |
MFG_TOOL_COMP_1 |
Specifies the length number of the first corrector. |
MFG_TOOL_COMP_DIST |
Defines the distance between the position of the current corrector
and the tool tip. |
MFG_TOOL_COMP_DIST_1 |
Defines the distance between the position of the first corrector
and the tool tip. |
Geometry parameters are as follows:
NC Commands |
Comments |
MFG_DIAMETER |
Defines the nominal diameter of the tool. |
MFG_NOMINAL_DIAMETER |
Defines the nominal diameter of the machined feature. |
MFG_JUMP_DIST |
Defines the jump distance. |
Computed parameters are as follows (see Figure
1 and Figure 2 above):
NC Commands |
Comments |
MFG_DETAIL_DEPTH |
Computes the hole depth that is effectively machined. |
MFG_TOTAL_DEPTH |
Computes the total depth machined by the operation. This includes the
hole depth, breakthrough, and tool tip length. |
MFG_TOTAL_DEPTH_COMP |
Computes the total depth machined by the operation up to the tool
compensation point selected for the operation. This includes hole depth,
breakthrough, and tool tip length up to the compensation point. |
MFG_PLUNGE_DIST |
Whatever the selected plunge mode (by Tip or by Diameter),
this parameter returns the plunge distance. The plunge offset is taken into
account in this value.
|
MFG_CMP_DWL_TIME |
Computes the dwell delay (in time units of seconds): this
parameter is computed if dwell mode is set to 'revolutions'. Otherwise,
the dwell time is returned as is. |
MFG_EFFCT_DEPTH |
Defines the effective depth (= maximum depth of cut).
|
By default,
the syntax is
CYCLE/DEEPHL,%MFG_TOTAL_DEPTH,%MFG_CLEAR_TIP
NC_DRILLING General parameters are as follows:
NC Commands |
Comments |
MFG_MO_TYPE |
Defines the machining operation type. |
MFG_MO_IDENTIFIER |
Specifies the machining operation name or identifier. |
MFG_PATTERN_NAME |
Specifies the machining pattern name. |
Feeds and Speeds parameters are as follows:
NC Commands |
Comments |
MFG_FEED_APP_MODE |
Specifies the approach feedrate mode (0: Value / 1: Rapid). |
MFG_FEED_APP_VALUE MFG_FEED_APPRCH |
Defines the approach feedrate. |
MFG_FEED_PLUNGE_MODE MFG_FEED_PL_TYPE |
Defines the plunge feedrate mode (0: Value
/ 1: Rapid). |
MFG_FEED_PLUNGE_VALUE MFG_PLUNGE_FEED |
Defines the plunge feedrate. |
MFG_FEED_MACH_VALUE MFG_FEED_MACH |
Defines the machining feedrate. |
MFG_SPINDLE_MACH_VALUE MFG_SPNDL_MACH |
Defines the machining spindle speed. |
MFG_FEED_RETRACT_MODE MFG_FEED_RT_TYPE |
Defines the retract feedrate mode (0: Value
/ 1: Rapid). |
MFG_FEED_RETRACT_VALUE MFG_FEED_RETRACT |
Defines the retract feedrate. |
MFG_FEED_UNIT |
Defines the feedrate unit. |
MFG_SPNDL_UNIT |
Defines the spindle speed unit. |
Machining Strategy parameters are as follows:
NC Commands |
Comments |
MFG_CLEAR_TIP |
Defines the approach clearance. |
MFG_DEPTH_MODE |
Defines the depth mode (1: Tip / 2: Shoulder).
|
MFG_BREAKTHROUGH |
Defines the breakthrough distance. |
MFG_PLUNGE_MODE |
Defines the plunge mode (0: None / 1: Tip / 3: Diameter). |
MFG_PLUNGE_TIP |
Defines the plunge tip distance. |
MFG_PLUNGE_OFFST |
Defines the plunge tip offset. |
MFG_PLUNGE_DIAMETER |
Defines the plunge diameter. |
MFG_TOOL_COMP MFG_TL_COMP |
Specifies the length number of current corrector. |
MFG_TOOL_COMP_1 |
Specifies the length number of the first corrector. |
MFG_TOOL_COMP_DIST |
Defines the distance between the position of the current corrector
and the tool tip. |
MFG_TOOL_COMP_DIST_1 |
Defines the distance between the position of the first corrector
and the tool tip. |
Geometry parameters are as follows:
NC Commands |
Comments |
MFG_DIAMETER |
Defines the nominal diameter of the tool. |
MFG_NOMINAL_DIAMETER |
Defines the nominal diameter of the machined feature. |
MFG_JUMP_DIST |
Defines the jump distance. |
Computed parameters are as follows (see Figure
1 and Figure 2 above):
NC Commands |
Comments |
MFG_DETAIL_DEPTH |
Computes the hole depth that is effectively machined. |
MFG_TOTAL_DEPTH |
Computes the total depth machined by the operation. This includes the
hole depth, breakthrough, and tool tip length. |
MFG_TOTAL_DEPTH_COMP |
Computes the total depth machined by the operation up to the tool
compensation point selected for the operation. This includes hole depth,
breakthrough, and tool tip length up to the compensation point. |
MFG_PLUNGE_DIST |
Whatever the selected plunge mode (by Tip or by Diameter),
this parameter returns the plunge distance. The plunge offset is taken into
account in this value.
|
By default,
the syntax is
CYCLE/DRILL,%MFG_TOTAL_DEPTH,%MFG_CLEAR_TIP,%MFG_FEED_MACH,
&MFG_FEED_UNIT
NC_DRILLING_DWELL_DELAY General parameters are as follows:
NC Commands |
Comments |
MFG_MO_TYPE |
Defines the machining operation type. |
MFG_MO_IDENTIFIER |
Specifies the machining operation name or identifier. |
MFG_PATTERN_NAME |
Specifies the machining pattern name. |
Feeds and Speeds parameters are as follows:
NC Commands |
Comments |
MFG_FEED_APP_MODE |
Specifies the approach feedrate mode (0: Value / 1: Rapid). |
MFG_FEED_APP_VALUE MFG_FEED_APPRCH |
Defines the approach feedrate. |
MFG_FEED_PLUNGE_MODE MFG_FEED_PL_TYPE |
Defines the plunge feedrate mode (0: Value
/ 1: Rapid). |
MFG_FEED_PLUNGE_VALUE MFG_PLUNGE_FEED |
Defines the plunge feedrate. |
MFG_FEED_MACH_VALUE MFG_FEED_MACH |
Defines the machining feedrate. |
MFG_SPINDLE_MACH_VALUE MFG_SPNDL_MACH |
Defines the machining spindle speed. |
MFG_FEED_RETRACT_MODE MFG_FEED_RT_TYPE |
Defines the retract feedrate mode (0: Value
/ 1: Rapid). |
MFG_FEED_RETRACT_VALUE MFG_FEED_RETRACT |
Defines the retract feedrate. |
MFG_FEED_UNIT |
Defines the feedrate unit. |
MFG_SPNDL_UNIT |
Defines the spindle speed unit. |
Machining Strategy parameters are as follows:
NC Commands |
Comments |
MFG_CLEAR_TIP |
Defines the approach clearance. |
MFG_DEPTH_MODE |
Defines the depth mode (1: Tip / 2: Shoulder).
