Open the flattened
document.
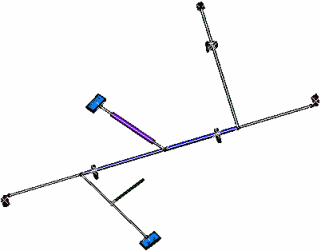
Switch to the
Drafting workbench and open a new drawing document.
Click Front View
and select the top-face of the rectangular connector as Plane.
The drawing document updates according to this choice.
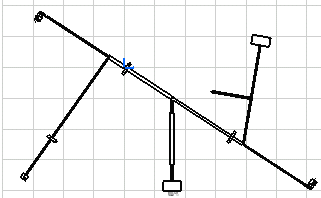
Click Automatic
Generation
.
The drawing is updated according to the generative view style previously
defined:
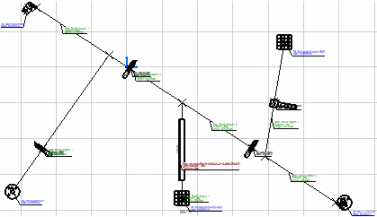
Automatic
Generation options are stored within the GVS. The following
example shows the definition of the segment template, with a predefined
type of text template:
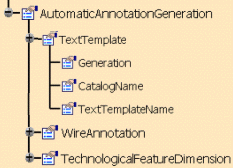
Text Templates are generated on:
-
segments
-
protective
coverings
-
supports
-
connectors
(single insert connectors, ground studs, internal splices, external
splices, terminal strips and terminal blocks)
-
Backshells
Wire
Annotations are generated on:
- Segments
- connectors
(single insert connectors, ground studs, internal splices, external
splices, terminal strips and terminal blocks)
Support
Sections are generated on:
-
a ditto
for each support section, with
-
appropriate
labels on the support itself and on the section for easy identification.
2D Clocking View is generated for:
- Backshell and SIC relative orientation
Text
Templates, Conductor Annotations , Support Sections
and 2D Clocking View are defined in the GVS. They are placed at a default location but can be
moved for better legibility or presentation. To do so: - Drag the
annotation you want to move:
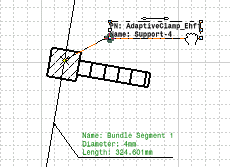
- Release
the mouse button when you are satisfied with the new position.
If you modify
the original 3D document for example to: - Change
a segment diameter
- Change
a connector / device position
- Add or
remove a branch, etc.
You will need
to update the drawing. To do so: - First
click Synchronize
to
reflect the modifications of the geometry on the flattened document.
For more information, please refer to
About Synchronization.
- Then
click Update Current Sheet
to reflect the modifications of the geometry on the drawing.
- Finally
click Update Dress-up
to:
|