Click
Tool Change Position
on the Machine Building toolbar.
The Tool Change Position Editor dialog box is
displayed.
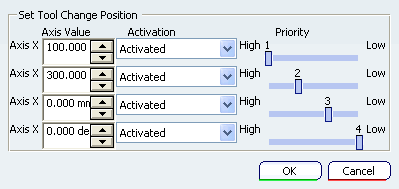
Modify the axis as required in Axis Value frame.
Select Activated or Deactivated for specific parts, in Activation frame.
- Activated: If you select Activated, the axis become activated and participates in simulation.
- Deactivated: If you select Deactivated, the axis become deactivated and does not participates in simulation.
Move the slider bars, on the right side of dialog box, to set the priority for the corresponding axis. Moving the slider bar to the right lowers the axis priority and moving the slider bar to the left increases the priority. The value of the priority appears just above the slider bar. You can set priority values for deactivated axes as well. The priority of an axis is applicable for activated axis during simulation.
Click OK.
|