Cutter Compensation Options
The Cutter Compensation: None / On / Reverse option is proposed
for finish operations. If this option is set to On or Reverse, the NC output
can include CUTCOM instructions in the APT or clfile output for cutter
compensation (CUTCOM/RIGHT, CUTCOM/LEFT, CUTCOM/OFF).
- On: CUTCOM/RIGHT instruction generated if tool is to
the right of the tool path and CUTCOM/LEFT if tool is to the left of
the tool path
- Reverse: CUTCOM/RIGHT instruction generated if tool is
to the left of the tool path and CUTCOM/LEFT if tool is to the right
of the tool path.
- None: If the option is set to None, no CUTCOM instruction
can be included in the NC data output.
A CUTCOM instruction is always generated before a linear trajectory in
order to be active on that displacement:
- for a tool approach, the instruction CUTCOM/RIGHT or CUTCOM/LEFT
is generated at latest in the approach phase of the trajectory, before
the lead-in and on a linear trajectory.
- for a tool retract, the instruction CUTCOM/OFF is generated at earliest
in the retract phase of the trajectory, before a linear trajectory or
the last point of the operation.
The figure below illustrates a Profile Finishing operation that has circular
lead-in and linear lift-off.
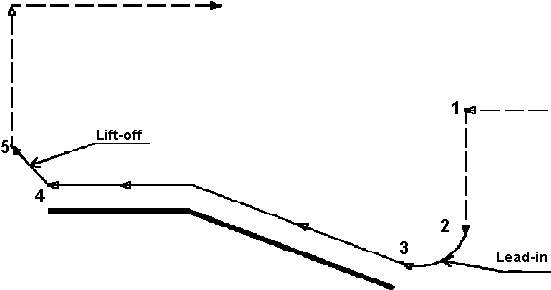
If the cutter compensation is set to ON, the CUTCOM instructions are
generated as follows:
- CUTCOM/RIGHT is generated at point 1, before the tool motion to
point 2.
Note that if lead-in was linear, CUTCOM/RIGHT is generated at
point 2, before the tool motion to point 3.
- CUTCOM/OFF is generated at point 4, before the tool motion to point
5.
Note that if lift-off was circular CUTCOM/OFF get generated at
point 5, before the linear retract motion.

Set Cutter Compensation Options
The computed tool path corresponds to the trajectory followed by the output
point of the tool used in the Part Operation.
- Set Cutter Compensation to On in the following
cases:
- the cutter radius of the actual tool used for machining is greater
than the radius of the programmed tool and a positive compensation value
is entered at the NC machine.
- the cutter radius of the actual tool used for machining is less
than the radius of the programmed tool and a negative compensation value
is entered at the NC machine.
- Set Cutter Compensation to Reverse in the following
cases:
- the cutter radius of the actual tool used for machining is less
than the radius of the programmed tool and a positive compensation value
is entered at the NC machine.
- the cutter radius of the actual tool used for machining is greater
than the radius of the programmed tool and a negative compensation value
is entered at the NC machine.
We recommend that you should program with tools whose cutter radius is greater
than those that can actually be used on the machine. This helps you
to anticipate tool/part collisions that may arise when cutter compensation
is used.
If negative compensation values are allowed on the machine, set Cutter
Compensation to On.
If negative compensation values are not allowed on the machine set Cutter
Compensation to:
- On, if the tool actually used has a greater cutter radius
than the programmed tool.
- Reverse, if the tool actually used has a smaller cutter
radius than the programmed tool.
The figure below illustrates cutter compensation for profile finishing.
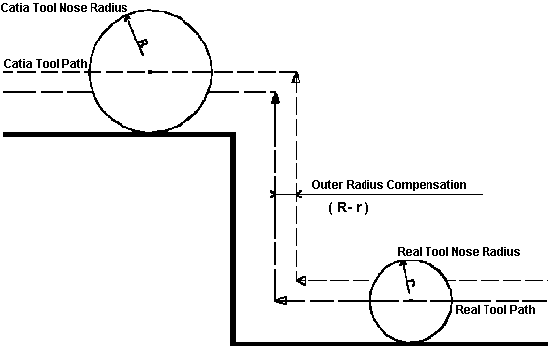