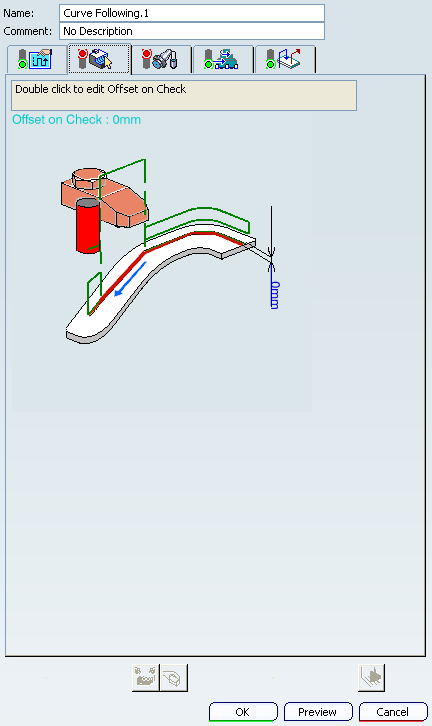
Machining Strategy Parameters
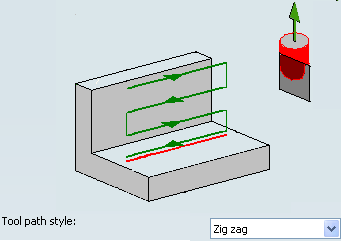
- Tool path style
- Specifies tool path style.
The options in the
Tool path style dropdown combo box are as follows:
- Zig Zag: the machining direction is reversed from one path
to the next
- One way: the same machining direction is used from one
path to the next.

Machining Parameters
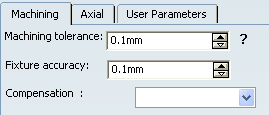
- Machining tolerance
- Specifies
the maximum allowed distance between the theoretical and computed tool
path.
- Fixture accuracy
- Specifies a
tolerance applied to the fixture thickness.
- If the distance between the
tool and fixture is less than fixture thickness minus fixture accuracy, the
position is eliminated from the trajectory.
- If the distance is greater, the
position is not eliminated.
- Compensation
- Specifies the tool
corrector identifier to be used in the operation. The corrector type (P1, P2, P3, for example), corrector
identifier, and corrector number are defined on the tool. When the NC data
source is generated, the corrector number can be generated using specific
parameters.

Axial Parameters
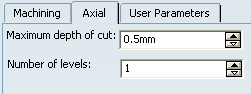
- Maximum depth of cut
- Defines the
maximum depth of cut in an axial strategy.
- Number of levels
- Defines the
number of levels to be machined in an axial strategy.

Geometry
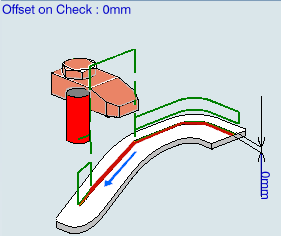
You can specify the following geometry:

Feedrates and Speeds Parameters
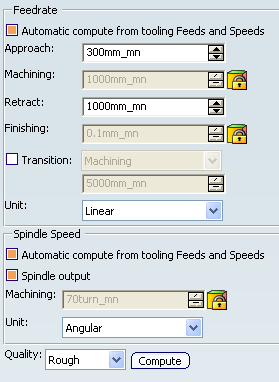
- Feedrate: Automatic compute from tooling Feeds and Speeds
- This check box allow an operation's feeds and speeds values to be updated automatically when the tool's feeds and speeds values are modified.
You can specify the following feedrates:
- Approach
- Machining
- Retract
- Finishing
Note:
The above feedrates can be defined in linear (feed per minute) or angular (feed per revolution)
units.
- Angular: feedrate in revolutions per minute and unit is set to mm_turn.
- Linear: feedrate in feed per minute and unit is set to mm_mn.
- Transition
- You can locally set the feedrate for a transition path to a
machining operation B from a machining operation A or from a tool
change activity. This is done by selecting the Transition check box in the Machining Operation dialog box for
operation B.
For more information, please refer to the Setting a Transition Feedrate.
- Spindle Speed: Automatic compute from tooling Feeds and Speeds
This check box allow an operation's feeds and speeds values to be updated automatically when the tool's feeds and speeds values are modified. If the Feedrate Automatic compute check box is selected
and the Spindle Speed: Automatic compute from tooling Feeds and Speeds check box is not selected, then only the feedrate values can
be computed. If both are not selected then automatic updating
is not done.
When you modify a tool's feeds and speeds, all existing
operations with the Automatic
compute check boxes selected that use this tool (or an
assembly using this tool) can be recomputed.
- Spindle output
- This check box manage output
of the SPINDL instruction in the generated NC data file:
- If the check box is selected, the instruction is generated.
- Otherwise,
it is not generated.
Note:
Spindle speed is applied on the different
motions of the operations (including approach, retract, linking
macros). Spindle can be re-defined with Spindle tool motion. The spindle speed can be defined in linear (length per minute) or angular (length per revolution)
units.
- Angular: length in revolutions per minute and unit is set to mm_turn.
- Linear: length in feed per minute and unit is set to mm_mn.
- Quality
- The feed and speed values are computed according to the
Quality setting on the operation.
- Compute
- Feeds and speeds of the operation can be updated according to tooling feeds and speeds by clicking the Compute button located in the Feeds and Speeds tab of the operation.
Feeds and speeds of the operation can be updated automatically
according to tooling data and the Rough
or Finish quality of the operation. This is described
in
About Feeds and Speeds.

NC Macros
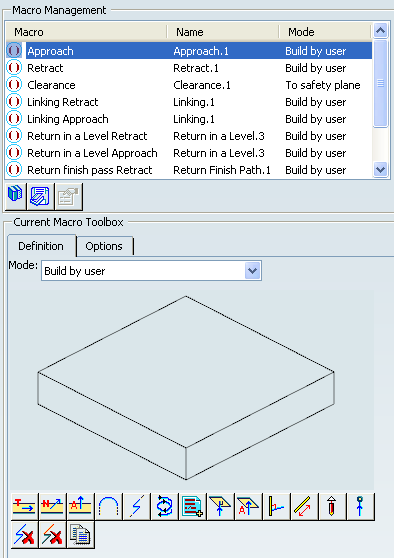
You can define transition paths in your machining operations by means
of NC macros:
- Approach: to approach the operation start point,
- Retract: to retract from the operation end point,
- Return between Levels
to go to the next level in a multi-level machining operation,
- Clearance to avoid a fixture,
for example.
The proposed macro mode for Approach and Retract macro are:
- None
- Build by user
- Horizontal horizontal axial
- Axial
- Ramping
The proposed macro mode for Clearance macro are:
- Distance
- To a Plane
- To safety plane
For more information, please refer to the Defining Macros.
|