From any product:
- Select .
A PPR context with an empty Machining Cell is created. An empty Activities Process Tree opens automatically.
- Create a generic machine or assign a machine from the database.
As soon as a machine is assigned to the Machining Cell, a Part Operation and a Manufacturing Program are created in the Activities Process Tree.
- Alternatively, open an existing Machining Process or PPR context .
By default,
the
Activities Process Tree opens
automatically.
Activate the Manufacturing Program.
- Click
Axial Machining Operations.
- Click
Drilling in the sub-toolbars that appear.
- Go to the Macros tab
in the Machining Operation dialog box that appears.
The initial status of all the macros in the Macro Management
list is Inactive
.
Right-click the Approach
macro line and select Activate in the contextual menu.
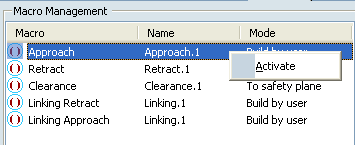
The macro line is activated.
turns to
, meaning some definition data exist but may require modifications.
In the Current Macro Toolbox, select
Add Axial Motion
.
A sensitive icon representing the elementary paths of
the macro appears.
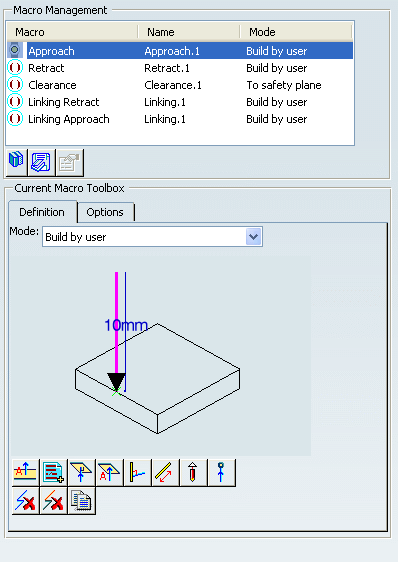
Double-click 10mm to edit the distance (to 30mm, for example).
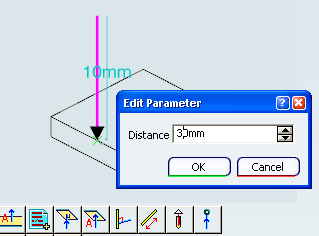
The yellow light turns to green, meaning the data are up-to-date.
Click Tool Path Replay
to check the axial approach.
Under Macro Management, as you did above:
- Activate the Retract
macro line, and create a 30mm axial retract motion.
- Activate the Linking Retract
macro line, and create a 25mm
axial retract motion.
The Linking Approach/Retract macros have a common behavior and are seen as the same object. It allows to handle Activate/Deactivate for both Approach and Retract. Consequently, they share the same name and it is not possible to rename one independently from the other.
- Create a 25mm axial
motion for the Linking Approach macro
- Click Tool Path Replay
to check the defined motions.
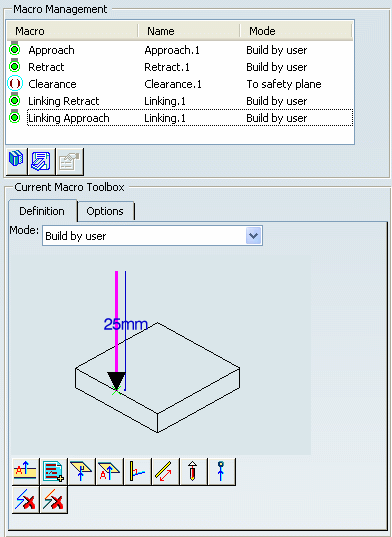
Note:
If a jump distance is defined
in the Machining Operation, it is used in preference to the
linking macro. Similarly if local entry/exit distances
are defined on the Machining Operation, they are used in preference
to the linking macro.
Click Tool Path Replay
to validate the tool path.
- In the Replay dialog box,
select the Different colors mode
in order to visualize feedrate changes. See Color Modes.
The tool path
is displayed with the following default colors:
- Yellow: approach feedrate
- Green: machining feedrate
- Blue: retract feedrate
- Red: Rapid feedrate
- Purple: plunge feedrate
- White: local feedrate.
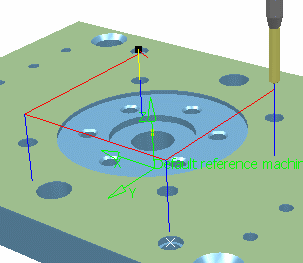
Click OK to validate and exit the dialog box.
The Machining Operation is
updated with the specified macros.