Content according to Macro Mode
The dialog box can have different looks, according to the macro definition mode.
Load from Catalog: load a macro from an existing catalog. Save in Catalog: save a macro in catalog.
- In the Graphic Mode:
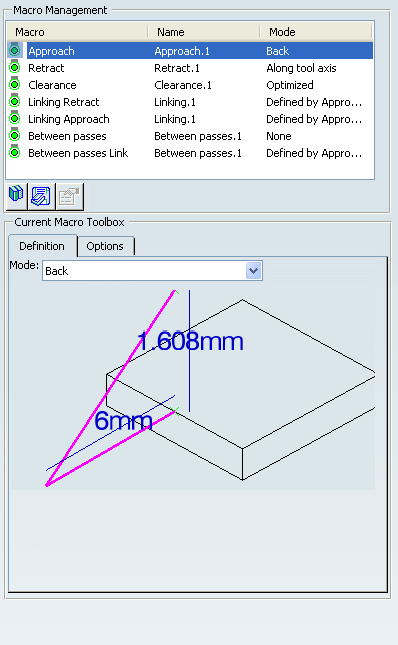
- In the Graphic Mode, using the Build by user macros:
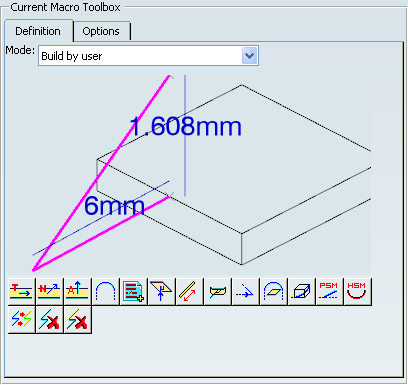
- In the Numeric Mode:
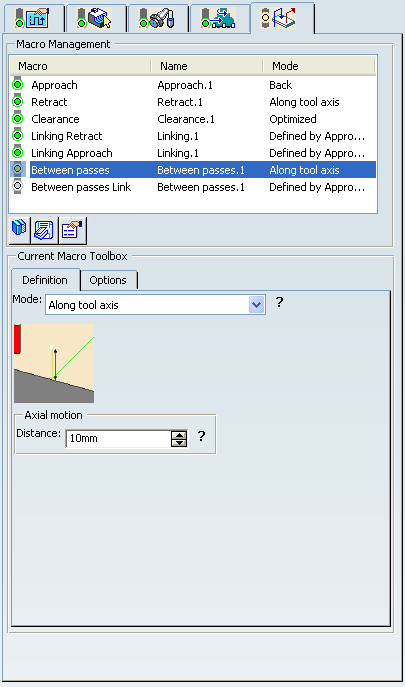
With the cursor in the viewer window of the dialog box, you
can:
- zoom in and out and pan the paths.
- place your cursor on a portion of the macro path ad right click
to display the contextual menu.
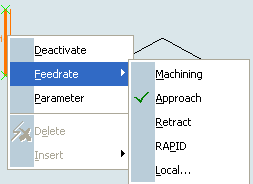 Delete and Insert are available for the
Build by user macros.
Note:
The graph displayed in the viewer of the dialog box is a generic
representation of a macro mode. It is not the true representation
of the macro you are using or defining. To check the result of you
settings, click Tool Path Replay.

Macros Parameters
You can define macros with the following parameters.
Normal The tool moves in a direction perpendicular to the surface being
machined ( Perpendicular
motion), for a given Distance,
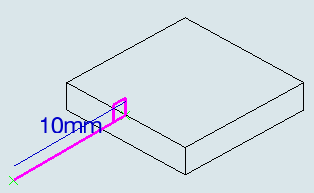
In Graphic Mode, double-click the magenta line to edit the
distance in the Perpendicular motion,
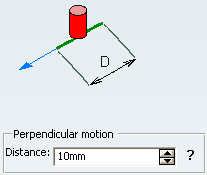
In Numeric Mode, type the Perpendicular motion
Distance.
