Simulation at

- Program level/Part operation level
- Select the desired option to perform material removal simulation at either
Manufacturing Program or Part Operation level. Depending on the selected level, simulation begins either from the start
of the Manufacturing Program or from the start of the Part Operation .
Note:
Best performance is obtained with program level.
By default,
the Program level option is selected.

Video
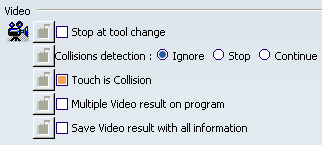
- Stop at tool change
- When selected, stops the Video
simulation each time a Tool Change is encountered in the program.
By default,
this check box is not selected.
- Collision detection
- Select the desired Collisions detection option to:
- Ignore collisions during the Video simulation
- Stop the Video simulation at the first collision
- Continuethe Video simulation even when
collisions are detected. In this case, you can consult the list of collisions
at any time during the simulation.
Note:
Best performance is obtained when collisions are ignored.
By default,
the Ignore option is selected.
- Touch is collision
- When selected, detects collisions of type touch
(or contact).
By default,
this check box is selected.
- Multiple Video result on program
- When selected, stores video results on more than one operation in the program.
By default,
this check box is not selected.
- Save Video result with all information
- When selected, saves a video result with geometrical information and all extra information such as collisions, cut information, material etc.
By default,
this check box is not selected.

Photo
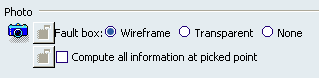
- Fault box
- Select the desired Fault box type for examining remaining
material or gouges:
- Transparent: to display a transparent bounding box
- Wireframe: to display a wireframe bounding box
- None: if no bounding box is required.
By default,
the Wireframe option is selected.
- Compute all information at picked point
- When selected, computes all information at the picked point.
Note:
Best performance is obtained when:
- Fault box is set to
None
- and the Compute all information at picked point check
box is not selected.
By default,
this check box is not selected.

Other Color
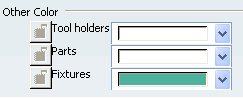
- Tool holders/Parts/Fixtures
- Let you assign colors to tool holders, parts, and fixtures from the lists.

Positioning Move

- Maximum tool axis variation
- Lets you set the maximum tool axis variation allowed
between the end point of an operation and the start point of the next operation.
Note:
If the tool axis varies by an amount greater than the specified value, the tool is positioned at the start of the following operation.
By default,
this angle is set to 1 degree.
|