
Strategy for Holes or Pins Probing
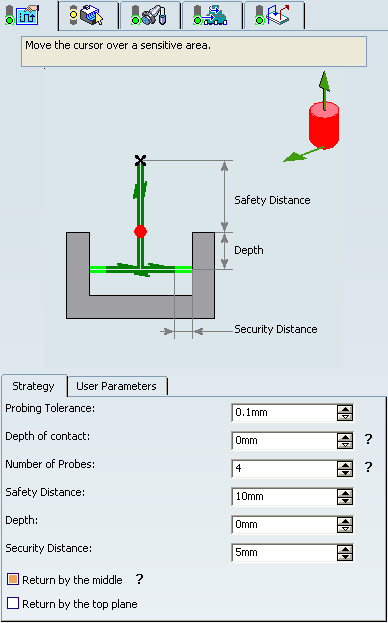
- Tool axis
- Select tool axis in the authoring window.
By default,
the value is 0., 0., 1.
See Defining the Tool Axis
- Probing direction
- Specifies direction of the first probing.
By default,
the value is 1., 0., 0.
- Probing Tolerance
- Specifies probing
tolerance used in the computation of the tool path.
- Depth of contact
- Specifies depth
of penetration of the stylus into the material.
- Number of Probes
- Specifies number of
probing points.
By default,
the value is 4.
The value must be greater than 0.
- Safety Distance
- Specifies safety distance.
By default,
the value is 10.mm.
- Depth
- Specifies depth distance.
By default,
the value is 0.mm, if you select points.
- Security Distance
- Specifies distance before contact with part to change the feedrate in probing
feedrate.
By default,
the value is 5.mm.
- Return by the middle
- When selected, after each probe, the retract goes
through the middle of the hole (or the pin).
Example when the option is activated then deactivated:
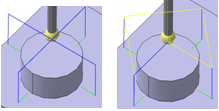
- Return by the top plane
-
- Is available only when Probing Side is set to Probe Inside.
- When selected, after each probe, the retract goes
through the top plane.
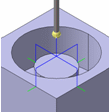

Geometry for Holes or Pins Probing
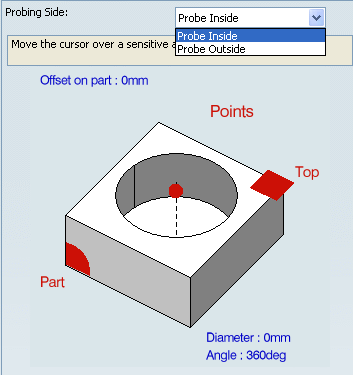
- Probing Side
- List of geometries composed of points (center of holes or pins
to probe) or guides (contour of holes or pins).
You can select points, circles, and cylinders.
- Probe Inside to probe a hole,
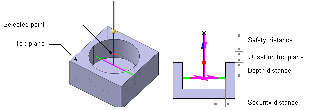
- or Probe Outside to probe a pin.
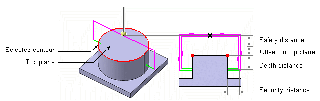
- Diameter
- Specifies diameter.
Double-click Diameter and edit it in the dialog box
that appears.
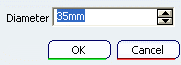
By default,
the value is
0.mm.
- Angle
- Specifies angle.
Double-click Angle and edit it in the dialog box
that appears.
- Top\Part\Points
- Select top, part, and plane in the authoring window.
You can:
- remove your selection and select a new contour,
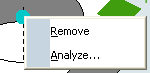
- Modify the geometry, hence the diameter or the angle, and
retrieve the associativity via the contextual menu:
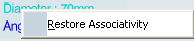
Note:
If the contour of the hole (or pin) is selected, the diameter is
automatically computed and is associated with the geometry.
Its value is displayed in the sensitive icon.
- Offset on Part
- Specifies offset on part.
By default,
the value is
0.