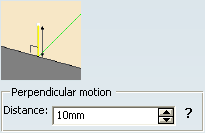
None No approach nor retract macro is applied.
Note:
when this macro is selected on Approach or
Retract, no Link to Safety Plane is added, as shown
below.
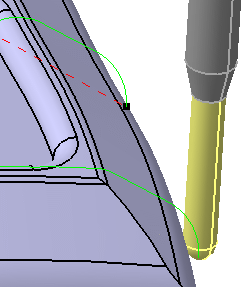
If you require a Link to Safety Plane, select Along tool
axis with an Axial motion Distance value equal to
0 mm. This is what you will get:
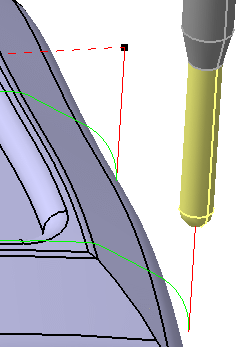
(This is not available with an Isoparametric Machining Operation.)
Back The tool doubles back like an arrow above the cutting tool path
(Back motion).
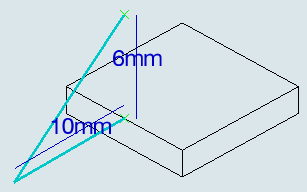
You can either define this type with a Distance
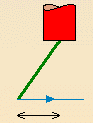
and a Height.
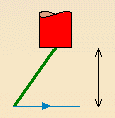
In Graphic Mode, double-click the magenta line to edit the
Distance and the Height.
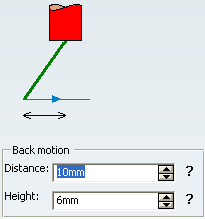
In Numeric Mode, type the Distance and the
Height.
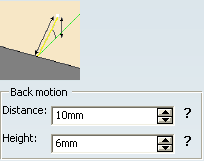
Note:
When you type a Distance higher than the cutting tool
path to which the macro refers, a tool path Along Tool
Axis is added, its length being equal to the difference
between Distance and the length of the cutting tool
path.
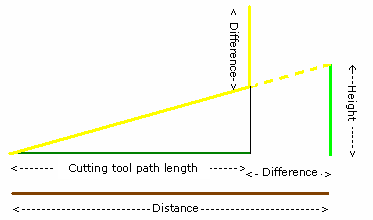
Circular The tool moves towards/away from the part in an arc (circular
motion).
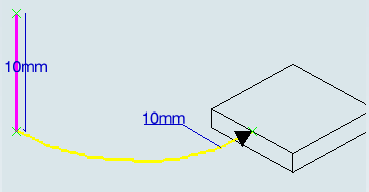
The following conventions apply:
- For the Radius:
Given the spindle axis as shown in the picture,
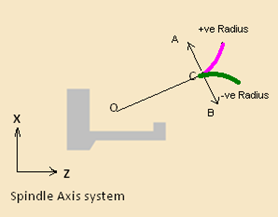 the line OC can be the toolpath or a macro before the
Circular macro.
- A positive radius (shown as +ve) positions the arc as shown in pink, with the center A to the left of
the line OC.
- A negative radius (shown as -ve) positions the arc as shown in green, with the center b to the right of
the line OC.
Note:
The arcs produced are always smooth with
respect to the preceeding line meaning such a case is not valid:
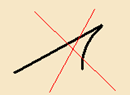
- For the Angular sector with a positive radius: Given the spindle axis as shown,
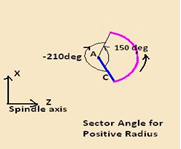 a positive Angular sector (+ ve ) produces an anticlockwise direction of the circular arc for the Retract macro and a clockwise direction of the circular arc for the Approach macro.Note:
For a positive radius, all the negative
angles are converted to the equivalent positive angles. The picture shows an
example for 150 degrees and -210 degrees. Since here
-210 is equivalent to +150, the arc produced in both these
cases is essentially the same (the pink arc).
