Activate the Manufacturing Program and click Rough Turning
in the Lathe Machining Operations toolbar.
A Rough Turning entity is added to the Manufacturing Program.
The Rough Turning dialog box appears directly at the
Geometry tab
.
Note:
Geometry tab includes a sensitive area to help you specify
the geometry to be machined. The part and stock are colored
red indicating that this geometry is required. All other geometry is
optional.
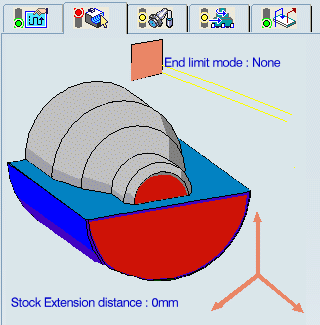
Still in the Geometry tab.
- Click the red part area in the Geometry tab and then select the
desired part profile in the 3D window.
See Selecting Edges and Faces to Define Geometry
The Automatic Link Type option
allows you to select a first element and then
the element to navigate to in order to complete the profile selection.
The Axial/Radial and Radial/Axial Linking options are also useful for
profile selection.
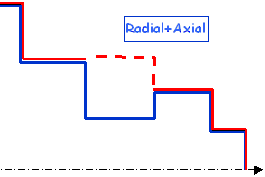
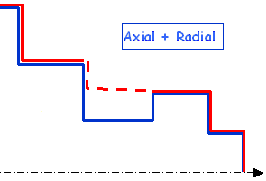
Once selected, the part areas changes color to
green indicating that this geometry is now defined.
- Click the red stock area in the Geometry tab and then select the desired
stock profile in the 3D window.
Once selected, the stock areas changes color to
green indicating that this geometry is now defined.
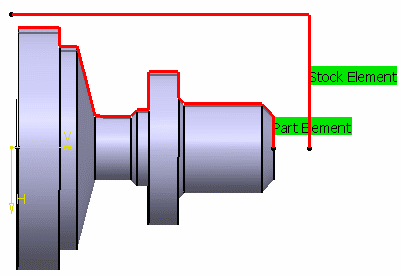
- Right-click the geometry to be assigned the local value,
and select the Add Local Information contextual command.
A
dialog box appears allowing you to assign the desired local
values. In addition to the global offsets that you can assign to the
part profile, you can also add local offset values.
Other contextual commands are available for managing
local information. Please refer to the Managing Local Information for more details.
- Set Part Offset to 5mm.
Select the Strategy tab
.
- Specify the machining strategy parameters.
- Roughing mode: Longitudinal
- Orientation: External
- Location: Front
- Double-click Max depth of cut
Set this value to 2.5mm in the Edit Parameter dialog box and
click OK.
- Set other parameters in the Option and User Parameters tab.
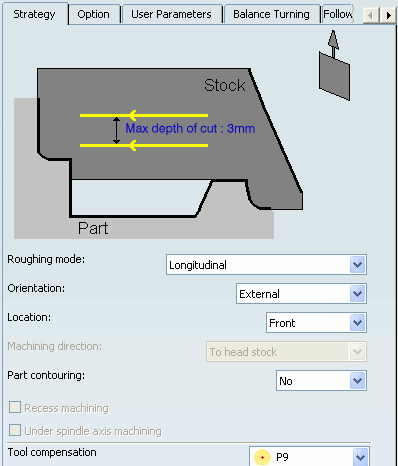
Go to the Tool tab
to select a tool.
See Specifying a Tool Element in a Machining Operation
Select the Feeds and Speeds
tab
to specify the feedrates and spindle speeds for the Machining Operation.
Select the Macros tab
to specify the Machining Operation transition paths.
For more information, please refer to the
Define Macros on a Lathe
Operation.
Click Tool Path Replay
to check the validity of the Machining Operation.
See Replaying the Tool Path
The toolpath is computed.
- The tool path is computed.
- A progress indicator is displayed.
- You can cancel the tool path computation at any moment before 100%
completion.
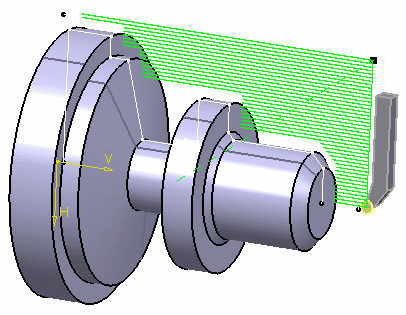
Click OK to create the Machining Operation.