Click Bump
in the Advanced Surfaces toolbar.
The Bump Deformation Definition dialog box appears.
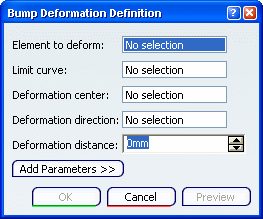
In the Element to deform box, select the curve or the surface to be deformed.
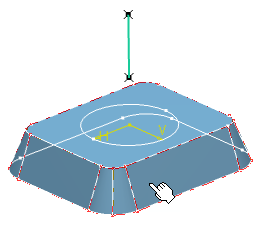
In the Limit curve box, select the limiting curve to
delimit the deformation area.
The limit curve needs to be lying on the element to be deformed.
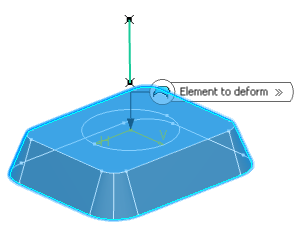
In the Deformation center box, select the
point representing the center of the deformation.
The deviation will be maximum at this point, and evolve
towards the limit curve, where it should reach 0.
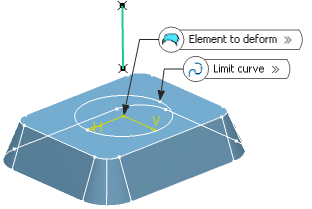
In the Deformation
direction box, select the curve indicating the deformation direction.
The deformation is propagated along this direction. By default,
the deformation direction is normal to the deformed
element.
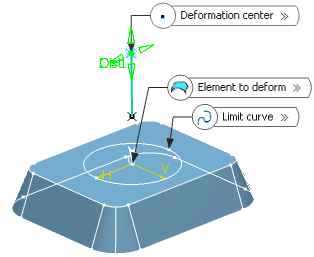
In the Deformation distance box, set the maximum
distance, along the deformation direction, from the deformed
surface towards the deformation center. Here, we entered
20mm.
Click Preview to preview the bumped element.
Click Add Parameters>> to display further options:
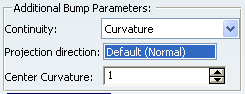
You can:
- Define the continuity to be kept between the deformed area and
the surface outside the deformation area (point, tangent, or
curvature continuity).
- Specify a projection direction if the deformation center
does not lie within the selected element to be deformed, so that it
is projected onto it.
- Define a center curvature value to
control the shape of the bump deformation.
If the value is:
- Equal to 1 (case A), the shape is the default one (as if no
value was defined)
- Smaller than 1 (case B), the shape is flatter
- Bigger than 1 (case C), the shape is steeper.
Note:
All values are allowed (positive, null, and negative
values), however it is advised to define a value comprised between
-1 and 5.
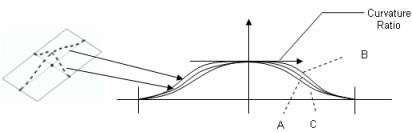
Click OK to validate the element deformation.
The element (identified as Bump.xxx) is added to the
specification tree.
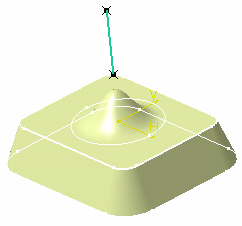
|