|
MFG_BREAKTHROUGH |
Defines the breakthrough distance. |
MFG_PLUNGE_MODE |
Defines the plunge mode (0: None / 1: Tip / 3: Diameter). |
MFG_PLUNGE_TIP |
Defines the plunge tip distance. |
MFG_PLUNGE_OFFST |
Defines the plunge tip offset. |
MFG_PLUNGE_DIAMETER |
Defines the plunge diameter. |
MFG_DWELL_MODE |
Defines the dwell mode (0: None / 1: By revolutions / 2: By time). |
MFG_DWELL_REVOL |
Defines the dwell delay in revolutions. |
MFG_DWELL_TIME |
Defines the dwell delay in time units (seconds). |
MFG_TOOL_COMP MFG_TL_COMP |
Specifies the length number of current corrector. |
MFG_TOOL_COMP_1 |
Specifies the length number of the first corrector. |
MFG_TOOL_COMP_DIST |
Defines the distance between the position of the current corrector
and the tool tip. |
MFG_TOOL_COMP_DIST_1 |
Defines the distance between the position of the first corrector
and the tool tip. |
Geometry parameters are as follows:
NC Commands |
Comments |
MFG_DIAMETER |
Defines the nominal diameter of the tool. |
MFG_NOMINAL_DIAMETER |
Defines the nominal diameter of the machined feature. |
MFG_JUMP_DIST |
Defines the jump distance. |
Computed parameters are as follows (see Figure
1 and Figure 2 above):
NC Commands |
Comments |
MFG_DIAMETER |
Defines the nominal diameter of the tool. |
MFG_NOMINAL_DIAMETER |
Defines the nominal diameter of the machined feature. |
MFG_JUMP_DIST |
Defines the jump distance. |
MFG_DETAIL_DEPTH |
Computes the hole depth that is effectively machined. |
MFG_TOTAL_DEPTH |
Computes the total depth machined by the operation. This includes the
hole depth, breakthrough, and tool tip length. |
MFG_TOTAL_DEPTH_COMP |
Computes the total depth machined by the operation up to the tool
compensation point selected for the operation. This includes hole depth,
breakthrough, and tool tip length up to the compensation point. |
MFG_PLUNGE_DIST |
Whatever the selected plunge mode (by Tip or by Diameter),
this parameter returns the plunge distance. The plunge offset is taken into
account in this value.
|
MFG_CMP_DWL_TIME |
Computes the dwell delay (in time units of seconds): this
parameter is computed if dwell mode is set to 'revolutions'. Otherwise,
the dwell time is returned as is. |
By default,
the syntax is
CYCLE/DRILL,%MFG_TOTAL_DEPTH,%MFG_CLEAR_TIP
NC_LATHE_THREADING General parameters are as follows:
NC Commands |
Comments |
MFG_MO_TYPE |
Defines the machining operation type. |
MFG_MO_IDENTIFIER |
Specifies the machining operation name or identifier. |
MFG_PATTERN_NAME |
Specifies the machining pattern name. |
Machining Strategy parameters are as follows:
NC Commands |
Comments |
MFG_THREAD_MACHINING |
Defines the machining type (1: Constant depth / 2: Section
of cut). |
MFG_THREAD_PENETRATION
|
Defines the penetration (1: Straight / 2: Flank / 3: Alternate). |
MFG_THREAD_UNIT |
Defines the unit (1: Pitch / 2: Thread per inch).
|
MFG_THREAD_PROFILE |
Defines the profile (1: ISO / 2: Trapezoidal / 3: UNC / 4: Gaz).
|
MFG_THREAD_ORIENTATION |
Defines the orientation (1: Internal / 2: External). |
MFG_THREAD_PITCH |
Defines the thread pitch. |
MFG_NUM_THREADS |
Defines the number of threads. |
MFG_THRD_PER_UNIT |
Specifies the threads per inch. |
MFG_FIR_PATH |
Defines the boolean for first passes (0: No / 1: Yes).
|
MFG_LAS_PATH |
Defines the boolean for last passes (0: No / 1: Yes).
|
MFG_SPR_PATH |
Defines the boolean for spring passes (0: No / 1: Yes). |
MFG_NUM_FIR_PATH |
Defines the number of first passes. |
MFG_NUM_LAS_PATH |
Defines the number of last passes. |
MFG_NUM_SPR_PATH |
Defines the number of spring passes. |
MFG_FIR_SECT_CUT |
Defines the section of cut for first passes. |
MFG_LAS_DEPT_CUT |
Defines the depth of cut for last passes. |
MFG_FIR_SECT_RAT |
Defines the section ratio between first passes and next passes. |
MFG_CRES_DIA_CLR |
Defines the clearance on the crest diameter.
|
MFG_ENTER_ANG |
Defines the entry angle. |
MFG_LEAD_IN_DIST |
Defines the lead-in distance. |
MFG_LIFT_OFF_ANG |
Defines the lift-off angle. |
MFG_LIFT_OFF_DIS |
Defines the lift-off distance. |
MFG_SPNDL_UNIT
|
Defines the spindle speed unit. This is done from a list with two values:
- First value: spindle rotation expressed in revolutions per minute.
By default,
the value is RPM.
- Second value: spindle rotation expressed in surface meters per minute.
By default,
the value is SMM.
|
MFG_SPNDL_WAY
|
Defines the spindle direction. This is done from a list with two values:
- First value: spindle rotation processed clockwise.
By default,
the value is CLW.
- Second value: spindle rotation processed counter-clockwise.