- For the Angular sector with a negative radius: Given the spindle axis as shown,
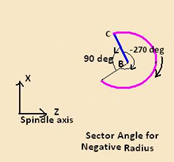 a negative Angular sector (- ve ) produces a clockwise direction of the circular arc for the Retract macro and an anticlockwise direction of the circular arc for the Approach macro.Note:
For a negative radius, all the positive
angles are converted to the equivalent negative angles. The picture shows an
example for 90 degrees and -270 degrees. Since here
90 is equivalent to -270, the arc produced in both these
cases is essentially the same (the pink arc).
In Graphic Mode:
- double-click the arc (yellow line) to edit the circular
motion:
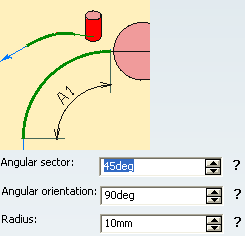
- double-click the magenta line to edit the Axial motion
Distance.
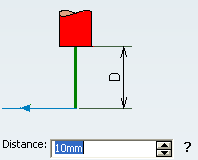
In Numeric Mode, type the Angular sector, the
Angular orientation, the Radius and the
Axial motion Distance.
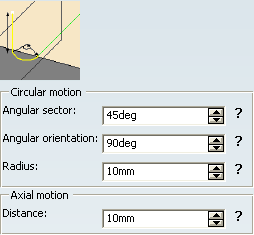
Ramping The tool follows a slope defined by the ramping angle.
The parameters to define are the Axial motion Distance
and the Ramping angle.
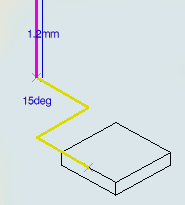
In Graphic Mode:
- double-click the magenta line to edit the Axial motion
Distance:
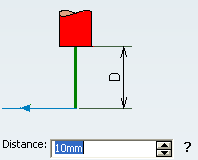
- double-click the yellow line to define the Ramping
angle:
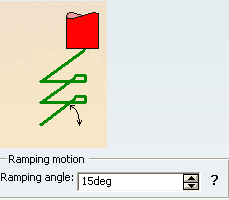
In Numeric Mode, type the Ramping angle and the
Axial motion Distance.
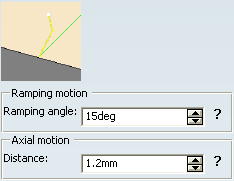
Ramping up to Plane The tool follows a slope defined by the ramping angle up to a plane. In Sweep Roughing,
Sweeping, 4-Axis Curve Sweeping, Pencil, Contour Driven Machining, Spiral
Milling, Multi-Axis Spiral Milling, and Multi-Pockets Flank
Contouring Machining Operations, the slope no longer goes down when the tool
path does and prevents plunges into the material. The parameters to define are the Angle and the plane.
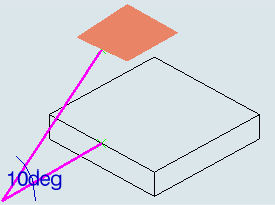 In Graphic Mode, double-click the Angle to define it:
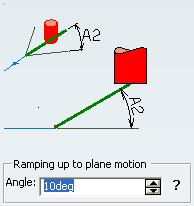 and click the plane to select one.
In Numeric Mode, enter the Angle:
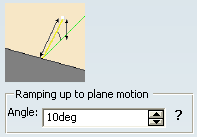
Circular or Ramping The tool uses either circular or ramping mode depending on
whichever is best adapted to the part being machined.
