You can define the law that will be used to create the multi-sections surface.
But first, let's open the Generative Shape Design workbench.
In our example, three sketches with closed contours have been created
and filled. A spine between these sections have been created:
Click Measure
to compute the geodesic length of the spine:
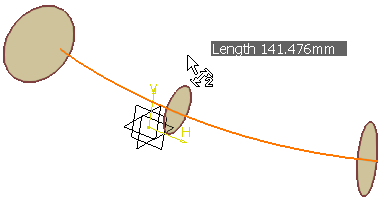
Click Split
to split the spine by the section plane.
Click Measure
again to compute the geodesic length of the resulting curve:
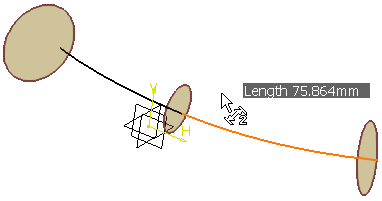
Using the Sketcher, create a line and a curve corresponding
to the previous computed lengths.
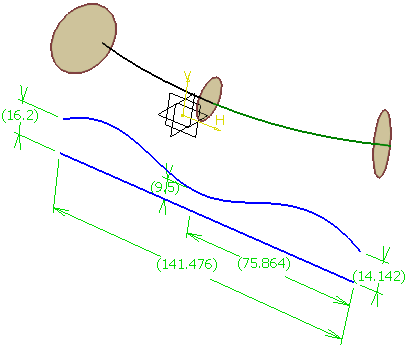
Click Extract
to create separate elements of the line and curve.
Click Law
to create the law from the previously extracted elements.
In the Law Definition dialog box, select
the Reference line and the Definition curve.
Click OK to create the law.
Click Multi-sections Surface
.
The Multi-sections Surface Definition dialog box appears.
Select the sketches as the planar section curves.
Select the Area law tab.
In the Law field, specify the length law
to be used to control the section area.
Here, select the law we have just created.
The Intermediate sections deviation option
only applies to intermediate sections (unlike the Deviation
option that applies to the sections extremities) and is homogeneous
with the selected law. It specifies the deviation of the length law
to be applied to the intermediate sections in order to smooth the resulting
shape
Click OK to create the multi-sections surface.
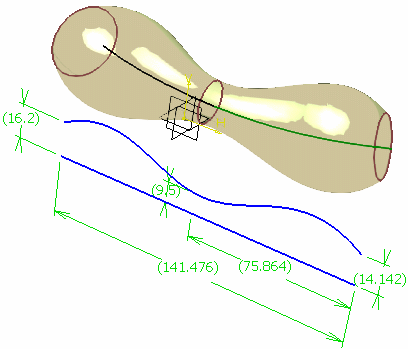