By default,
the value is CCLW.
|
MFG_SPNDL_SPEED |
Defines the numerical value of the spindle speed. |
Computed parameters are as follows:
NC Commands |
Comments |
MFG_ST_THRD_AX |
Defines the axial coordinate of the start thread on the crest. |
MFG_ST_THRD_RAD |
Defines the radial coordinate of the start thread on the crest. |
MFG_END_THRD_AX |
Defines the axial coordinate of the end thread on the crest. |
MFG_END_THRD_RAD |
Defines the radial coordinate of the end thread on the crest. |
MFG_END_THRD1_AX |
Defines the axial coordinate of the end thread on the root. |
MFG_END_THRD1_RAD |
Defines the radial coordinate of the end thread on the root. |
MFG_THRD_DEL_RAD |
Defines the depth of thread according to the radial axis. |
MFG_THRD_ANG |
Defines the angle of the thread. If different from zero, this angle
indicates a conical thread. |
MFG_NOM_DIAM |
Defines the nominal diameter of the thread. |
MFG_THRD_LENGTH |
Defines the length of the thread. |
MFG_NB_PATH |
Defines the number of passes. First, last and spring passes are not
included. |
MFG_DEPTH_CUT |
Defines the depth of cut. |
MFG_SECTION_CUT |
Defines the section of cut for passes that follow the first passes. |
MFG_THREAD_DEPTH |
Defines the depth of thread. |
By default,
the syntax is
CYCLE/THREAD,%MFG_THREAD_PITCH
NC_REAMING General parameters are as follows:
NC Commands |
Comments |
MFG_MO_TYPE |
Defines the machining operation type. |
MFG_MO_IDENTIFIER |
Specifies the machining operation name or identifier. |
MFG_PATTERN_NAME |
Specifies the machining pattern name. |
Feeds and Speeds parameters are as follows:
NC Commands |
Comments |
MFG_FEED_APP_MODE |
Specifies the approach feedrate mode (0: Value / 1: Rapid). |
MFG_FEED_APP_VALUE MFG_FEED_APPRCH |
Defines the approach feedrate. |
MFG_FEED_PLUNGE_MODE MFG_FEED_PL_TYPE |
Defines the plunge feedrate mode (0: Value
/ 1: Rapid). |
MFG_FEED_PLUNGE_VALUE MFG_PLUNGE_FEED |
Defines the plunge feedrate. |
MFG_FEED_MACH_VALUE MFG_FEED_MACH |
Defines the machining feedrate. |
MFG_SPINDLE_MACH_VALUE MFG_SPNDL_MACH |
Defines the machining spindle speed. |
MFG_FEED_RETRACT_MODE MFG_FEED_RT_TYPE |
Defines the retract feedrate mode (0: Value
/ 1: Rapid). |
MFG_FEED_RETRACT_VALUE MFG_FEED_RETRACT |
Defines the retract feedrate. |
MFG_FEED_UNIT |
Defines the feedrate unit. |
MFG_SPNDL_UNIT |
Defines the spindle speed unit. |
Machining Strategy parameters are as follows:
NC Commands |
Comments |
MFG_CLEAR_TIP |
Defines the approach clearance. |
MFG_DEPTH_MODE |
Defines the depth mode (1: Tip / 2: Shoulder).
|
MFG_BREAKTHROUGH |
Defines the breakthrough distance. |
MFG_PLUNGE_MODE |
Defines the plunge mode (0: None / 1: Tip / 3: Diameter). |
MFG_PLUNGE_TIP |
Defines the plunge tip distance. |
MFG_PLUNGE_OFFST |
Defines the plunge tip offset. |
MFG_PLUNGE_DIAMETER |
Defines the plunge diameter. |
MFG_DWELL_MODE |
Defines the dwell mode (0: None / 1: By revolutions / 2: By time). |
MFG_DWELL_REVOL |
Defines the dwell delay in revolutions. |
MFG_DWELL_TIME |
Defines the dwell delay in time units (seconds). |
MFG_TOOL_COMP MFG_TL_COMP |
Specifies the length number of current corrector. |
MFG_TOOL_COMP_1 |
Specifies the length number of the first corrector. |
MFG_TOOL_COMP_DIST |
Defines the distance between the position of the current corrector
and the tool tip. |
MFG_TOOL_COMP_DIST_1 |
Defines the distance between the position of the first corrector
and the tool tip. |
Geometry parameters are as follows:
NC Commands |
Comments |
MFG_DIAMETER |
Defines the nominal diameter of the tool. |
MFG_NOMINAL_DIAMETER |
Defines the nominal diameter of the machined feature. |
MFG_JUMP_DIST |
Defines the jump distance. |
Computed parameters are as follows (see Figure
1 and Figure 2 above):
NC Commands |
Comments |
MFG_DETAIL_DEPTH |
Computes the hole depth that is effectively machined. |
MFG_TOTAL_DEPTH |
Computes the total depth machined by the operation. This includes the
hole depth, breakthrough, and tool tip length. |
MFG_TOTAL_DEPTH_COMP |
Computes the total depth machined by the operation up to the tool
compensation point selected for the operation. This includes hole depth,
breakthrough, and tool tip length up to the compensation point. |
MFG_PLUNGE_DIST |
Whatever the selected plunge mode (by Tip or by Diameter),
this parameter returns the plunge distance. The plunge offset is taken into
account in this value.
|
MFG_CMP_DWL_TIME |
Computes the dwell delay (in time units of seconds): this
parameter is computed if dwell mode is set to 'revolutions'. Otherwise,
the dwell time is returned as is. |
By default,
the syntax is
CYCLE/REAM,%MFG_TOTAL_DEPTH,%MFG_CLEAR_TIP
NC_REVERSE_THREADING General parameters are as follows:
NC Commands |
Comments |
MFG_MO_TYPE |
Defines the machining operation type. |
MFG_MO_IDENTIFIER |
Specifies the machining operation name or identifier. |
MFG_PATTERN_NAME |
Specifies the machining pattern name. |
Feeds and Speeds parameters are as follows:
NC Commands |
Comments |
MFG_FEED_APP_MODE |
Specifies the approach feedrate mode (0: Value / 1: Rapid). |
MFG_FEED_APP_VALUE MFG_FEED_APPRCH |
Defines the approach feedrate. |
MFG_FEED_PLUNGE_MODE MFG_FEED_PL_TYPE |
Defines the plunge feedrate mode (0: Value
/ 1: Rapid). |
MFG_FEED_PLUNGE_VALUE MFG_PLUNGE_FEED |
Defines the plunge feedrate. |
MFG_FEED_MACH_VALUE MFG_FEED_MACH |
Defines the machining feedrate. |
MFG_SPINDLE_MACH_VALUE MFG_SPNDL_MACH |
Defines the machining spindle speed. |
MFG_FEED_RETRACT_MODE MFG_FEED_RT_TYPE |
Defines the retract feedrate mode (0: Value
/ 1: Rapid). |
MFG_FEED_RETRACT_VALUE MFG_FEED_RETRACT |
Defines the retract feedrate. |
MFG_FEED_UNIT |
Defines the feedrate unit. |
MFG_SPNDL_UNIT |
Defines the spindle speed unit. |
Machining Strategy parameters are as follows:
NC Commands |
Comments |
MFG_CLEAR_TIP |
Defines the approach clearance. |
MFG_DEPTH_MODE |
Defines the depth mode (1: Tip / 2: Shoulder).
