Create and Edit a Part Operation
You can access and create a Part Operation in the Activities Process Tree.
From any product or 3D part: - Select .
A PPR context with an empty Machining Cell is created. An empty Activities Process Tree opens automatically.
- Create a generic machine or assign a machine from the database.
As soon as a machine is assigned to the Machining Cell, a Part Operation and a Manufacturing Program are created in the Activities Process Tree.
- Alternatively, open an existing Machining Process or PPR context .
By default,
the
Activities Process Tree opens
automatically.
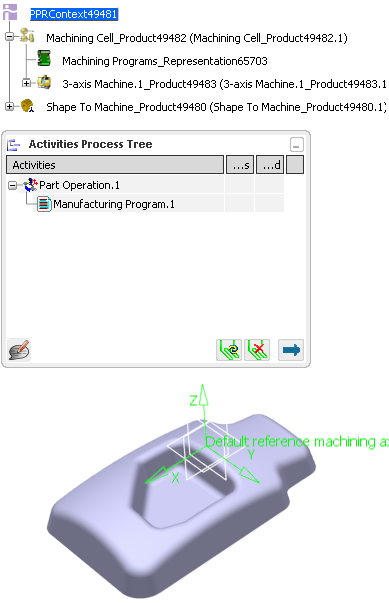
If you need to add a Part Operation, click .
Double-click the Part Operation in the Activities Process Tree. The dialog box to edit a Part Operation varies depending on the type of the machine. - When the assigned machine is a milling machine, the Part Operation dialog box is:
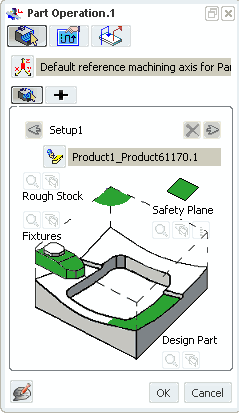
- When the assigned machine is a millturn machine, the Part Operation dialog box is:
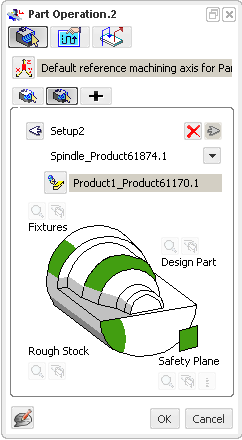
Optional: Click to edit the Part Operation Name and assign Comments to the
Part Operation.
Optional: Edit the Setup, Options, and Transition Path tabs.
Click Analyse to open the Geometry Analyser dialog box containing the selected geometry points.
Click Rest all selections to reset all geometry selections in the authoring window
Click Show/Hide the offset to show/hide the offsets in authoring window.

Assign a Reference Machining Axis System
You can assign a reference machining axis system to the Part Operation.
Click Reference Machining Axis
System
.
The Machining Axis System dialog
box is displayed.
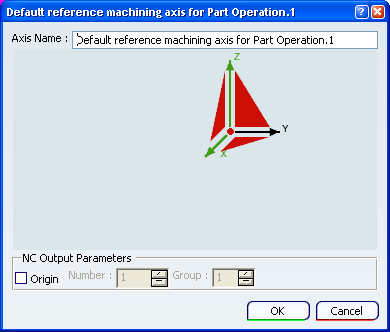
See
Inserting Machining Axis Changes
Note:
- Output coordinates can be expressed
in the reference machining axis system.
- If a local machining
axis system is inserted in the Manufacturing Program, coordinates
can be expressed in the local axis system.

Define the Setup of the Part Operation
You can define the geometry of the Setup Assembly, the Design, the Stock, Check elements and Safety planes from the Setup tab.
Go to the Setup tab .
Assign an existing setup assembly to the
Part Operation.
- Click Setup Assembly
to
associate an existing setup assembly to the Part Operation. The icon turns to .
- When needed, click
to remove the currently associated setup assembly. The icon turns back to .
Click Design Part
then select the desired geometry.
See Comparing Machined Stock Part and Design Part for more information. The geometry of the design part is associated to the Part Operation. This is useful for material removal simulations.
Click
Rough Stock
then select the desired geometry.
See also Intermediate Stock. A rough stock is associated to the Part Operation. This is useful for some Surface
Machining Operationsand also for
material removal simulations.
Click
Fixtures
then select the desired geometry.
Fixtures are associated to the Part Operation. This is useful if you want to do
material removal simulations later.
Click Safety Plane
then select the desired plane. This plane is associated to the Part Operation, as its global safety plane.
Click + to add a Setup. A Setup tab is added.
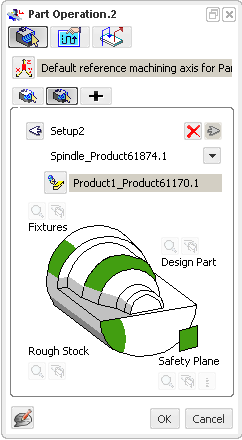
Click the left or right arrow to modify the order of the existing setups.
Click the red cross to delete an existing setup.
Right-click Reference Machining Axis
System
on Part Operation Setup tab:
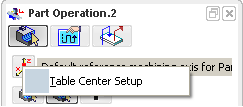
Click Table Center Setup and modify the reference positions.
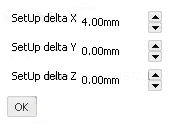
Click OK.