Strategy for Slots or Ribs Probing
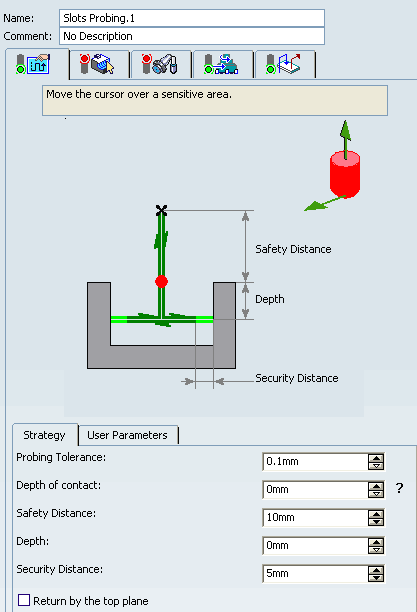
- Tool axis
- Select tool axis in the authoring window.
By default,
the value is 0., 0., 1.
See Defining the Tool Axis
- Probing direction
- Specifies direction of the first probing.
By default,
the value is 1., 0., 0.
- Probing Tolerance
- Specifies probing
tolerance used in the computation of the tool path.
- Depth of Contact
- Specifies depth
of penetration of the stylus into the material.
- Safety Distance
- Specifies safety distance.
By default,
the value is 10.mm.
- Depth
- Specifies depth distance.
By default,
the value is 0.mm.
- Security Distance
- Specifies distance before contact with part to change the feedrate in probing
feedrate.
By default,
the value is 5.mm.
- Return by the top plane
-
- Is available only when Probing Side is set to Probe Inside.
- When selected, after each probe, the retract goes
through the top plane.

Geometry for Slots or Ribs Probing
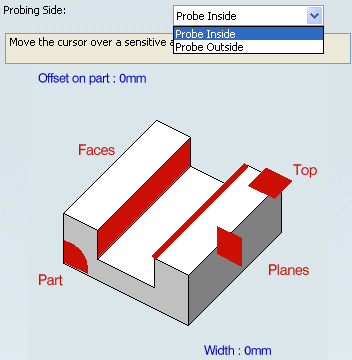
In addition to the two faces or planes which compose the Slot or the Rib, you can define the following. Note:
If the faces of the slot (or rib) are selected, the width is
automatically computed and is associated of the geometry.
- Probing Side
- Speifies the probimg side.
You can specify:
- Probe Inside to probe a slot,
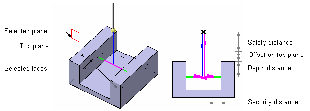
- or Probe Outside to probe a rib.
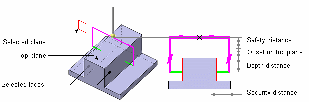
- Offset on Part
- Specifies offset on part.
By default,
the value is
0.
- Width
- Specifies width. Its value is displayed in the sensitive icon.
Double-click Width and edit it in the dialog box
that appears.
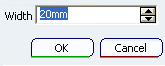
By default,
the value is
0.
- Top\Planes\Part\Faces
- Select top\planes\part\faces in the authoring window.
You can
-
remove your selection and select new faces,
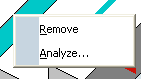
- Modify the geometry, hence the rib or the slot, and retrieve
the associativity via the contextual menu:
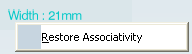

Strategy for Corner Probing
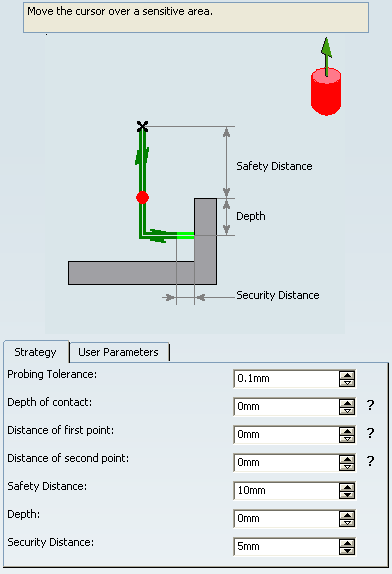
- Tool axis
- Select tool axis in the authoring window.
By default,
the value is 0., 0., 1.
See Defining the Tool Axis
- Probing Tolerance
- Specifies probing
tolerance used in the computation of the tool path.
- Depth of contact
- Specifies depth
of penetration of the stylus into the material.
- Distance of first point
- Defines the distance between
the corner and the first probing point.
- Distance of second point
- Defines the distance between
the first and the second probing points.
- Safety Distance
- Specifies safety distance.
By default,
the value is 10.mm.
- Depth
- Specifies depth distance.
By default,
the value is 0.mm.
- Security Distance
- Specifies distance before contact with part to change the Feedrates in probing
Feedrates.
By default,
the value is 5.mm.

Geometry for Corner Probing
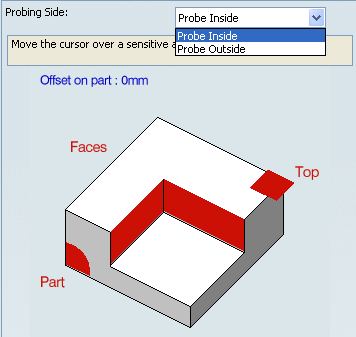
In addition to the two faces which compose the corner, you can define the following:
- Probing Side
- Specifies probing side.
You can specify:
- Probe Inside to probe a internal corner,
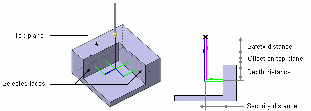
- or Probe Outside to probe an external corner.
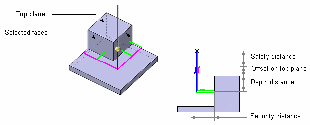
- Offset on Part
- Specifies offset on part.
By default,
the value is
0.
- Top plane/Faces/Part
- Select top plane/faces/part in the authoring window.