|
MFG_BREAKTHROUGH |
Defines the breakthrough distance. |
MFG_PLUNGE_MODE |
Defines the plunge mode (0: None / 1: Tip / 3: Diameter). |
MFG_PLUNGE_TIP |
Defines the plunge tip distance. |
MFG_PLUNGE_OFFST |
Defines the plunge tip offset. |
MFG_TOOL_COMP MFG_TL_COMP |
Specifies the length number of current corrector. |
MFG_TOOL_COMP_1 |
Specifies the length number of the first corrector. |
MFG_TOOL_COMP_DIST |
Defines the distance between the position of the current corrector
and the tool tip. |
MFG_TOOL_COMP_DIST_1 |
Defines the distance between the position of the first corrector
and the tool tip. |
Geometry parameters are as follows:
NC Commands |
Comments |
MFG_DIAMETER |
Defines the nominal diameter of the tool. |
MFG_THREAD_DIAMETER |
Defines the thread diameter. |
MFG_JUMP_DIST |
Defines the jump distance. |
Computed parameters are as follows (see Figure
1 and Figure 2 above):
NC Commands |
Comments |
MFG_DETAIL_DEPTH |
Computes the hole depth that is effectively machined. |
MFG_TOTAL_DEPTH |
Computes the total depth machined by the operation. This includes the
hole depth, breakthrough, and tool tip length. |
MFG_TOTAL_DEPTH_COMP |
Computes the total depth machined by the operation up to the tool
compensation point selected for the operation. This includes hole depth,
breakthrough, and tool tip length up to the compensation point. |
MFG_PLUNGE_DIST |
Whatever the selected plunge mode (by Tip or by Diameter),
this parameter returns the plunge distance. The plunge offset is taken into
account in this value.
|
MFG_TOOL_PITCH |
Defines the pitch value of the tool. |
By default,
the syntax is
CYCLE/TAP,%MFG_TOTAL_DEPTH,%MFG_CLEAR_TIP
NC_SPOT_DRILLING General parameters are as follows:
NC Commands |
Comments |
MFG_MO_TYPE |
Defines the machining operation type. |
MFG_MO_IDENTIFIER |
Specifies the machining operation name or identifier. |
MFG_PATTERN_NAME |
Specifies the machining pattern name. |
Feeds and Speeds parameters are as follows:
NC Commands |
Comments |
MFG_FEED_APP_MODE |
Specifies the approach feedrate mode (0: Value / 1: Rapid). |
MFG_FEED_APP_VALUE MFG_FEED_APPRCH |
Defines the approach feedrate. |
MFG_FEED_PLUNGE_MODE MFG_FEED_PL_TYPE |
Defines the plunge feedrate mode (0: Value
/ 1: Rapid). |
MFG_FEED_PLUNGE_VALUE MFG_PLUNGE_FEED |
Defines the plunge feedrate. |
MFG_FEED_MACH_VALUE MFG_FEED_MACH |
Defines the machining feedrate. |
MFG_SPINDLE_MACH_VALUE MFG_SPNDL_MACH |
Defines the machining spindle speed. |
MFG_FEED_RETRACT_MODE MFG_FEED_RT_TYPE |
Defines the retract feedrate mode (0: Value
/ 1: Rapid). |
MFG_FEED_RETRACT_VALUE MFG_FEED_RETRACT |
Defines the retract feedrate. |
MFG_FEED_UNIT |
Defines the feedrate unit. |
MFG_SPNDL_UNIT |
Defines the spindle speed unit. |
Machining Strategy parameters are as follows:
NC Commands |
Comments |
MFG_CLEAR_TIP |
Defines the approach clearance. |
MFG_DEPTH_MODE |
Defines the depth mode (1: Tip / 2: Shoulder).
|
MFG_BREAKTHROUGH |
Defines the breakthrough distance. |
MFG_PLUNGE_MODE |
Defines the plunge mode (0: None / 1: Tip / 3: Diameter). |
MFG_PLUNGE_TIP |
Defines the plunge tip distance. |
MFG_PLUNGE_OFFST |
Defines the plunge tip offset. |
MFG_PLUNGE_DIAMETER |
Defines the plunge diameter. |
MFG_DWELL_MODE |
Defines the dwell mode (0: None / 1: By revolutions / 2: By time). |
MFG_DWELL_REVOL |
Defines the dwell delay in revolutions. |
MFG_DWELL_TIME |
Defines the dwell delay in time units (seconds). |
MFG_TOOL_COMP MFG_TL_COMP |
Specifies the length number of current corrector. |
MFG_TOOL_COMP_1 |
Specifies the length number of the first corrector. |
MFG_TOOL_COMP_DIST |
Defines the distance between the position of the current corrector
and the tool tip. |
MFG_TOOL_COMP_DIST_1 |
Defines the distance between the position of the first corrector
and the tool tip. |
Geometry parameters are as follows:
NC Commands |
Comments |
MFG_DIAMETER |
Defines the nominal diameter of the tool. |
MFG_JUMP_DIST |
Defines the jump distance. |
Computed parameters are as follows (see Figure
3 above):
NC Commands |
Comments |
MFG_DETAIL_DEPTH |
Computes the hole depth that is effectively machined. |
MFG_TOTAL_DEPTH |
Computes the total depth machined by the operation. This includes the
hole depth, breakthrough, and tool tip length. |
MFG_TOTAL_DEPTH_COMP |
Computes the total depth machined by the operation up to the tool
compensation point selected for the operation. This includes hole depth,
breakthrough, and tool tip length up to the compensation point. |
MFG_PLUNGE_DIST |
Whatever the selected plunge mode (by Tip or by Diameter),
this parameter returns the plunge distance. The plunge offset is taken into
account in this value.
