General
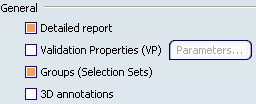
-
Detailed report
- When selected, includes the Detailed report this
chapter in the report file.
By default,
Detailed report is selected.
- Validation Properties (VP)
-
Note:
In the Data Exchange Interfaces User's Guide read:
- About Validation Properties
- License Requirements for STEP
Once you have activated this option, Validation Properties (VP) become active and Parameters becomes available. It starts the Parameters for Validation Properties dialog box:
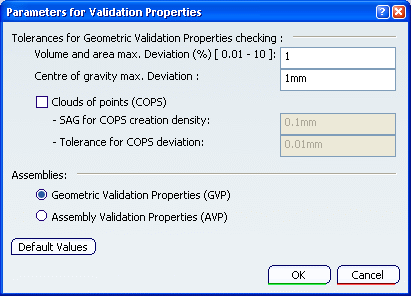 In this dialog box, you can:
- activate Geometric Validation Properties (GVP) or Assembly Validation
Properties (AVP) according to your needs,
- activate the Clouds of points (COPS) functionality (This functionality involves a slight performance loss, due to
the properties computation cost.)
- define the tolerances for the
validation properties checking.
Tolerances for Geometric Validation Properties
checking detect large errors during exchanges by comparing the centre
of gravity, the volume and the area of the exchanged solids with
their native properties:
- Volume and area max. Deviation
is a percentage of variation of volume or area allowed.
By default,
the value is set to
1%.
- Centre of gravity max. Deviation
is the maximum error for the center of gravity.
By default,
the value is set to 1m.
SAG for COPS creation density controls the density of the cloud of points generated for each
face; the cloud of point is created by tessellating the face
according to the given SAG: a low value of SAG means a large number
of points by face and a high value of SAG means few points by
face. The SAG must be defined between 0.01 and 10.
By default,
the value is set to 0.1
mm.
Tolerance for COPS deviation is the largest allowed gap between a point and the imported face.
With a standard scale, the deviation must be defined between the
following bounds 0.0001 and 0.1.
By default,
the value is set to is 0.01
mm.
Default Values reverts to the default values.
By default,
- the option Validation
Properties (VP) is not selected.
- In the Parameters dialog box:
- Volume and area max. Deviation is 1,
- Centre of gravity max. Deviation is 1 mm
- the option Cloud of points (COPS) is not
selected.
- SAG for COPS creation density is 0.1 mm.
- Tolerance for COPS deviation is 0.01 mm.
- the option Geometric Validation Properties
(GVP) is selected.
- the option Assembly Validation Properties
(AVP) is not selected.
- Groups (Selection Sets)
-
When this check box is selected:
Note:
Importing or exporting Groups may be time consuming.
By default,
Groups (Selection Sets) is selected.
- 3D Annotations
-
Note:
In the Data Exchange Interfaces User's Guide read:
- About 3D Annotations
- License Requirements for STEP. In addition to those requirements, this functionality requires Application Protocol AP203 ed2 (it follows the recommended Practices for Geometric Dimensions & Tolerances (GD&T) for Polyline Representation.
When selected, this option enables the import and export of 3D annotations. Information about the annotations is found in the report file.
By default,
3D Annotations is not selected.

Import - Continuity optimization of curves and surfaces
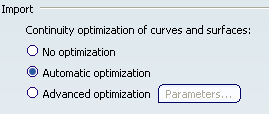
This setting allows a better user control over the number of
curves and surfaces that are created during the process of
importing STEP data into V6:
- V6 requires its geometry to be C2-continuous. When non
C2-continuous geometry must be imported from a STEP file, this
geometry (curves, surfaces) is broken down into a set of contiguous
geometries, each of them being C2-continuous. This is what happens
when the No Optimization option is chosen.
- However, this can produce an increase of the size of the
resulting data, because more curves/surfaces are created. In order
to limit this drawback, two other modes are optionally
offered.
- In those modes, the STEP interface tries to limit the splitting
of curves and surfaces by modifying their shape slightly, so that
they become C2-continuous while remaining very close to their
original shape.
- In order to guarantee that the deformation is not excessive, a
maximum deviation (tolerance) parameter is used. When in
Automatic optimization mode, this maximum deviation is
read into the STEP file itself, in the STEP parameter that
documents the precision of points in the file. In this mode, the
value read from the STEP file is then corrected so that it remains
comprised between 10E-2 and 10E-3. This guarantees an optimization
that remains compatible with the precision for the data that was
set by the emitting system.
- Last, if this strategy is not enough, you can choose the
Advanced optimization mode, in which an arbitrary
deviation value can be entered.