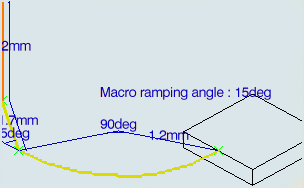
The Circular or
ramping motion is defined by:
- Angular sector,
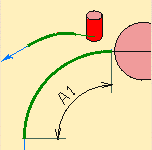
- Angular Orientation,
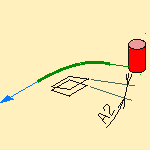
- Radius,
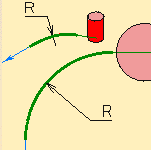
- Ramping angle,
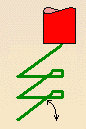
The Prolonged motion is defined by:
- Length,
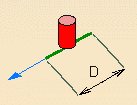
- Angle,
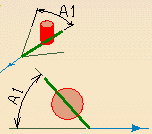
In Graphic Mode:
- double-click the orange line to edit the Axial motion
Distance:
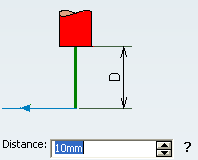
- Double-click the inclined yellow line to edit the
Prolonged motion:
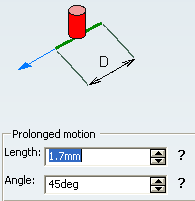
- Double-click the arc to edit the Circular or ramping
motion:
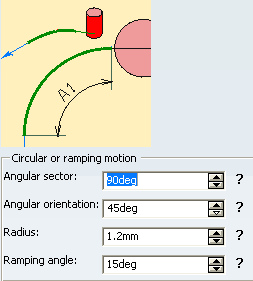
In Numeric Mode, type:
- the Angular sector, Angular Orientation, Radius, and Ramping
angle for the Circular or ramping motion
- Angular sector
- Angular Orientation
You can tilt the plane of circular motion in Approach macro, Retract macro, linking Approach, linking Retract, and Between passes. This provides better control of the tool motion to ensure longer lifecycle for the tool and smoother surface quality. The Angular Orientation parameter corresponds to the tilt
angle and the tilted arc is represented with
GOTO points in the NC output. Since the motion is not in the plane
perpendicular to the tool axis, the circular interpolation
(G41/G42) cannot be generated.
By default,
Angular Orientation is set to 0, the plane is
perpendicular to the tool axis. Allowed values are between 0 and 90 degrees.
Note:
Angular Orientation exist for circular or ramping macro mode only for ZLevel and Advanced Finishing Machining Operations.
- the Length and Angle for the
Prolonged motion and
- the Axial motion Distance.
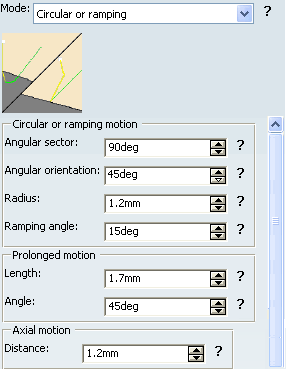
Box The tool moves across the diagonal of an imaginary box (Box motion), either
in a straight line or in a curve (Linking
mode).
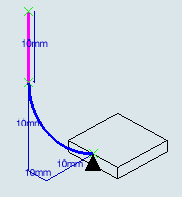
The Box motion is defined by:
- the Distance along
the tangent,
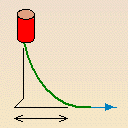
- the Distance
along the tool axis (can be a negative value),
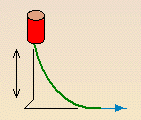
- the Distance
along the normal axis,
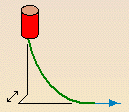
- the direction of the box diagonal that is defined by whether
you want to use the normal to the left or the right of the end of
the tool path (Side of normal
axis). Left or Right is determined
by looking along the tool path in the direction of the
approach/retract.
- the Linking mode (Curved or
Straight).
The Axial motion Distance is the distance that the
tool will move in once it has crossed the box.
- Distance along the tangent,
- Distance along the tool axis,
- Distance along the normal axis.
In Graphic Mode:
- double-click the magenta line to edit the Axial motion
Distance:
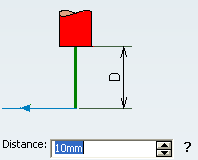
- double-click the arc (yellow line) to edit the Box
motion:
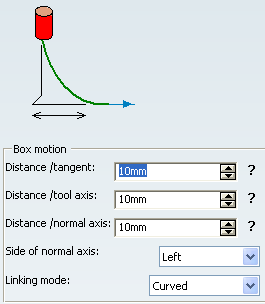
In Numeric Mode:
- type the values of the Distance/tangent,
Distance/tool axis, Distance/normal axis, and
of the Axial motion Distance.