|
MFG_CMP_DWL_TIME |
Computes the dwell delay (in time units of seconds): this
parameter is computed if dwell mode is set to 'revolutions'. Otherwise,
the dwell time is returned as is. |
By default,
the syntax is
CYCLE/DRILL,%MFG_TOTAL_DEPTH,%MFG_CLEAR_TIP
NC_T_SLOTTING General parameters are as follows:
NC Commands |
Comments |
MFG_MO_TYPE |
Defines the machining operation type. |
MFG_MO_IDENTIFIER |
Specifies the machining operation name or identifier. |
MFG_PATTERN_NAME |
Specifies the machining pattern name. |
Feeds and Speeds parameters are as follows:
NC Commands |
Comments |
MFG_FEED_APP_MODE |
Specifies the approach feedrate mode (0: Value / 1: Rapid). |
MFG_FEED_APP_VALUE MFG_FEED_APPRCH |
Defines the approach feedrate. |
MFG_FEED_PLUNGE_MODE MFG_FEED_PL_TYPE |
Defines the plunge feedrate mode (0: Value
/ 1: Rapid). |
MFG_FEED_PLUNGE_VALUE MFG_PLUNGE_FEED |
Defines the plunge feedrate. |
MFG_FEED_MACH_VALUE MFG_FEED_MACH |
Defines the machining feedrate. |
MFG_SPINDLE_MACH_VALUE MFG_SPNDL_MACH |
Defines the machining spindle speed. |
MFG_FEED_RETRACT_MODE MFG_FEED_RT_TYPE |
Defines the retract feedrate mode (0: Value
/ 1: Rapid). |
MFG_FEED_RETRACT_VALUE MFG_FEED_RETRACT |
Defines the retract feedrate. |
MFG_FEED_UNIT |
Defines the feedrate unit. |
MFG_SPNDL_UNIT |
Defines the spindle speed unit. |
Machining Strategy parameters are as follows:
NC Commands |
Comments |
MFG_CLEAR_TIP |
Defines the approach clearance. |
MFG_DEPTH_MODE |
Defines the depth mode (1: Tip / 2: Shoulder).
|
MFG_DWELL_MODE |
Defines the dwell mode (0: None / 1: By revolutions / 2: By time). |
MFG_DWELL_REVOL |
Defines the dwell delay in revolutions. |
MFG_DWELL_TIME |
Defines the dwell delay in time units (seconds). |
MFG_TOOL_COMP MFG_TL_COMP |
Specifies the length number of current corrector. |
MFG_TOOL_COMP_1 |
Specifies the length number of the first corrector. |
MFG_TOOL_COMP_DIST |
Defines the distance between the position of the current corrector
and the tool tip. |
MFG_TOOL_COMP_DIST_1 |
Defines the distance between the position of the first corrector
and the tool tip. |
Geometry parameters are as follows:
NC Commands |
Comments |
MFG_DIAMETER |
Defines the nominal diameter of the tool. |
MFG_NOMINAL_DIAMETER |
Defines the nominal diameter of the machined feature. |
MFG_LENGTH |
Defines the slot height (= Tool length, which is read on tool). |
MFG_JUMP_DIST |
Defines the jump distance. |
Computed parameters are as follows (see Figure
1 and Figure 2 above):
NC Commands |
Comments |
MFG_DETAIL_DEPTH |
Computes the hole depth that is effectively machined. |
MFG_TOTAL_DEPTH |
Computes the total depth machined by the operation. This includes the
hole depth, breakthrough, and tool tip length. |
MFG_TOTAL_DEPTH_COMP |
Computes the total depth machined by the operation up to the tool
compensation point selected for the operation. This includes hole depth,
breakthrough, and tool tip length up to the compensation point. |
MFG_CMP_DWL_TIME |
Computes the dwell delay (in time units of seconds): this
parameter is computed if dwell mode is set to 'revolutions'. Otherwise,
the dwell time is returned as is. |
By default,
the syntax is
CYCLE/TSLOT,%MFG_TOTAL_DEPTH,%MFG_CLEAR_TIP
NC_TAPPING General parameters are as follows:
NC Commands |
Comments |
MFG_MO_TYPE |
Defines the machining operation type. |
MFG_MO_IDENTIFIER |
Specifies the machining operation name or identifier. |
MFG_PATTERN_NAME |
Specifies the machining pattern name. |
Feeds and Speeds parameters are as follows:
NC Commands |
Comments |
MFG_FEED_APP_MODE |
Specifies the approach feedrate mode (0: Value / 1: Rapid). |
MFG_FEED_APP_VALUE MFG_FEED_APPRCH |
Defines the approach feedrate. |
MFG_FEED_PLUNGE_MODE MFG_FEED_PL_TYPE |
Defines the plunge feedrate mode (0: Value
/ 1: Rapid). |
MFG_FEED_PLUNGE_VALUE MFG_PLUNGE_FEED |
Defines the plunge feedrate. |
MFG_FEED_MACH_VALUE MFG_FEED_MACH |
Defines the machining feedrate. |
MFG_SPINDLE_MACH_VALUE MFG_SPNDL_MACH |
Defines the machining spindle speed. |
MFG_FEED_RETRACT_MODE MFG_FEED_RT_TYPE |
Defines the retract feedrate mode (0: Value
/ 1: Rapid). |
MFG_FEED_RETRACT_VALUE MFG_FEED_RETRACT |
Defines the retract feedrate. |
MFG_FEED_UNIT |
Defines the feedrate unit. |
MFG_SPNDL_UNIT |
Defines the spindle speed unit. |
Machining Strategy parameters are as follows:
NC Commands |
Comments |
MFG_CLEAR_TIP |
Defines the approach clearance. |
MFG_DEPTH_MODE |
Defines the depth mode (1: Tip / 2: Shoulder).
