Activate the Manufacturing Program and click Sequential Turning
in the Lathe Machining Operations toolbar.
A Sequential Turning entity is added to the Manufacturing Program. The Sequential Turning operation dialog box appears with the
Geometry tab
.
Select the Strategy tab
.
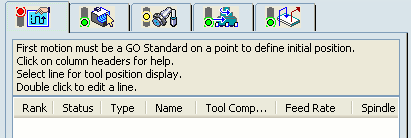
Still in the Strategy tab
.
- Select Go
and define the first motion parameters.
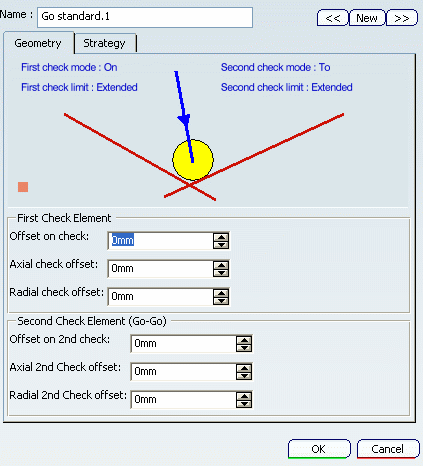
Note:
The first motion must be a Go motion to a point.
- Click check representation (Red lines) in the Geometry tab to select desired check element in the 3D view.
- Click OK to define the motion.
- Select Go
again to define the second
motion parameters.
- Successively select the check representation in
the Geometry tab and select the desired check elements in the 3D
view.
- Set the first and second Check Modes to To.
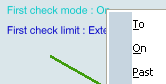
- Set a Offset on Check to 2mm for first check element.
- Click OK to define the motion.
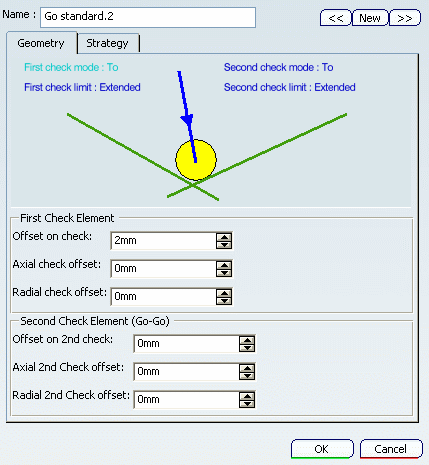
- Select Go
again to define the next motion.
- Click check representation in the Geometry tab and then select
the desired check element in the 3D view.
- Set the Check Mode to Past.
- Set a Offset on Check element to 5mm.
- Click OK to define the motion.
- Select Go InDirv
.
- Select the drive direction in the Geometry tab then the
desired linear element in the 3D view.
- Select a check representation in the Geometry tab then
select the desired check element in the 3D view.
- Set the Check Mode to To.
- Click OK to define the motion.
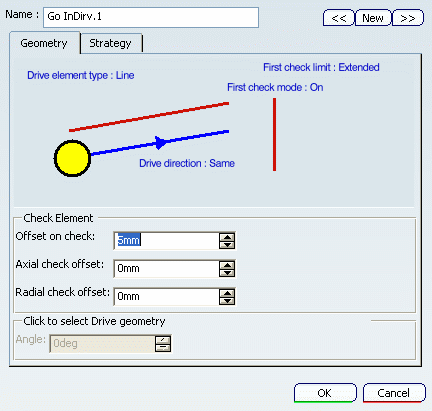
- Select Follow
. The check curve of
the previous motion is used as drive curve. This drive element is highlighted
in the 3D view
- Select a check representation in the Geometry tab and then select
the desired check element in the 3D view.
- Set the Check Mode to To.
- Click OK to define the motion.
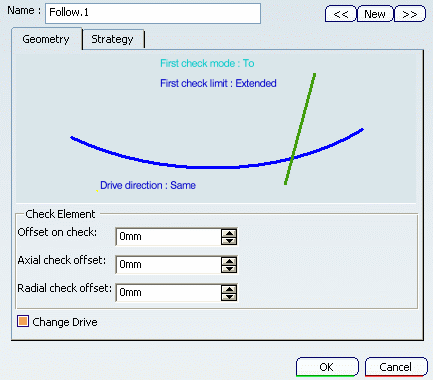
- Select PP Word
,
then specify a PP word (DELAY/5, for
example) in the dialog box that appears.
- Select Go Delta

- Set the check mode to Line and distance in Geometry tab.
- Select the line representation in the dialog box
then the desired linear element in the 3D view.
- Enter a distance.
- Click OK to define the motion.
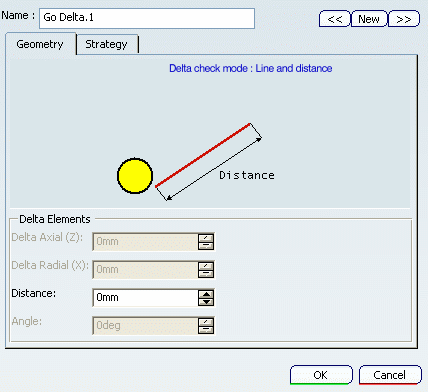
The defined motions are shown below.
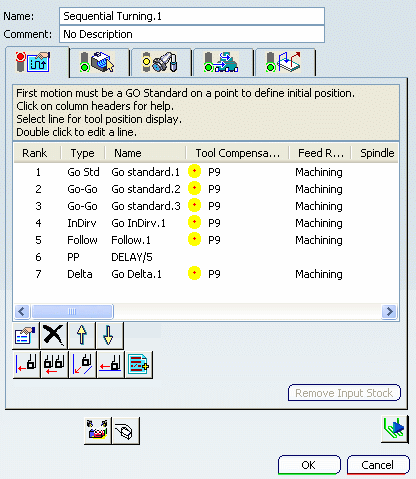
Right-click any motion to access the contextual menu.
- Column Order: Allows to change the header column order with Up and Down buttons.
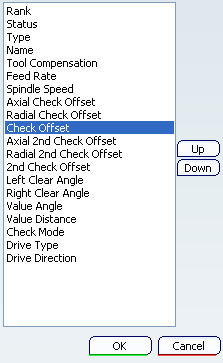
- Column Filter: Allows to filter the header columns.
- Properties: Allows to modify the selected motion.
- Delete: Removes the selected motion.
- Cut: Cut the selected motion.
- Copy: Copy the selected motion.
Go to the Tool tab
to select a tool.
See Specifying a Tool Element in a Machining Operation
Select the Feeds and Speeds tab
to specify the feedrates and spindle speeds for the Machining Operation.
Select the Macros tab
to specify the operation's transition paths.
See Define Macros on a Lathe
Operation for more information.
Click Tool Path Replay
to check the validity of the Machining Operation.
See Replaying the Tool Path
- The tool path is computed.
- A progress indicator is displayed.
- You can cancel the tool path computation at any moment before 100%
completion.
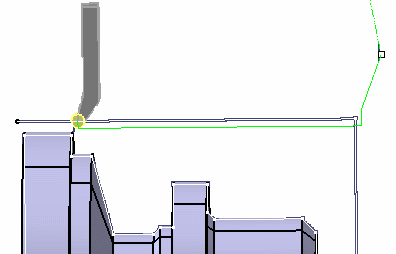
Click OK to create the Machining Operation.