- choose from the list which side of the normal axis will
determine the direction of the diagonal of the box.
- select a Linking mode (Curved or
Straight).
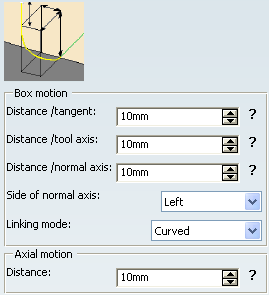
Prolonged Movement The tool moves in a straight line that may slant upwards.
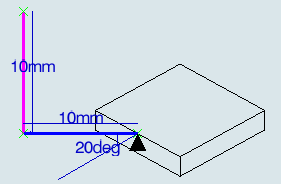
The Prolonged motion is defined by:
- the Distance,
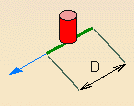
- the Vertical angle,
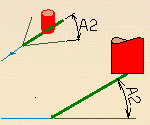
- the Horizontal angle,
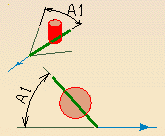
The Axial motion is defined by the
Distance.
The advantage of this mode is that collisions are automatically
detected. In the event that a possible collision is detected, the
angle will be adjusted to avoid collision. If the angle cannot be
adjusted (because of the shape of the part, for instance), the
length of the prolongation will be automatically adjusted to avoid
collision.
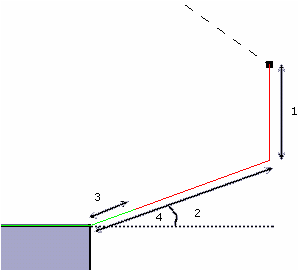
In Graphic Mode:
- double-Click the magenta line to edit the Axial motion
Distance:
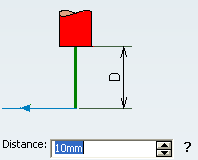
- double-click the yellow line to edit the Tangent
motion:
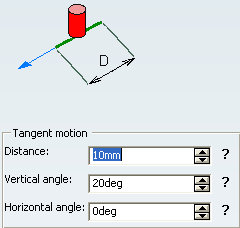
In Numeric Mode, type the Distance, the Vertical
angle, the Horizontal angle and the Axial motionDistance.
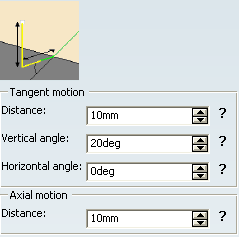
High Speed Milling
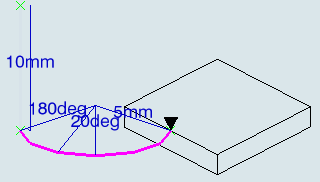
The parameters are:
- Axial motion Distance,
- Transition radius which is the radius of the arc
that goes to the pass.
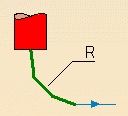
- Discretization angle which is a value which, when reduced, gives a smoother tool path.
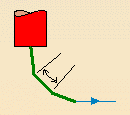
- Transition angle which is a angle of the arc that goes to the pass.
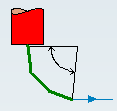
In Graphic Mode:
- double-click the magenta line to edit the Axial motion
Distance:
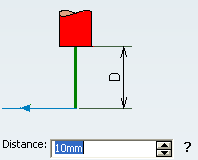
- double-click the green arc to edit the High Speed Milling
motion.
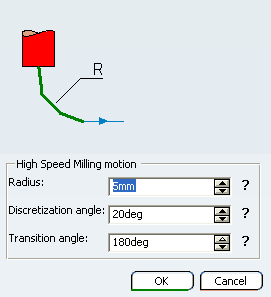
By default,
the angle value is 180 degree.
The Transition angle value lies between 0 and 180 degree. The old
Machining Operations containing HSM macro will not be changed if the default
value is kept.
In Numeric Mode, type the Radius,
Discretization angle, and the Transition angle defining the High Speed
Milling motion, and the Axial motion Distance.