|
MFG_BREAKTHROUGH |
Defines the breakthrough distance. |
MFG_PLUNGE_MODE |
Defines the plunge mode (0: None / 1: Tip / 3: Diameter). |
MFG_PLUNGE_TIP |
Defines the plunge tip distance. |
MFG_PLUNGE_OFFST |
Defines the plunge tip offset. |
MFG_TOOL_COMP MFG_TL_COMP |
Specifies the length number of current corrector. |
MFG_TOOL_COMP_1 |
Specifies the length number of the first corrector. |
MFG_TOOL_COMP_DIST |
Defines the distance between the position of the current corrector
and the tool tip. |
MFG_TOOL_COMP_DIST_1 |
Defines the distance between the position of the first corrector
and the tool tip. |
Geometry parameters are as follows:
NC Commands |
Comments |
MFG_DIAMETER |
Defines the nominal diameter of the tool. |
MFG_THREAD_DIAMETER |
Defines the thread diameter. |
MFG_JUMP_DIST |
Defines the jump distance. |
Computed parameters are as follows (see Figure
1 and Figure 2 above):
NC Commands |
Comments |
MFG_DETAIL_DEPTH |
Computes the hole depth that is effectively machined. |
MFG_TOTAL_DEPTH |
Computes the total depth machined by the operation. This includes the
hole depth, breakthrough, and tool tip length. |
MFG_TOTAL_DEPTH_COMP |
Computes the total depth machined by the operation up to the tool
compensation point selected for the operation. This includes hole depth,
breakthrough, and tool tip length up to the compensation point. |
MFG_PLUNGE_DIST |
Whatever the selected plunge mode (by Tip or by Diameter),
this parameter returns the plunge distance. The plunge offset is taken into
account in this value.
|
MFG_TOOL_PITCH |
Defines the pitch value of the tool. |
By default,
the syntax is
CYCLE/TAP,%MFG_TOTAL_DEPTH,%MFG_CLEAR_TIP
NC_THREAD_WITHOUT_TAP_HEAD General parameters are as follows:
NC Commands |
Comments |
MFG_MO_TYPE |
Defines the machining operation type. |
MFG_MO_IDENTIFIER |
Specifies the machining operation name or identifier. |
MFG_PATTERN_NAME |
Specifies the machining pattern name. |
Feeds and Speeds parameters are as follows:
NC Commands |
Comments |
MFG_FEED_APP_MODE |
Specifies the approach feedrate mode (0: Value / 1: Rapid). |
MFG_FEED_APP_VALUE MFG_FEED_APPRCH |
Defines the approach feedrate. |
MFG_FEED_PLUNGE_MODE MFG_FEED_PL_TYPE |
Defines the plunge feedrate mode (0: Value
/ 1: Rapid). |
MFG_FEED_PLUNGE_VALUE MFG_PLUNGE_FEED |
Defines the plunge feedrate. |
MFG_FEED_MACH_VALUE MFG_FEED_MACH |
Defines the machining feedrate. |
MFG_SPINDLE_MACH_VALUE MFG_SPNDL_MACH |
Defines the machining spindle speed. |
MFG_FEED_RETRACT_MODE MFG_FEED_RT_TYPE |
Defines the retract feedrate mode (0: Value
/ 1: Rapid). |
MFG_FEED_RETRACT_VALUE MFG_FEED_RETRACT |
Defines the retract feedrate. |
MFG_FEED_UNIT |
Defines the feedrate unit. |
MFG_SPNDL_UNIT |
Defines the spindle speed unit. |
Machining Strategy parameters are as follows:
NC Commands |
Comments |
MFG_CLEAR_TIP |
Defines the approach clearance. |
MFG_DEPTH_MODE |
Defines the depth mode (1: Tip / 2: Shoulder).
|
MFG_BREAKTHROUGH |
Defines the breakthrough distance. |
MFG_PLUNGE_MODE |
Defines the plunge mode (0: None / 1: Tip / 3: Diameter). |
MFG_PLUNGE_TIP |
Defines the plunge tip distance. |
MFG_PLUNGE_OFFST |
Defines the plunge tip offset. |
MFG_TOOL_COMP MFG_TL_COMP |
Specifies the length number of current corrector. |
MFG_TOOL_COMP_1 |
Specifies the length number of the first corrector. |
MFG_TOOL_COMP_DIST |
Defines the distance between the position of the current corrector
and the tool tip. |
MFG_TOOL_COMP_DIST_1 |
Defines the distance between the position of the first corrector
and the tool tip. |
Geometry parameters are as follows:
NC Commands |
Comments |
MFG_DIAMETER |
Defines the nominal diameter of the tool. |
MFG_THREAD_DIAMETER |
Defines the thread diameter. |
MFG_NOMINAL_DIAMETER |
Defines the nominal diameter of the machined feature. |
Computed parameters are as follows (see Figure
1 and Figure 2 above):
NC Commands |
Comments |
MFG_DETAIL_DEPTH |
Computes the hole depth that is effectively machined. |
MFG_TOTAL_DEPTH |
Computes the total depth machined by the operation. This includes the
hole depth, breakthrough, and tool tip length. |
MFG_TOTAL_DEPTH_COMP |
Computes the total depth machined by the operation up to the tool
compensation point selected for the operation. This includes hole depth,
breakthrough, and tool tip length up to the compensation point. |
MFG_PLUNGE_DIST |
Whatever the selected plunge mode (by Tip or by Diameter),
this parameter returns the plunge distance. The plunge offset is taken into
account in this value.
