Open a typical part with two grooves to machine like the one shown below:

Activate the Manufacturing Program and click
Sequential Groove
in the Axial Machining Operations toolbar.
A Sequential Groove entity is added to the Manufacturing Program.
The Sequential Groove dialog box appears directly
at the Geometry tab
. This tab includes a sensitive icon to
help you specify the
geometry.
Areas of the icon are colored red indicating that this
geometry is required
Still in the Geometry tab.
See Selecting Geometry
- Go to the Global tab to define the
hole geometry to machine.
- Select the red groove depth representation
in the sensitive icon, then select the two holes in
the part.
- Set the Number of levels
to 2.
- Double click to end your selections.
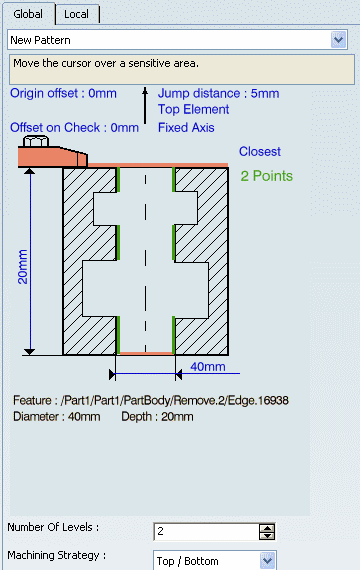
- Go to the Local tab
to define the machining planes to reach.
- For Level Number 1, select the plane representations
in the sensitive icon, and the planes of the first groove
in the part.
The Local tab is updated as shown below.
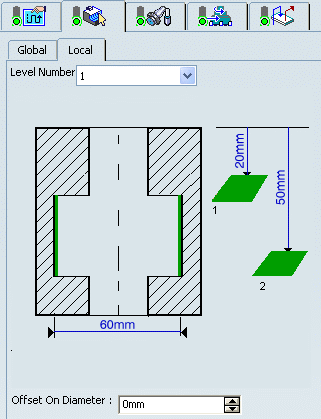
- For Level number 2, select the appropriate planes of
the second groove in the part.
Select the Strategy tab
,
which comprises two tabs Motions (to define the
elementary motions making up the machining operation) and Strategy.
- Go to the Motions tab.
- Click Go to Plane
,
then define a Go to Plane motion to Plane 1 and a Local
Feedrate of 50mm/mn. Set Compensation to 2.
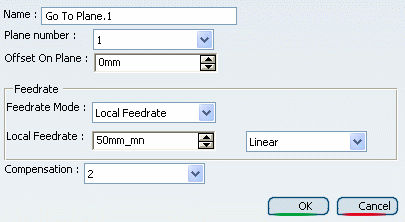
- Click OK to add the first tool motion in the list in
the Sequential Groove dialog box.
- Click Circular
,
then define a circular motion
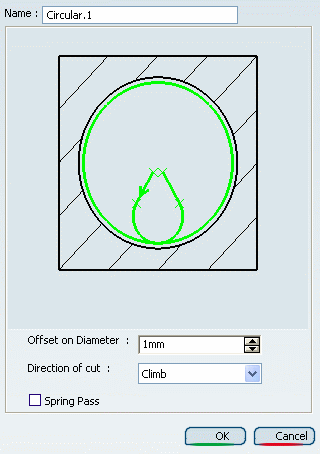
- If necessary, adjust the
radius of the circular approach (and circular retract)
portion of this motion to be compatible with the groove
and tool radius values.
- Right-click the circular arc in
the icon, and set the radius parameter to 5mm.
- Click
OK to add the motion in the list
- Click Go to Plane
,
then define a Go to Plane motion to Plane 2 and a Local
Feedrate of 50mm/mn. Set Compensation to 1.

- Click OK to add the tool motion in the list.
- Insert other motions as follows:
Circular motion with Feedrate=Machining
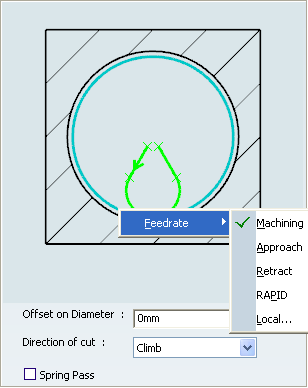
Go to Clearance motion with
Local Feedrate of 500mm/mn.
Right-click this motion in the list
and set the Application mode
to Last level.
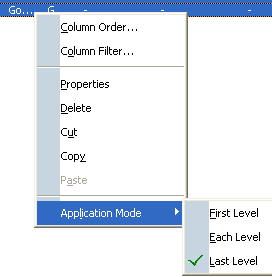
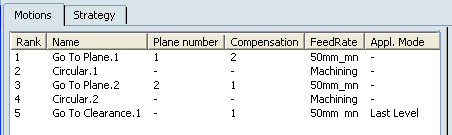
- Go to the Strategy tab
.
- Specify machining parameters such as Approach
clearance.
- Make sure the Compensation application mode
is set to Guiding Point.
Go to the Tool tab
to select a tool.
See Specifying a Tool Element in a Machining Operation
- Select a T-slotter tool and set the nominal diameter
to a value less that 40mm (so that the tool can pass
through the top of the hole).
- Click More >> and go to the Compensation tab to specify a second corrector
P2 as follows:
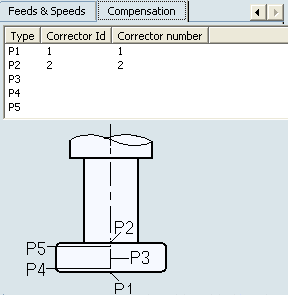
Select the
Feeds and Speeds tab
to
specify the feedrates and spindle speeds for the operation.
Select the
Macros tab
to specify the desired transition paths.
See Defining Macros on Axial Machining Operations
Click Tool Path Replay
to check the validity of the operation.
See Replaying the Tool Path
- The tool path is computed.
- A progress indicator is displayed.
- You can cancel the tool path computation at any moment before 100%
completion.
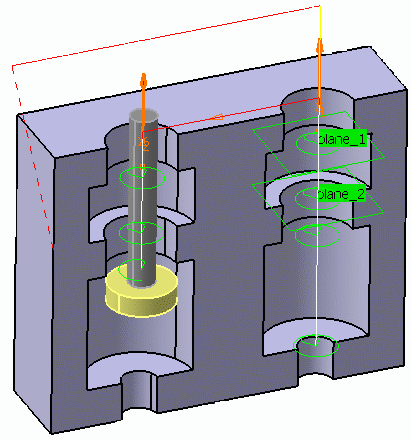
Click OK to create the
operation.