Probing User Parameters
This tab page is found in each probing command and works as described in Adding an User Parameter. Probing User parameters can be of the following types:
- String,
- Boolean,
- Integer,
- Real,
- Length,
- Angle.

Feedrates and Speeds
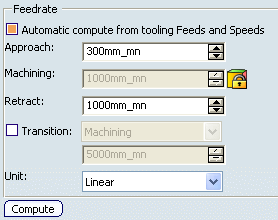

NC Macros
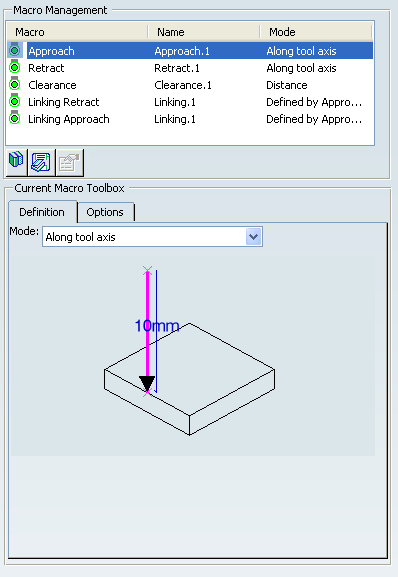
For more information, please refer to the Defining Macros. You can define transition paths in your machining operations by means
of NC macros:
The macros generated in APT file are managed as the drilling
operations. Examples:
- Hole probing of two holes with the Linking macros
deactivated:
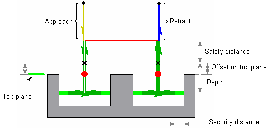
- Strategy Parameters:
- Diameter = 40mm
- Safety Distance = 10mm
- Offset on Top Plane = 2mm
- Depth = 20mm
- Security Distance = 5mm
- Macro Parameters:
- Along Tool Axis - 20mm
- Linking: Deactived
- Retract: Along Tool Axis - 20mm
- Approach:
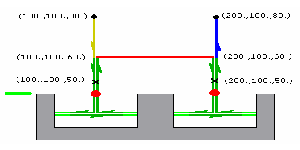
- APT Generated:
$$ Start generation of: Holes Probing.1
RAPID
GOTO / 100.0, 100.0, 80.0, 0.0, 0.0, 1.0
FEDRAT/ 300.0000,MMPM
GOTO / 100.0, 100.0, 60.0, 0.0, 0.0, 1.0
CYCLE/PROBING_HOLE, 40.000000, 10.000000, 2.000000, 20.000000,
5.000000
GOTO / 100.0, 100.0, 50.0, 0.0, 0.0, 1.0
GOTO / 200.0, 100.0, 50.0, 0.0, 0.0, 1.0
CYCLE/OFF
FEDRAT/ 1000.0000,MMPM
GOTO / 200.0, 100.0, 80.0, 0.0, 0.0, 1.0
$$ End of generation of: Holes Probing.1
Edit Cycle Macro
-
Edit cycle is available for all probing commands.
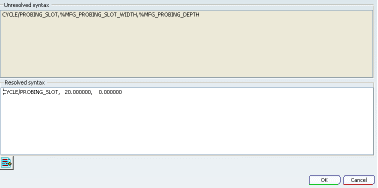
Add PP word list
- lets you add PP Words.
General information about PP Words can be found in PP Tables and PP Word Syntaxes.
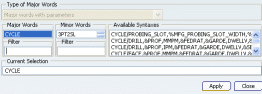
See Defining Macros for more information.
The syntaxes available are:
Probing operation
|
Available syntaxes (where n is a number: 1,2, etc.)
|

Holes or Pins Probing
|
NC_PROBING_HOLE
NC_PROBING_PIN
NC_PROBING_HOLE_n
NC_PROBING_PIN_n
|

Slots or Ribs Probing
|
NC_PROBING_SLOT
NC_PROBING_RIB
NC_PROBING_SLOT_n
NC_PROBING_RIB_n
|

Corner Probing
|
NC_PROBING_CORNER
NC_PROGING_CORNER_n
|

Multi-Points Probing
|
NC_PROBING_MULTI_POINTS
NC_PROBING_MULTI_POINTS_n
|
|