|
By default,
the syntax is
CYCLE/TAP,%MFG_TOTAL_DEPTH,%MFG_CLEAR_TIP
NC_THREAD_MILLING General parameters are as follows:
NC Commands |
Comments |
MFG_MO_TYPE |
Defines the machining operation type. |
MFG_MO_IDENTIFIER |
Specifies the machining operation name or identifier. |
MFG_PATTERN_NAME |
Specifies the machining pattern name. |
Feeds and Speeds parameters are as follows:
NC Commands |
Comments |
MFG_FEED_APP_VALUE MFG_FEED_APPRCH |
Defines the approach feedrate. |
MFG_FEED_MACH_VALUE MFG_FEED_MACH |
Defines the machining feedrate. |
MFG_SPINDLE_MACH_VALUE MFG_SPNDL_MACH |
Defines the machining spindle speed. |
MFG_FEED_RETRACT_MODE MFG_FEED_RT_TYPE |
Defines the retract feedrate mode (0: Value
/ 1: Rapid). |
MFG_FEED_RETRACT_VALUE MFG_FEED_RETRACT |
Defines the retract feedrate. |
MFG_FEED_UNIT |
Defines the feedrate unit. |
MFG_SPNDL_UNIT |
Defines the spindle speed unit. |
Machining Strategy parameters are as follows:
NC Commands |
Comments |
MFG_THREAD_STRATEGY |
Defines the thread milling mode (1: Mono-pass / 2: Optimized
passes). |
MFG_THREAD_DIRECTION |
Defines the thread milling direction (1: Top to bottom / 2: Bottom
to top). |
MFG_CLEAR_TIP |
Defines the approach clearance. |
MFG_BREAKTHROUGH |
Defines the breakthrough distance. |
MFG_TOOL_COMP MFG_TL_COMP |
Specifies the length number of current corrector. |
MFG_TOOL_COMP_1 |
Specifies the length number of the first corrector. |
MFG_TOOL_COMP_DIST |
Defines the distance between the position of the current corrector
and the tool tip. |
MFG_TOOL_COMP_DIST_1 |
Defines the distance between the position of the first corrector
and the tool tip. |
Geometry parameters are as follows:
NC Commands |
Comments |
MFG_DIAMETER |
Defines the nominal diameter of the tool. |
MFG_JUMP_DIST |
Defines the jump distance. |
MFG_THREAD_DIAMETER |
Defines the thread diameter. |
MFG_PITCH |
Defines the pitch. |
MFG_PITCH_SENS MFG_PITCH_WAY_OF_ROT |
Defines the thread direction (1: Left-hand /
2: Right-hand).
|
Computed parameters are as follows (see Figure
1 and Figure 2 above):
NC Commands |
Comments |
MFG_DETAIL_DEPTH |
Computes the hole depth that is effectively machined. |
MFG_TOTAL_DEPTH |
Computes the total depth machined by the operation. This includes the
hole depth, breakthrough, and tool tip length. |
MFG_TOTAL_DEPTH_COMP |
Computes the total depth machined by the operation up to the tool
compensation point selected for the operation. This includes hole depth,
breakthrough, and tool tip length up to the compensation point. |
MFG_TOOL_PITCH |
Defines the pitch value of the tool. |
By default,
the syntax is
CYCLE/THREADMILLING,%MFG_TOTAL_DEPTH,
%MFG_CLEAR_TIP
NC_TWO_SIDES_CHAMFERING General parameters are as follows:
NC Commands |
Comments |
MFG_MO_TYPE |
Defines the machining operation type. |
MFG_MO_IDENTIFIER |
Specifies the machining operation name or identifier. |
MFG_PATTERN_NAME |
Specifies the machining pattern name. |
Feeds and Speeds parameters are as follows:
NC Commands |
Comments |
MFG_FEED_APP_MODE |
Specifies the approach feedrate mode (0: Value / 1: Rapid). |
MFG_FEED_APP_VALUE MFG_FEED_APPRCH |
Defines the approach feedrate. |
MFG_FEED_PLUNGE_MODE MFG_FEED_PL_TYPE |
Defines the plunge feedrate mode (0: Value
/ 1: Rapid). |
MFG_FEED_PLUNGE_VALUE MFG_PLUNGE_FEED |
Defines the plunge feedrate. |
MFG_FEED_MACH_VALUE MFG_FEED_MACH |
Defines the machining feedrate. |
MFG_SPINDLE_MACH_VALUE MFG_SPNDL_MACH |
Defines the machining spindle speed. |
MFG_FEED_RETRACT_MODE MFG_FEED_RT_TYPE |
Defines the retract feedrate mode (0: Value
/ 1: Rapid). |
MFG_FEED_RETRACT_VALUE MFG_FEED_RETRACT |
Defines the retract feedrate. |
MFG_FEED_UNIT |
Defines the feedrate unit. |
MFG_SPNDL_UNIT |
Defines the spindle speed unit. |
Machining Strategy parameters are as follows:
NC Commands |
Comments |
MFG_CLEAR_TIP |
Defines the approach clearance. |
MFG_CLEAR_TIP_2 |
Defines the second approach clearance. |
MFG_DEPTH_MODE |
Defines the depth mode (1: Tip / 2: Shoulder).
|
MFG_PLUNGE_MODE |
Defines the plunge mode (0: None / 1: Tip / 3: Diameter). |
MFG_PLUNGE_TIP |
Defines the plunge tip distance. |
MFG_PLUNGE_OFFST |
Defines the plunge tip offset. |
MFG_PLUNGE_DIAMETER |
Defines the plunge diameter. |
MFG_DWELL_MODE |
Defines the dwell mode (0: None / 1: By revolutions / 2: By time). |
MFG_DWELL_REVOL |
Defines the dwell delay in revolutions. |
MFG_DWELL_TIME |
Defines the dwell delay in time units (seconds). |
MFG_TOOL_COMP MFG_TL_COMP |
Specifies the length number of current corrector. |
MFG_TOOL_COMP_1 |
Specifies the length number of the first corrector. |
MFG_TOOL_COMP_DIST |
Defines the distance between the position of the current corrector
and the tool tip. |
MFG_TOOL_COMP_DIST_1 |
Defines the distance between the position of the first corrector
and the tool tip. |
Geometry parameters are as follows:
NC Commands |
Comments |
MFG_DIAMETER |
Defines the nominal diameter of the tool. |
MFG_NOMINAL_DIAMETER |
Defines the nominal diameter of the machined feature. |
MFG_JUMP_DIST |
Defines the jump distance. |
Computed parameters are as follows (see Figure
1 and Figure 2 above):
NC Commands |
Comments |
MFG_DETAIL_DEPTH |
Computes the hole depth that is effectively machined. |
MFG_TOTAL_DEPTH |
Computes the total depth machined by the operation. This includes the
hole depth, breakthrough, and tool tip length. |
MFG_TOTAL_DEPTH_COMP |
Computes the total depth machined by the operation up to the tool
compensation point selected for the operation. This includes hole depth,
breakthrough, and tool tip length up to the compensation point. |
MFG_PLUNGE_DIST |
Whatever the selected plunge mode (by Tip or by Diameter),
this parameter returns the plunge distance. The plunge offset is taken into
account in this value.
|
MFG_CMP_DWL_TIME |
Computes the dwell delay (in time units of seconds): this
parameter is computed if dwell mode is set to 'revolutions'. Otherwise,
the dwell time is returned as is. |
By default,
the syntax is
CYCLE/DRILL,%MFG_TOTAL_DEPTH,%MFG_CLEAR_TIP,%MFG_FEED_MACH,
&MFG_FEED_UNIT

Probing Operations
You can insert PP Words for Probing operations.
