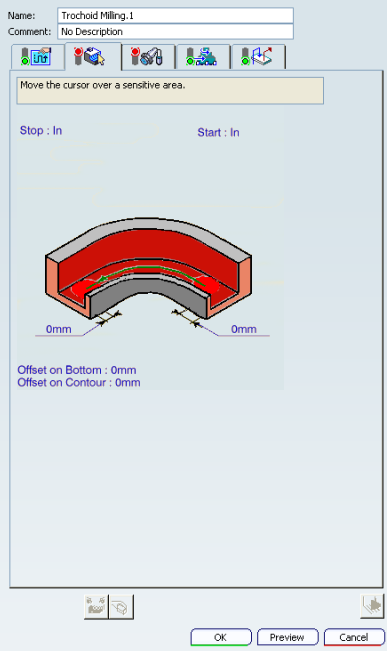

Stepover Parameters
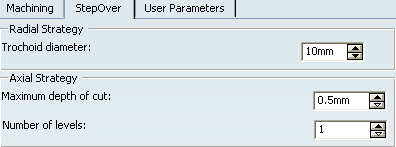
- Trochoid diameter
- Specifies
the diameter of the trochoidal motion (B in below image), which corresponds to the
width of the slot to machine.
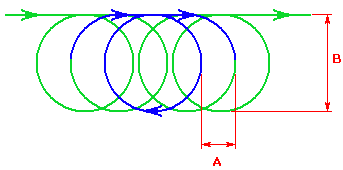
- Maximum depth of cut
- Defines
the maximum depth of cut in an axial strategy.
- Number of levels
- Defines
the number of levels to be machined in an axial strategy.

Geometry
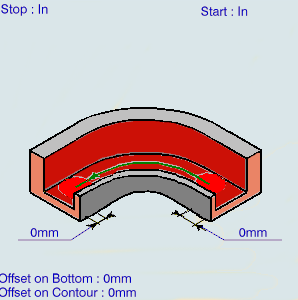
You can specify the following Geometry:
- Bottom (planar face or surface) with possible Offset on
Bottom.
- Guide contour (edges only) with possible Offset on
Contour.
- Start and Stop relimiting elements with possible offsets.
See also Selecting Guiding and Relimiting Elements

Feedrates and Speeds Parameters
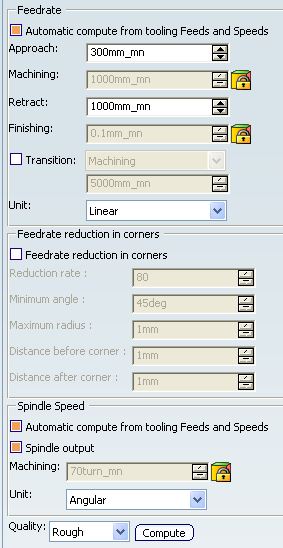
- Feedrate: Automatic compute from tooling Feeds and Speeds
- This check box allow an operation's feeds and speeds values to be updated automatically when the tool's feeds and speeds values are modified.
You can specify the following feedrates:
- Approach
- Machining
- Retract
- Finishing
Note:
The above feedrates can be defined in linear (feed per minute) or angular (feed per revolution)
units.
- Angular: feedrate in revolutions per minute and unit is set to mm_turn.
- Linear: feedrate in feed per minute and unit is set to mm_mn.
- Transition
- You can locally set the feedrate for a transition path to a
machining operation B from a machining operation A or from a tool
change activity. This is done by selecting the Transition check box in the Machining Operation dialog box for
operation B.
For more information, please refer to the Setting a Transition Feedrate.
- Feedrate Reduction in
Corners
You can reduce feedrates in corners encountered along the tool
path depending on values given in the Feeds and Speeds tab page:
- Reduction
rate
- Minimum angle
- Maximum radius
- Distance before corner
- Distance after corner
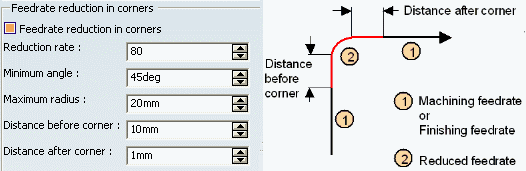
Feed reduction is applied to corners along the tool path whose
radius is less than the Maximum radius value and whose arc angle is
greater than the Minimum angle value. Corners can be angled or
rounded.
For Trochoid Milling, feedrate reduction applies to inside
corners. It does not apply for macros or default linking and return
motions.
If a cornering is defined with a radius of 5mm and the Feedrate
reduction in corners set to a lower radius value, the feedrate cannot be reduced.
Note:
Trochoid milling is an operation that allows to machine hard materials, using a small engagement step. Feedrate reduction cannot be applied to small distances, and thus does not affect trochoid milling.
- Spindle Speed: Automatic compute from tooling Feeds and Speeds
This check box allow an operation's feeds and speeds values to be updated automatically when the tool's feeds and speeds values are modified. If the Feedrate Automatic compute check box is selected
and the Spindle Speed: Automatic compute from tooling Feeds and Speeds check box is not selected, then only the feedrate values can
be computed. If both are not selected then automatic updating
is not done.
When you modify a tool's feeds and speeds, all existing
operations with the Automatic
compute check boxes selected that use this tool (or an
assembly using this tool) can be recomputed.
- Spindle output
- This check box manage output
of the SPINDL instruction in the generated NC data file:
- If the check box is selected, the instruction is generated.
- Otherwise,
it is not generated.
Note:
The spindle speed can be defined in linear (length per minute) or angular (length per revolution)
units.
- Angular: length in revolutions per minute and unit is set to mm_turn.
- Linear: length in feed per minute and unit is set to mm_mn.
- Quality
- The feed and speed values are computed according to the
Quality setting on the operation.
- Compute
- Feeds and speeds of the operation can be updated according to tooling feeds and speeds by clicking the Compute button located in the Feeds and Speeds tab of the operation.
Feeds and speeds of the operation can be updated automatically
according to tooling data and the rough
or finish quality of the operation. This is described
in
About Feeds and Speeds.

NC Macro
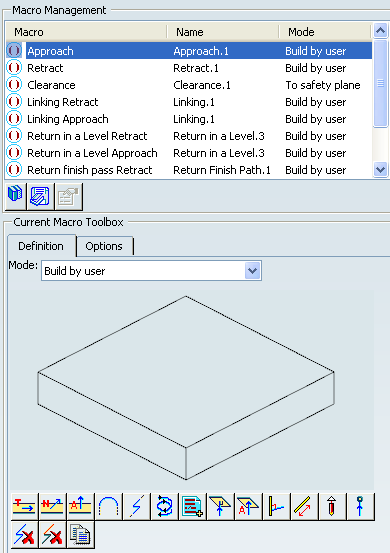
You can define transition paths in your machining operations by means
of NC macros:
- Approach: to approach the operation start point,
- Retract: to retract from the operation end point,
- Linking:
- to link two non consecutive paths
- to access finish and spring passes.
- Return in a Level to link two
consecutive paths in a given level in a multi-path operation
- Return between Levels
to go to the next level in a multi-level machining operation,
- Return to Finish Pass to go
to the finish pass
- Clearance to avoid a fixture,
for example.
The proposed macro mode are:
- None
- Build by user
- Circular horizontal axial
- Horizontal horizontal axial
- Axial
When a collision is detected between the tool and the part
or a check element, a clearance macro is applied automatically. If
applying a clearance macro would also result in a collision, then a
linking macro is applied. In this case, the top plane defined in
the operation is used in the linking macro. The top plane element
must be selected in order to apply an automatic linking macro
without collision. See Defining Macros.
|