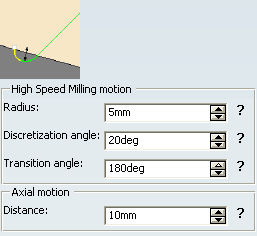
Defined by Approach/Retract, Defined by Approach The macro used for the Linking Retract, Linking Approach or Between passes Link is that used for the Approach or the Retract.
Build by user Available in Graphic Mode only.
Add several predefined
macros to create a machining path.
The current one is colored magenta.
If necessary, double-click:
- the line representing the macro to edit its parameter,
- the associated geometry representation to edit this
geometry.
We have listed below:
- the icons,
- the name of the macros,
- the representation of the macros,
- the corresponding edition dialog box.
A contextual menu is
available:
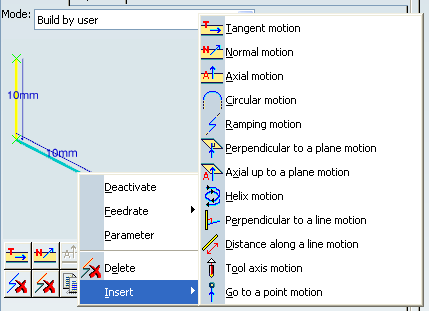
- Deactivate
- Deactivates the selected
macro path.
- Activate
- Activates a path that was
previously deactivated.
- Feedrate
- Allows you to modify the feedrate type associated to the selected macro path by making a selection in the sub-menu. If Local is selected, you can
assign a local feedrate value.
- Parameter
- Launches a dialog box to tune up the macro parameters, e.g.
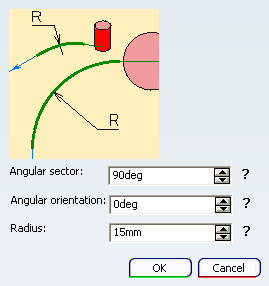 .
Note:
The parameters dialog box can also be launched by
double-clicking a portion of the path in the viewer.
- Delete
- Deletes the current macro path.
- Insert
- Inserts another macro path.
The following macros are available:
Straight The tool goes directly to the next path.
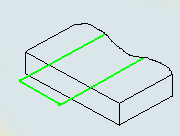
ClearanceFor all clearances, if no safety plane is defined, the safety plane
is the upper point of the part.
- Optimized
- This means that if no obstacle is detected between two passes,
the tool will not rise to the safety plane (because it is not
necessary) and the Machining Operation will take less time. In some cases
(where areas of the part are higher than the zone you are machining
and when you are using a safety plane), the tool will cut into the
part. When this happens, choose another clearance mode.
In both modes, you can only edit the Distance
parameter by double-clicking the label.
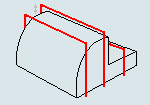
- Clearance Along Tool Axis
- The tool moves up to the defined safety plane along the tool
axis.
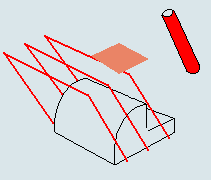
- Perpendicular to Safety Plane
- The tool moves up to the defined safety plane along an axis
perpendicular to the safety plane.
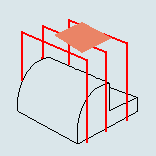

Options
This tab proposes clearance options.
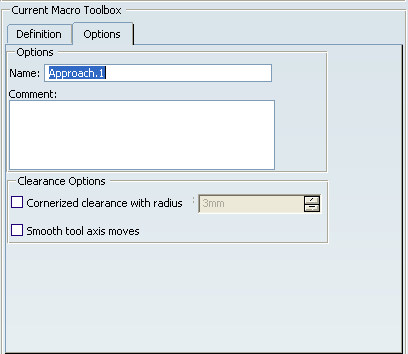
Cornerized
clearance with radius
creates a cornerized clearance and enter the
value of the corner radius.
Smooth tool axis
moves if the approach and the retract axes are different,
adds points on the rapid motion in order to smooth
the transition path.
The tool axis is interpolated, according to the Max
discretization angle.
|