Parameters for Probing OperationsSee Probing Operations and Parameters > Probing Operations in Prismatic
Machining User's Guide for more information.
NC Commands |
Comments |
MFG_PROBING_CONTACT_DEPTH |
Defines the depth
of penetration of the stylus into the material. |
MFG_PROBING_DEPTH_DST |
Defines the depth Distance.
By default,
the value is 0mm.
|
MFG_PROBING_DIRECTION_X MFG_PROBING_DIRECTION_Y MFG_PROBING_DIRECTION_Z |
Defines the probing direction, i.e. direction of the first probing.
By default,
the value is 1., 0., 0.
|
MFG_PROBING_DIST_PROBE |
Defines the distance between
the first and the second probing points. |
MFG_PROBING_FIRST_PROBE |
Defines the distance between
the corner and the first probing point. |
MFG_PROBING_HOLE_DIAMETER |
Defines the theoretical diameter.
By default,
the value is 0.mm.
|
MFG_PROBING_NB_PROB |
Defines the number of
probing points.
By default,
the value is 4. It must be greater than 0.
|
MFG_OFFSET_ON_TOP_PLANE |
Defines the offset on the top plane.
By default,
the value is 0.mm.
|
MFG_PROBING_RETURN_BY_MIDLE |
After each probe, the retract goes
through the middle of the hole (or the pin). |
MFG_PROBING_RETURN_BY_TOP_PLANE |
After each probe, the retract goes
through the top plane. |
MFG_PROBING_SAFETY_DST |
Defines the safety distance.
By default,
the value is 10.mm.
|
MFG_PROBING_SECURITY_DST |
Defines the distance before contact with part that requires to change the feedrate in probing
feedrate.
By default,
the value is 5mm.
|
MFG_PROBING_SIDE |
Defines the probing side. |
MFG_PROBING_SLOT_WIDTH |
Defines the theoretical width. |
MFG_PROBING_TOLERANCE |
Defines the probing
tolerance used in the computation of the tool path. |
Examples:
- Hole Probing operation: PPTable:
*START_NC_INSTRUCTION NC_PROBING_HOLE
*START_SEQUENCE
CYCLE/HOLE_PROBING,
%MFG_PROBING_NB_PROB, %MFG_PROBING_HOLE_DIAMETER, %MFG_PROBING_SAFETY_DST, %MFG_PROBING_DEPTH_DST, %MFG_OFFSET_ON_TOP_PLANE,
%MFG_PROBING_DIRECTION_X, %MFG_PROBING_DIRECTION_Y, %MFG_PROBING_DIRECTION_Z
*END
*END Generated APT File: The selected point coordinates are (0.0, 10.0, 0.0).$$ OPERATION NAME: Hole Probing.1
$$ Start generation of: Hole Probing.1
LOADTL/1,1
TLAXIS/ 0.00, 0.00, 1.00
SPINDL/ 0.00,RPM,CLW
RAPID
GOTO / 0.00, 10.00, 10.00
CYCLE/HOLE_PROBING, 4, 10.00, 10.00, 5.00, 0.00, 1.00, 0.00, 0.00
GOTO / 0.00, 10.00, 20.00
CYCLE/OFF
$$ End of generation of: Hole Probing.1
- Slot Probing operation: PPTable:
*START_NC_INSTRUCTION NC_PROBING_SLOT
*START_SEQUENCE
CYCLE/SLOT_PROBING, %MFG_PROBING_SLOT_WIDTH,
%MFG_PROBING_SAFETY_DST,
%MFG_PROBING_DEPTH_DST, %MFG_OFFSET_ON_TOP_PLANE,
%MFG_PROBING_DIRECTION_X, %MFG_PROBING_DIRECTION_Y,
%MFG_PROBING_DIRECTION_Z
*END
*END
Generated APT File: $$ OPERATION NAME: Slot Probing.1
$$ Start generation of: Slot Probing.1
LOADTL/1,1
TLAXIS/ 0.00, 0.00, 1.00
SPINDL/ 0.00,RPM,CLW
RAPID
GOTO / 0.00, 10.00, 10.00
CYCLE/SLOT_PROBING, 10.00, 10.00, 5.00, 0.00, 1.00, 0.00,
0.00
GOTO / 0.00, 10.00, 20.00
CYCLE/OFF
$$ End of generation of: Slot Probing.1
- Corner Probing operation: PPTable:
*START_NC_INSTRUCTION NC_PROBING_CORNER
*START_SEQUENCE
CYCLE/INT_CORNER_PROBING, %MFG_PROBING_SAFETY_DST, %MFG_PROBING_DEPTH_DST,
%MFG_OFFSET_ON_TOP_PLANE
*END
*END Generated APT File: All macro motions are deactivated. $$ OPERATION NAME: Int. Corner Probing.1
$$ Start generation of: Int. Corner Probing.1
LOADTL/1,1
TLAXIS/ 0.000000, 0.000000, 1.000000
SPINDL/ 0.0000,RPM,CLW
RAPID
GOTO / 0.00000, 10.00000, 10.00000
CYCLE/INT_CORNER_PROBING, 10.00000, 5.00000, 0.00000
GOTO / 0.00000, 10.00000, 20.00000
CYCLE/OFF
$$ End of generation of: Int. Corner Probing.1
- Multi-Points Probing operation: PPTable:
*START_NC_INSTRUCTION NC_PROBING_MULTIPOINTS
*START_SEQUENCE
VERIFY/ MULTI_PROBING, %MFG_PROBING_SAFETY_DST
*END
*END Generated APT File: All macro motions are deactivated. $$ OPERATION NAME: Multi Probing.1
$$ Start generation of: Multi Probing.1
LOADTL/1,1
TLAXIS/ 0.000000, 0.000000, 1.000000
SPINDL/ 0.0000,RPM,CLW
RAPID
GOTO / 0.00000, 10.00000, 10.00000
CYCLE/MULTI_PROBING, 10.00000, 5.00000, 0.00000
GOTO / 17.64900, 70.69300, 30.58600, -0.40615, 0.26639, 0.87411
GOTO / 59.80300, 68.11100, 39.42300, 0.07485, 0.26853, 0.96035
GOTO / 20.88300, 27.77500, 31.39400, -0.31938, -0.28117, 0.90496
CYCLE/OFF
$$ End of generation of: Multi Probing.1
|