Select the desired option:
- Automatic optimization
This option proposes no approximation, thus it does not create a
significant deformation and keeps the internal BSpline structure
(equations and knots). A continuity optimization is performed within the deformation
tolerance used for optimizing BSplines, comprised between 0.001mm
and 0.01mm (depending on the tolerance value defined within the
imported STEP file) on:
- BSpline surfaces,
- BSpline boundary curves (3D and P-curves when available),
- BSpline independent 3D curves,
The parameters box cannot be activated.
This option softens the effect C2 cutting of faces and
boundaries (which is mandatory in V6) without any significant
geometric deformation
- Advanced optimization
- No approximation is performed. The internal BSpline structure (equations and knots) is kept. A continuity optimization is performed on:
- BSpline surfaces,
- BSpline boundary curves (3D and P-curves when available),
- BSpline independent 3D curves,
but the deformation tolerance is set by the user.
With this option, you can enter a larger tolerance value which may
enhance the optimization impact (resulting in less C2 cutting on
faces).
- No optimization
-
No optimization is performed on BSplines (neither curves nor surfaces).
Elements are cut at discontinuity points to suit the modeler (exact mathematic continuity). This may result in a dramatic number of faces and boundary curves, data of poor quality and poor performances in further use in V6.
By default,
Automatic optimization is selected.
- Parameters
- When Advanced optimization is selected, Parameters gives access to advanced optimization options and tolerances.
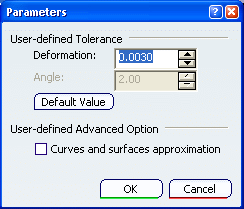
Deformation: maximum deformation (in millimeter)
allowed in the optimization of curves and surfaces. Ranges between
0.005 and 0.1 mm.
By default,
Deformation is set to 0.003. Angle: angle (in degree) below which contiguous
elements can be merged. Ranges between 0 and 10 degrees.
By default,
Angle is set to 2. Default Value reverts to the default values.
Curves and surfaces
approximation: BSpline surfaces and curves continuity is optimized. In addition, Bspline curves and surfaces approximation is
performed. It is possible to enter a user value for Deformation. This option may change the internal structure of BSplines
(equations and knots). This option usually results in a significant decrease in the
number of faces cuttings.
By default,
Curves and surfaces
approximation is not selected.

Export
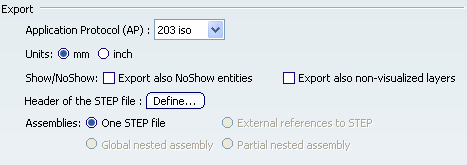
-
Application Protocol (AP)
-
Lets you select the STEP format into which the data will be
exported.
For more information about AP203, AP203 with
extensions, AP203 ed2, AP214 and AP214 ed3, refer to
Reference Information for STEP.
By default,
Application Protocol (AP) is set to AP203 iso.
-
Units
-
Lets you decide whether the data will be exported in mm or inches,
independently of the session unit.
By default,
Units is set to mm.
- Show/NoShow
-
The data to export may be:
- visible entities placed in the Show space,
- hidden entities placed in the NoShow space.
- hidden entities placed in layers that are not visualized.
Note:
Visualization filters are taken into account.
By default,
entities placed in non-visualized layers are not exported.
When Export also NoShow entities is not selected,
only visible entities are exported to STEP.
When Export also NoShow entities is selected, all
entities belonging to both the "Show" and the "NoShow" spaces are
exported, the entities that are in the NoShow space being exported
under the INVISIBILITY STEP entity.
When Export non-visualized layers is selected, all entities belonging to those layers are also exported. Those
entities are not exported under the INVISIBILITY STEP entity.
By default,
Export also NoShow entities nor Export also non-visualized layers are selected.
- Header of the STEP file
- Defines opens the Define Header of STEP File dialog box to help you define this header:
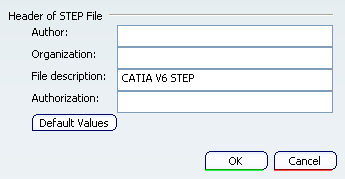
- Assemblies
-
Lets you select the required export mode for assemblies. Note:
In the Data Exchange Interfaces User's Guide read:
- License Requirements for STEP. In addition to those requirements, One STEP file is available for all Application Protocols while External references to STEP, Global nested assembly and Partial nested assembly are available for AP214 and AP203 ed2 as
stated in Recommended Practices for External References, Release
2.1, dated January 2005.
- at export, the check boxes Global nested assembly and Partial nested assembly are dimmed (with AP214/AP203 ed2),
- at import, referenced STEP files of type assembly are not taken into account, only referenced STEP files of type part are taken into account.
Note:
Dynamic Licensing: If you release the STEP license and you access the STEP options
panel, the export assemblies options may change. In this case, when you recover the STEP license, you have to go
back to the STEP options panel to restore the required values.
By default,
Assemblies is set to One STEP
file.
|