Click Engineering Connection
.
The Engineering Connection dialog box appears.
Select the connection Type to be created.
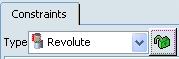
If you select User Defined
,
an appropriate connection type will be assigned to the engineering connection
based on the constraints you apply.
Techniques for creating predefined engineering connection
types are discussed in more detail in
Engineering Connections in the Assembly Design User's Guide.
Assign the driving constraints for the engineering connection.
If you are defining an engineering connection that can
be manipulated using a command in the mechanism representation, you
must define at least one additional controlled constraint:
- Select the geometry supports for the constraint. Controlled
constraints can be created only between lines, points, and
planes.
-
If necessary, change the type of constraint by right-clicking
the constraint type and selecting Replace from
the menu that appears. The controlled constraint must be
either an Angle or an Offset.
- Right-click the constraint Mode, and select
Controlled from the menu that appears.
The Value column is updated automatically
based on the current configuration of the model. This value
determines the initial configuration of the mechanism.
- Double-click the Lower and Upper
columns to define the lower and upper value limits for the
controlled constraint.
Lock any engineering connections that have a predefined type with controlled
constraints
to
include them as specifications for your mechanism.
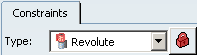
Unlocked engineering connections can still be used to enforce driving constraints
in a mechanism, but controlled constraints in an unlocked engineering
connection cannot be used as commands in a mechanism.
Click OK.
The engineering connection is created and identified in the specification
tree.