Click
Harness Flattening Parameters
.
The Harness Flattening Parameters dialog box opens on the
General tab.
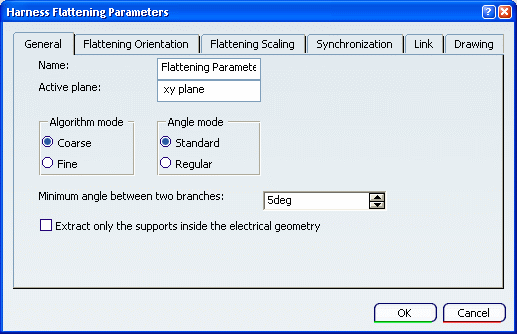
Select the
Active plane, which is the default plane you will be working
with when using the Rotate, Flatten, Roll
, Scale and Straighten functionality.
Select the
Algorithm
mode .
The Algorithm mode has to do with
the different ways you can flatten out a segment. The Coarse
mode is the default algorithm
mode.
- The Coarse mode will roughly straighten the
selected segments, allowing an easy viewing of the segments
you are working on.
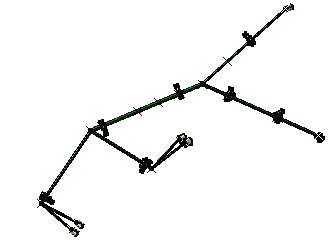
- The Fine mode will
respect the actual shape of the segments as it is in 3D.
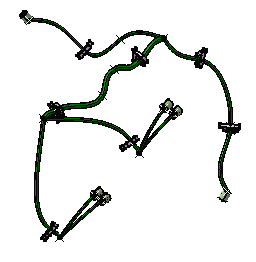
Select the
Angle mode .
Two Angle modes are available. The
Standard mode is the default angle mode.
- Choose the Standard mode in order to keep
the actual angles between the segments as in 3D.
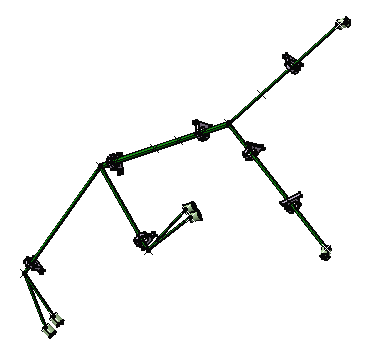
- Choose the Regular mode which calculates
regular angles, if you do not care about respecting the
true angle values.
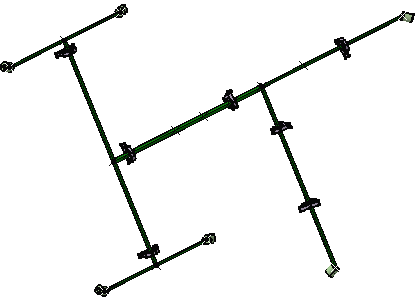
This mode calculates regular angles
in predefined target directions depending upon the number of segments and branches.
It is possible to use Flatten
Harness branch orientation at junction to better match 3D harness design
branch orientation at junction. As an example, let us consider the case
of a model consisting of 2 or 3 branches.
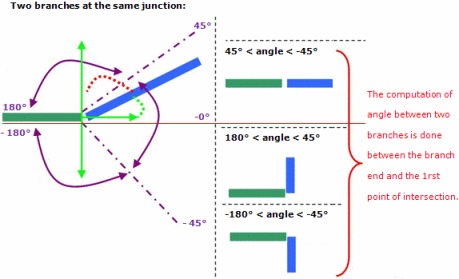
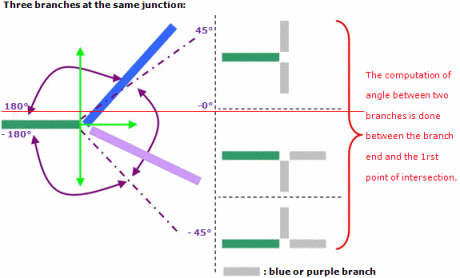
The angle computation between
two branches is only applied in Regular mode.
The branch direction is calculated with the exact tangency at the branch
end (between the branch extremity and the first passing point).
If all the branches' directions
in same junction are different, this computed direction is used to fit
it as possible as with the Regular angle mode.
If there is at least two segments with the same direction, the algorithm is not launched.
Note that during the process of
flattening, if one of the segments being flattened belongs to
the same branch as the segment already flattened, then it will
be aligned to the already flattened segment.
Specify the Minimum angle
between two branches.
During the flattening
process, this minimum angle is applied every time an angle between
two branches is null in the 3D design. That way, segments are
never superposed upon one another and can easily be made out.
If you
want to consider only the supports which belong to the given Electrical Geometry when running the extracting command, select Extract only
the supports inside the electrical geometry. The supports which
do not belong to the Electrical Geometry will not appear in the extracted
data. This option allows you to manage two types of supports:
-
The supports which must be assembled with
the geometry during the manufacturing step.
This type of support is created inside the Electrical Geometry.
-
The supports which are linked to the structure.
These supports are added to the harness during the installation
step.
This type of support is created outside the Electrical Geometry.
By default this option is not selected for consistency
with the previous versions.
Click OK to validate.
Save the new data.
From now on, the parameters you have just selected will be automatically
applied to the other commands available in this workbench. However, when
using a functionality, the dialog box will systematically pop up - with
these parameters already selected - in case you want to modify them.
For the time being, the different commands available in this workbench do
not take into account the segments on surface.