Edit the Options of the Part Operation
You can edit several options of the Part Operation from the Option tab.
Go to the Option tab . Only the relevant options are selectable.
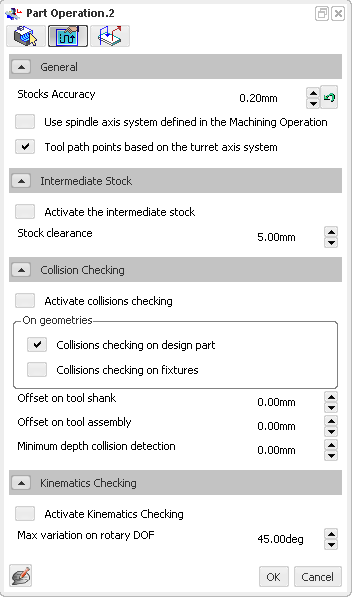
In General - Define the value of the Stocks Accuracy.
The Stock Accuracy is the tolerance used to compute tessellations for photo/video simulations.
By default,
the Stock Accuracy is set to 0.2 mm.
- Click
to revert to the default value.
- Select the required check boxes:
- Use Spindle Axis System
defined
in the Machining Operation: when selected, computes the tool
tip points based on
the spindle that is set on the Machining Operation.
If this check box is not selected,
the main spindle axis is used. This
is determined by the default reference
machining axis system set on the
Part Operation.
Note:
You must select a multi-slide lathe machine or a
mill-turn machine.
- Toolpath points based on the turret axis system: when selected, computes the tool path points shown in the Tool Path Replay dialog box and APT output based on the turret axis system for Lathe Operations.
By default,
this check box is cleared and the tool path points shown in Tool Path Replay dialog box and APT output are computed with respect to Part Operation axis system, in the spindle plane.
In Intermediate Stock - Select Activate the intermediate stock check box to enable the automatic computation of the
intermediate stock.
The computed stock is taken into account for
tool path computation. A clearance can be assigned to the stock.
- Define the value of the Stock Clearance.
By default,
the Stock Clearance is set to 5.00 mm.
In Collision Checking - Select the Activate collisions checking check box to get quick
feedback about collisions during
the Tool Path Replay.
Notes:
- The options in this tab are available for Milling
operations only.
- Barrel tools and boring bars are not
supported.
- For more information, see Collision Checking.
The collisions checking parameters become available.
- Select the On design
part check box to detect
collisions between the tool/tool
holder and the design part specified
in the Part Operation
Geometry tab.
- Select the On fixtures
check box to detect collisions
between the tool/tool holder
and the fixtures specified in
the Part Operation Geometry
tab.
- Optional: Set offsets
on the tool or tool assembly,
which are used as safety distances.
- Set the Minimum depth collision detection value.
Applying negative offsets on part surfaces or drive curves or surfaces leads to the detection of too many collisions, with the display of unwanted warnings. Setting the Minimum depth collision detection enables you to set a threshold under which collisions are not detected nor displayed. While Minimum depth collision detection has no maximum value, it cannot be greater than the tool corner radius defined in the Machining Operation.
By default,
these values are set to 0mm.
In Kinematics Checking - Select the Activate Kinematics Checking to consider Machine kinematics constraints at tool path computation time.
- Define the value of the Max Variation on Rotary DOF.
By default,
the Max Variation on Rotary DOF is set to 45.00 deg.
Define the value of the Stocks Accuracy. The Stock Accuracy is the tolerance used to compute tessellations for photo/video simulations.
By default,
the Stock Accuracy is set to 0.2 mm.
Click to revert to the default value.
Select the required check boxes: - Use Spindle Axis System
defined
in the Machining Operation: when selected, computes the tool
tip points based on
the spindle that is set on the Machining Operation.
If this check box is not selected,
the main spindle axis is used. This
is determined by the default reference
machining axis system set on the
Part Operation.
Note:
You must select a multi-slide lathe machine or a
mill-turn machine.
- Toolpath points based on the turret axis system: when selected, computes the tool path points shown in theTool Path Replay dialog box and APT output based on the turret axis system for Lathe Operations.
By default,
this check box is cleared and the tool path points shown in Machining Operation dialog box and APT output are computed with respect to Part Operation axis system, in the spindle plane.

Activate the Generation of Transition Paths
Except for a mill-turn or a lathe machine, you can activate the generation of transition paths from the Transition Path tab.
Go to the Transition Path tab .
Select the Activate the generation Transition Paths check box. The icons used to specify the required geometry become available.
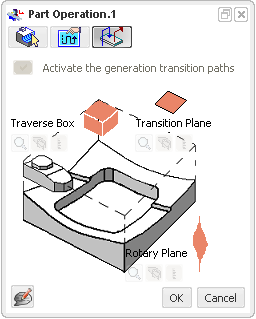
Note:
When the check box Generate Transition Path
- is selected, the Manufacturing Program contextual menu items Generate Machine Rotations and
Delete Generated Machine
Rotations
are
not available. All the generated machine rotations are removed from the Activities Process Tree.
- is cleared, the Manufacturing Program contextual menu items Generate Machine Rotations and
Delete Generated Machine
Rotations
are available
.
- See Inserting Machine Rotations.
Click Traverse Box Plane, then select five planes that define a global traverse
box for the Part Operation.
Click Transition Plane, then select the planes that can be used as a
global transition planes for the Part Operation.
Click Rotary Plane, then select the planes that can be used as a
global rotary planes for the Part Operation.
|